Rafael Fernandez-Nespral
Totalwind Legend
Cambio caja de aleta tuttlebox On Crusier 305
Es una tabla en la que reparación y su valor por antigüedad-estado se igualan. Se repara ya que el dueño le gusta esta tabla y como navega.
Por colisión de la aleta con unas rocas, se desprende parcialmente la caja de aleta.
Haciendo un poco de palanca sale la caja, que resulta estar fabricada en fibra de vidrio.
Después de limpiar el laminado adherido veo que esta fracturada y que no es reutilizable. Hay que reponer con una Chinock Tuttlebox de plástico negro.
Esta nueva caja me obliga a fresar en profundidad y en anchura desde carena y cubierta.
Veo que la caja de aleta estaba embutida en un bloque de XPS, que a su vez tiene un cerclaje en PVC de solo 3mm revestido en fibra de vidrio y con algunas grapas metálicas que estaban oxidadas por entrada de agua que llego hasta el núcleo del EPS. Creo que había una vía de agua previa al choque de la aleta, ya que el oxido encontrado en el PVC llevaba mucho mas tiempo actuando.
Presento la nueva caja de aleta.
Relleno la parte superior de la caja (que aproveche en toda su altura interior ya que el grosor de la tabla en popa es superior) con espuma de poliuretano de dos componentes de alta densidad, “enfundo” la caja de aleta con PVC de 5mm en los costados y de 12mm en el fondo y los dos lados: frontal y posterior, pegadas con resina espesada con microbalones y que presiono con sargentos hasta el endurecimiento de la resina.
Vuelvo a fresar el hueco para adaptarlo al ancho y largo de la caja revestida de PVC, lijado interior de las paredes del EPS, preparación de materiales para embutir la nueva caja. “pintado” interior con resina, tapado del poro con resina espesada con microbalones, “pintado”de la caja de aleta con resina, revestido con carbono de 180g en sarga y otro laminado encima en fibra de vidrio de 165gr y embutido hasta dejar a nivel superficial en carena.
Colocación de la aleta para corregir la perpendicularidad de esta con respecto a la carena mediante un nivel láser.
Tras el lijado del exceso el PVC sobrante en cubierta, repongo con doble sándwich en cubierta para conseguir el grosor original con dos capas de PVC de 3mm: Pintado con resina, relleno y nivelado con resina espesada con microbalones, laminado en fibra de vidrio de 165gr, Pieza de PVC de 3mm impregnada con resina, laminado en fibra de vidrio de 80gr, 2ª pieza de PVC de 3mm, cubro con tejido sangrador-pelable PEEL-PLY, manta de absorción, bolsa de vacío (que enfunda carena y cubierta) y compresión mediante bomba de vacío con depresión de 0,7, durante 9 horas con manta de calor durante 4 horas. Reposo hasta endurecimiento de 48 horas.
Lijado del nuevo PVC en cubierta dejándolo a nivel del original, señalado y fresado de los alojamientos de tornillos llegando hasta la superficie de plástico de la caja de aleta, preparación del laminado en carbono y fibra de vidrio del fondo y contorno interior de los alojamientos mediante machos recuperables (en carbono, de una vieja botavara) que se han enfundado con “dedos” cortados de guantes de vinilo, pintados con cera desmoldeante y a los que hemos enrollado los laminados, impreganandolos con resina, recorte en círculos de laminados en fibra de vidrio y carbono que asentaran en el fondo de los alojamientos de tornillos
Pintado con resina de los alojamientos, relleno con resina espesada con microbalones, inserción del laminado del fondo y el de los machos con el laminado a su alrededor, presión con sacos de arena durante 48 horas.
Resultado al extraer los machos.
Preparación del laminado exterior en carena y cubierta, una vez lijada y nivelada la boca de caja de aleta: En carena pintamos el contorno de la caja con liquido acoplador de plásticos para conseguir mejor adherencia con resina y la minados, pintamos toda la zona con resina, tapamos el poro y nivelamos con resina espesada con microbalones, laminamos Cuatro paños alternos en carbono y fibra de vidrio de menor a mayor (carbono 180grs sarga, fibra de vidrio 165gr, carbono 175gr satin y fibra de vidrio 80gr. Cubrimos con tejido sangrador-pelable PEEL-PLY, manta de absorción y sujetamos con cinta de carrocero para dar la vuelta a la tabla y trabajar en cubierta.
Reposición laminado en cubierta: Preparación del laminado, pintado con resina y tapado del poro con resina espesada con microbalones, laminado en fibra de vidrio 165grs a la que hacemos unos cortes a la altura de los alojamientos de tornillo, laminado en sarga 200gr, hacemos los cortes, laminado en fibra de vidrio 80gr, hacemos los cortes, ponemos encima Tejido sangrador-pelable PEEL-PLY, manta de absorción y embolsamos cubierta y carena, depresión de 0,6 con bomba de vacío durante 8 horas aplicando calor alternativamente en carena y cubierta mediante bombilla de rayos infrarrojos durante 4 horas, dejo endurecer la resina de 48 horas.
Fresado del laminado en la entrada en la caja de aleta y esmerilado del laminado con dremel para evitar que la aleta al salir levante el laminado en los vértices.
Lijado del laminado sobrante en cubierta, se hacen los taladros en el fondo alojamientos tornillos, se taladra y avellanado taladros tornillos footstrps, tapado de poro y nivelar con pasta de carrocero, lijado al agua imprimación y pintura.
Colacacion de pad reciclado, señalado de taladros con remaches cortados y metidos en los huecos para que atraviesen el pad y poder señalar su sustitución, pegado de pad con cola de contacto especial poliestireno (esta no hace reaccionar la pintura al no tener disolventes), compresión con cinta de embalar y sacos de arena para garantizar el pegado, reposición del antideslizante con laca y polvo de corindón.
Eliminación del sobrante de laminado en carena con cuter, lijado con orbital, tapado de poro y nivelación con pasta de carrocero, lijado al agua, imprimación, pintura y laca mate.
Resultado en cubierta popa
Resultado en carena popa con la aleta insertada quedando a nivel.
Los tornillos son mas largos ya que la caja es mas alta
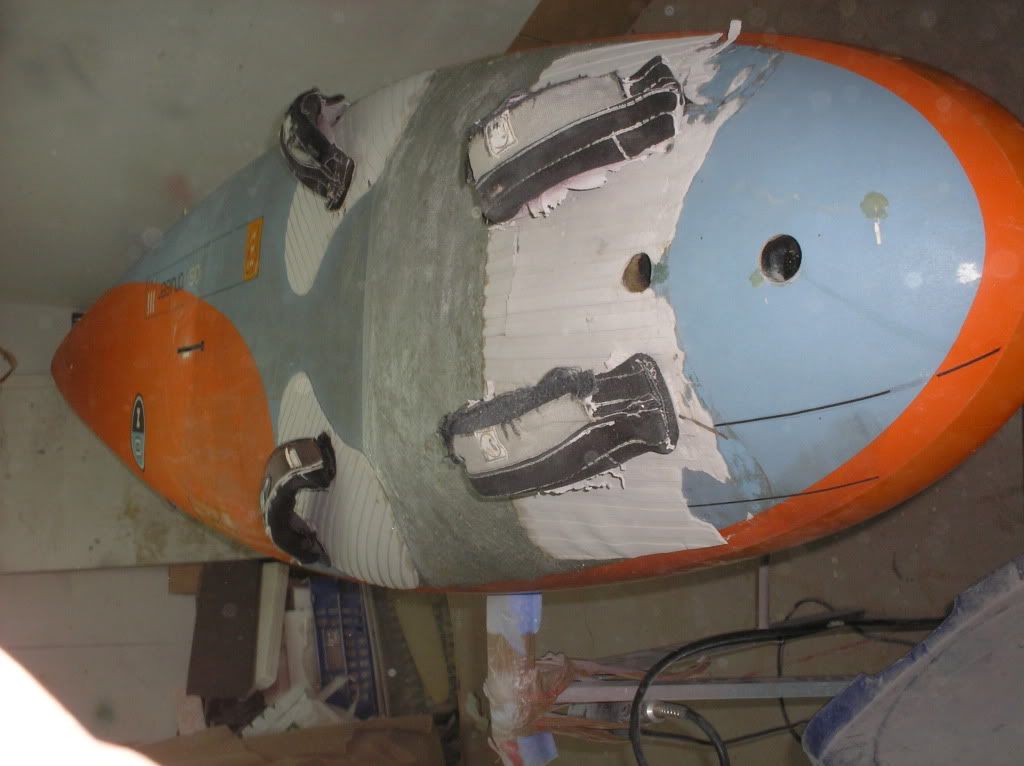
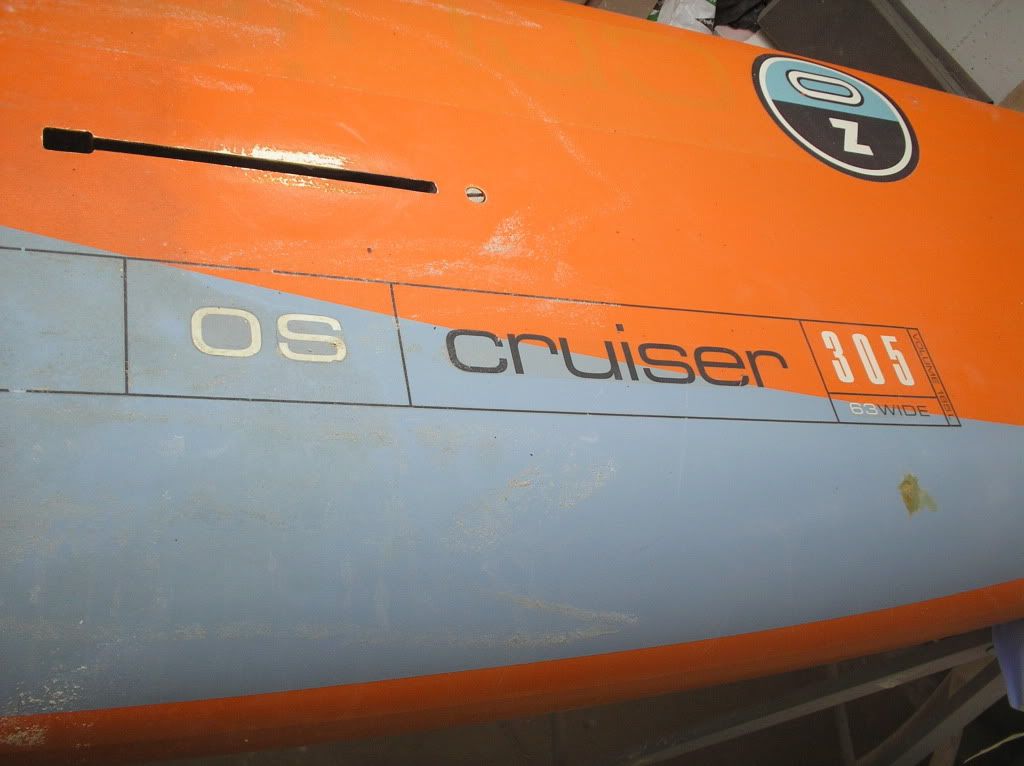
Es una tabla en la que reparación y su valor por antigüedad-estado se igualan. Se repara ya que el dueño le gusta esta tabla y como navega.
Por colisión de la aleta con unas rocas, se desprende parcialmente la caja de aleta.
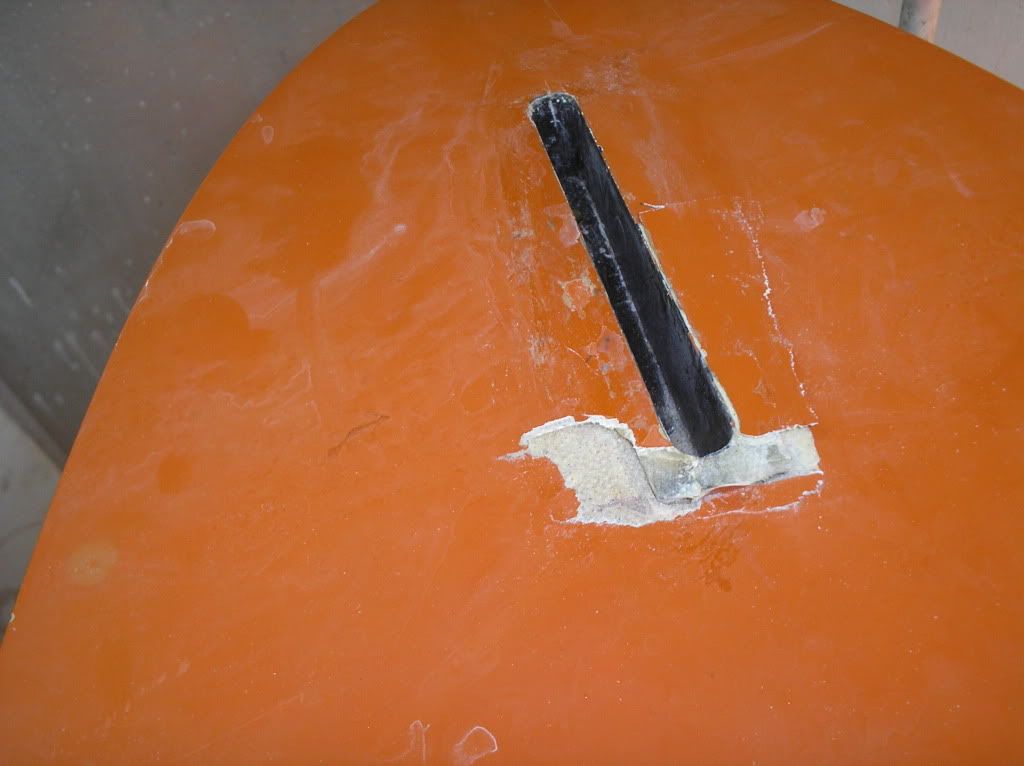
Haciendo un poco de palanca sale la caja, que resulta estar fabricada en fibra de vidrio.
Después de limpiar el laminado adherido veo que esta fracturada y que no es reutilizable. Hay que reponer con una Chinock Tuttlebox de plástico negro.
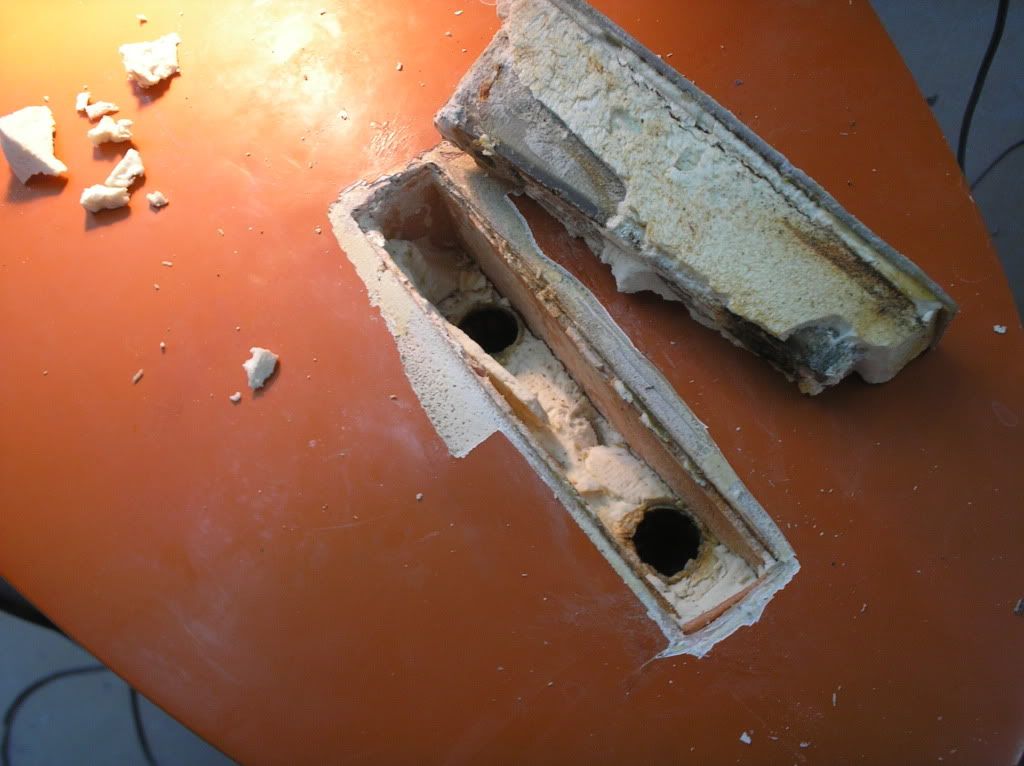
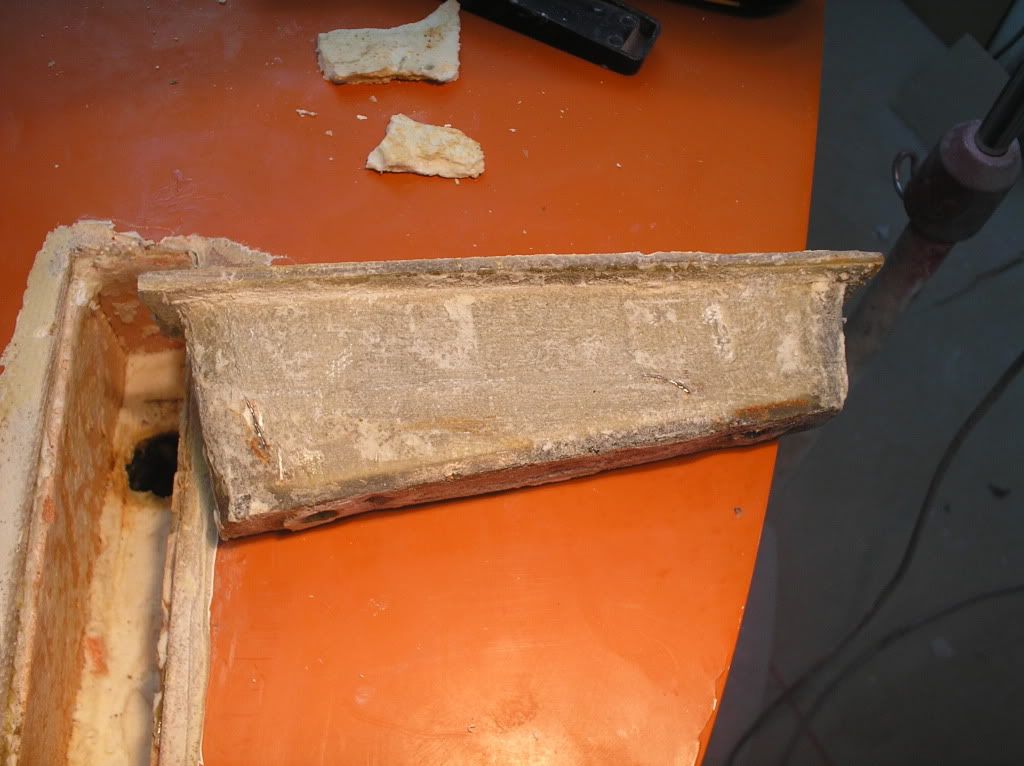
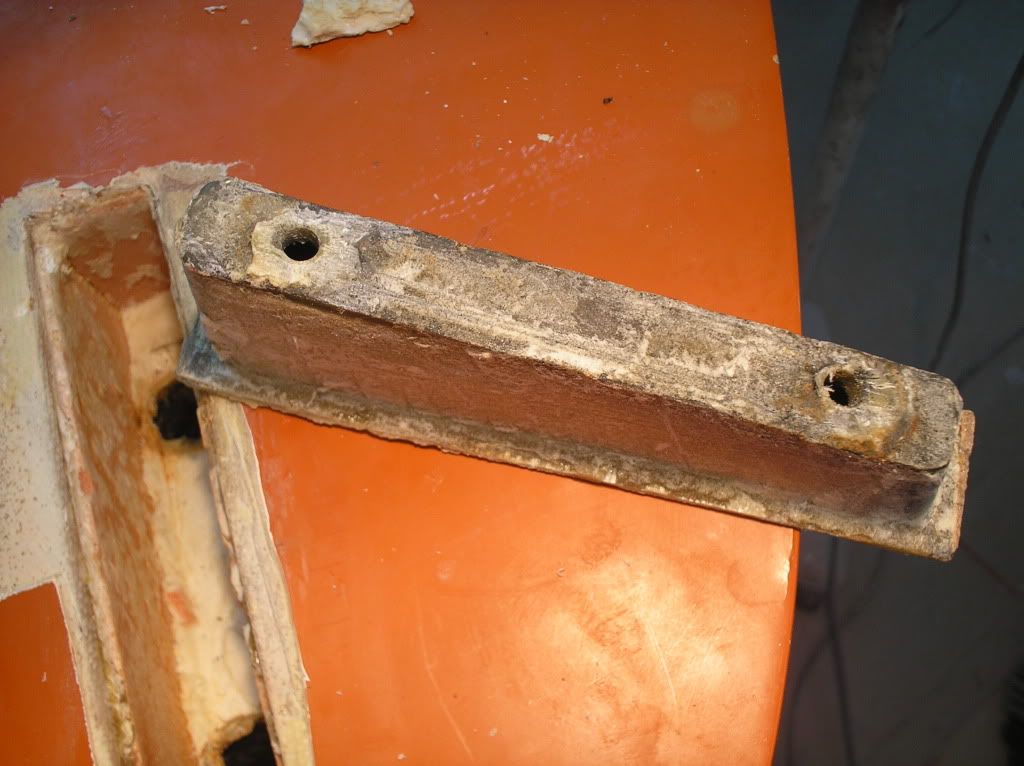
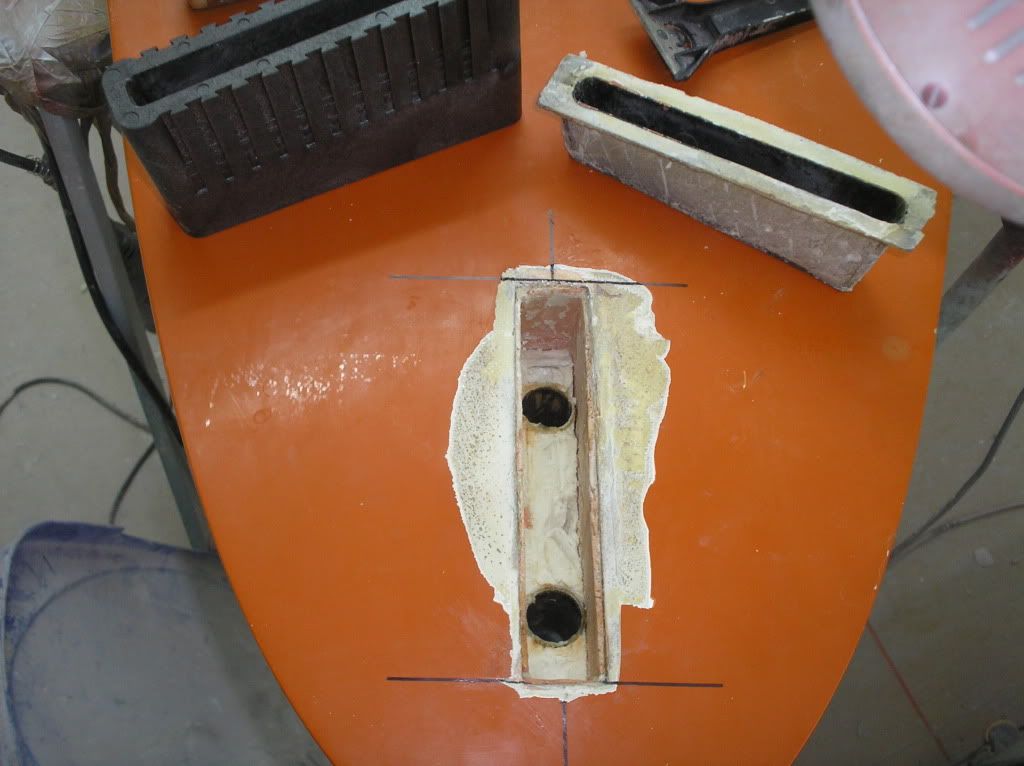
Esta nueva caja me obliga a fresar en profundidad y en anchura desde carena y cubierta.
Veo que la caja de aleta estaba embutida en un bloque de XPS, que a su vez tiene un cerclaje en PVC de solo 3mm revestido en fibra de vidrio y con algunas grapas metálicas que estaban oxidadas por entrada de agua que llego hasta el núcleo del EPS. Creo que había una vía de agua previa al choque de la aleta, ya que el oxido encontrado en el PVC llevaba mucho mas tiempo actuando.
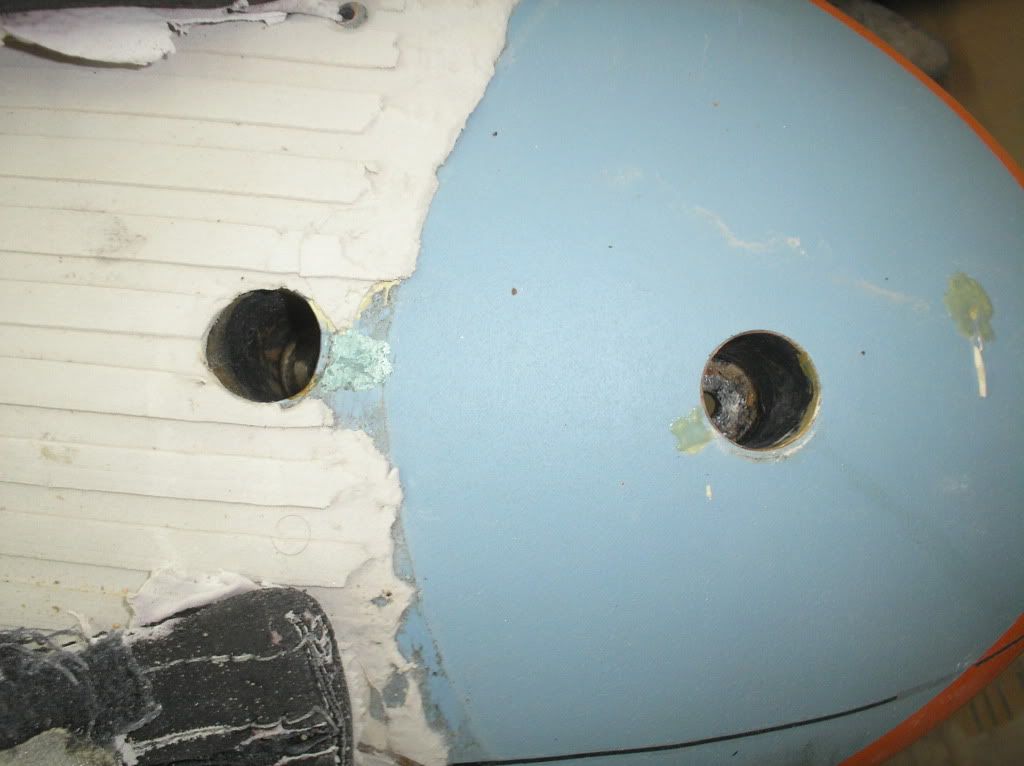
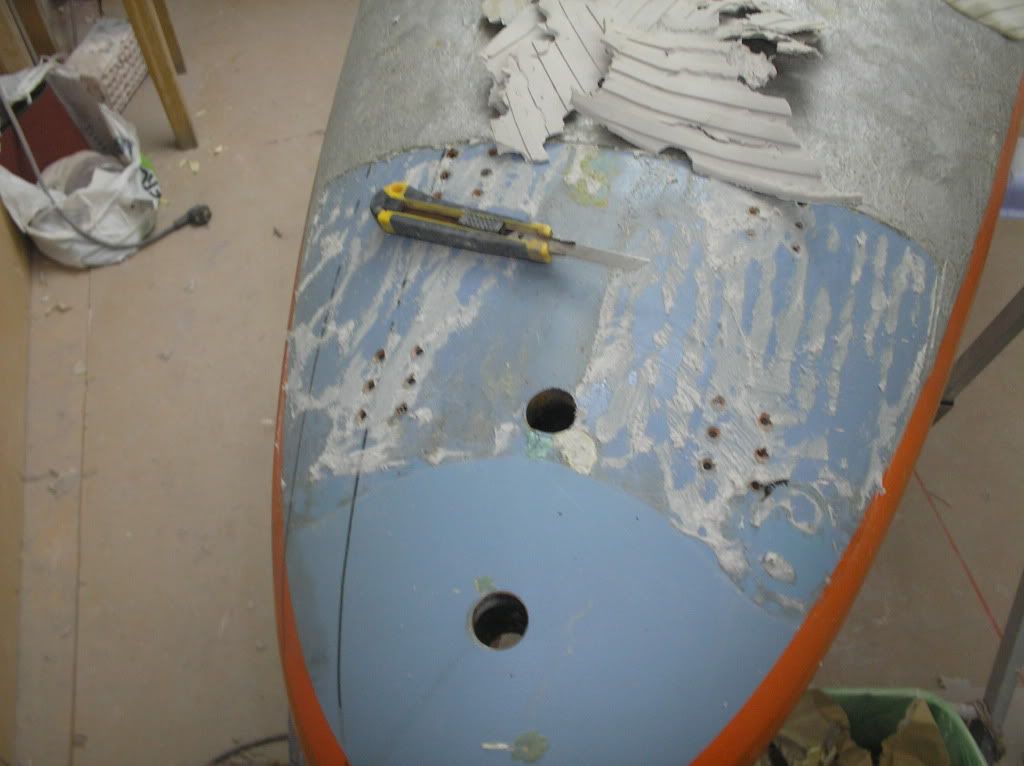
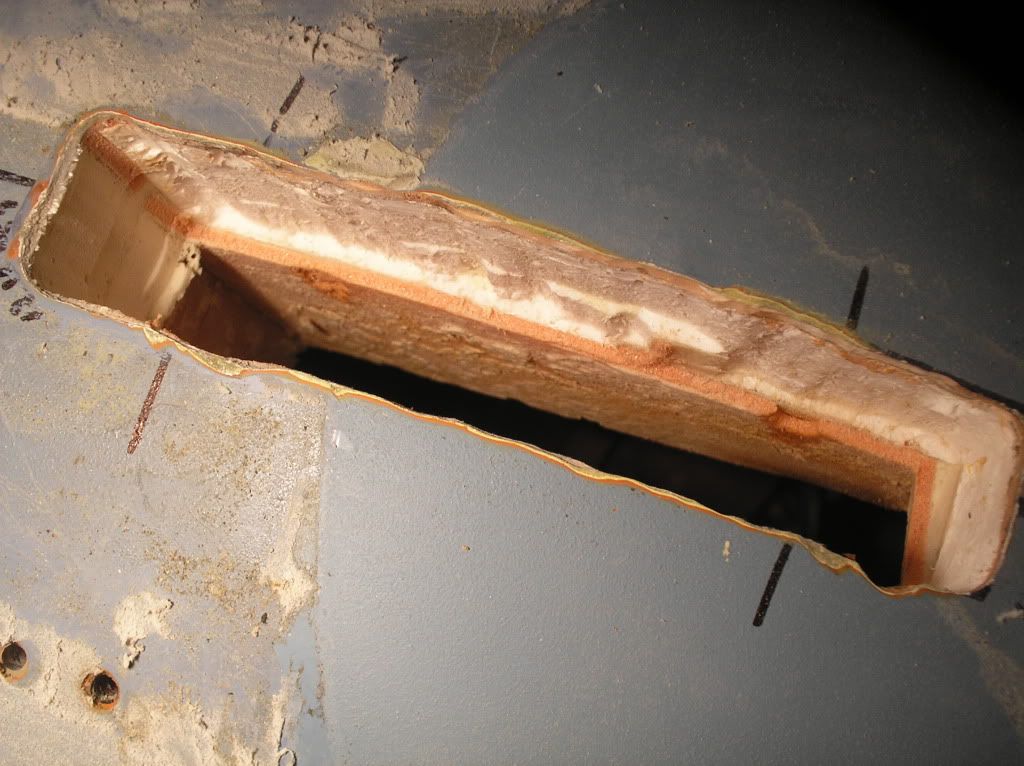
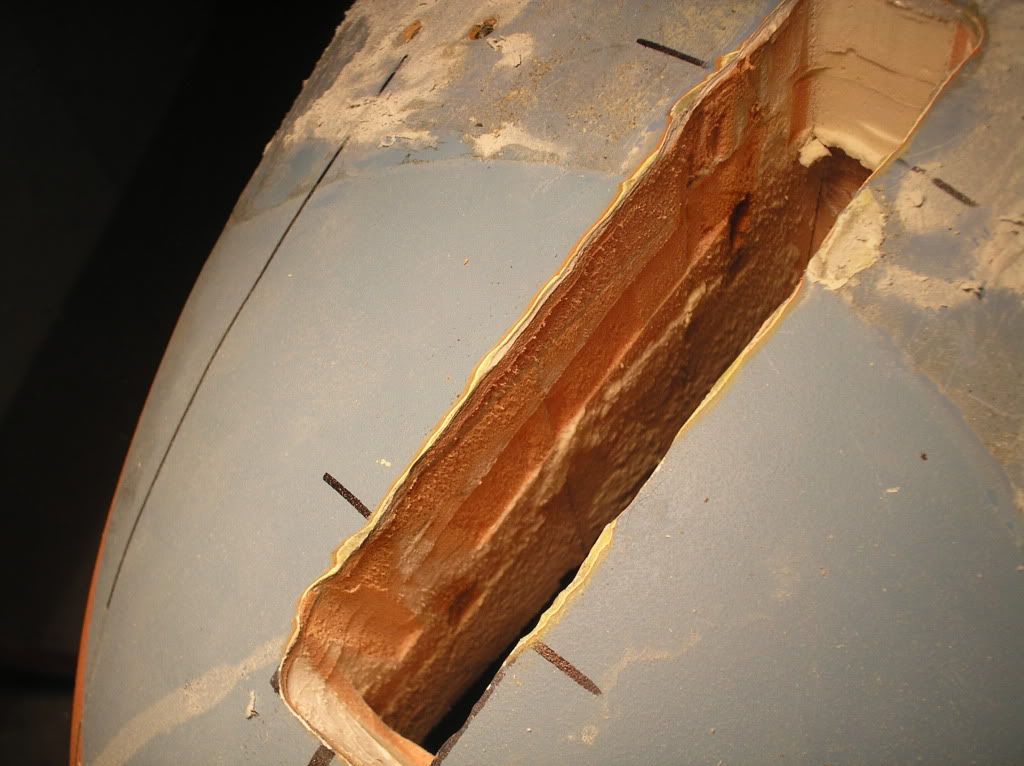
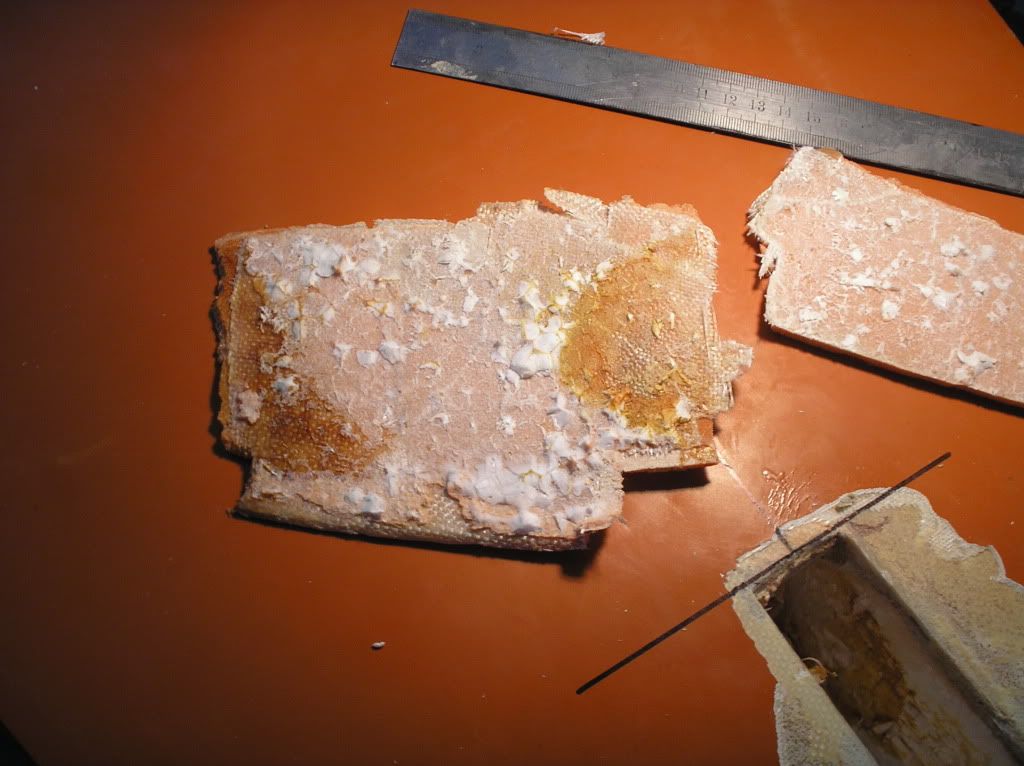
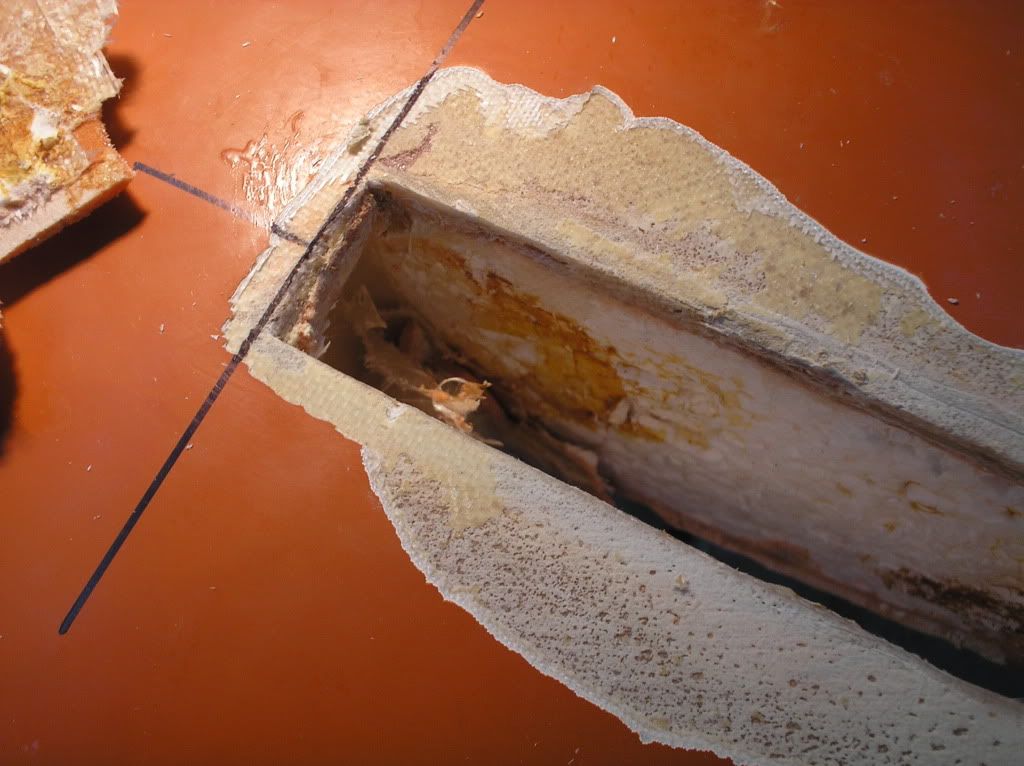
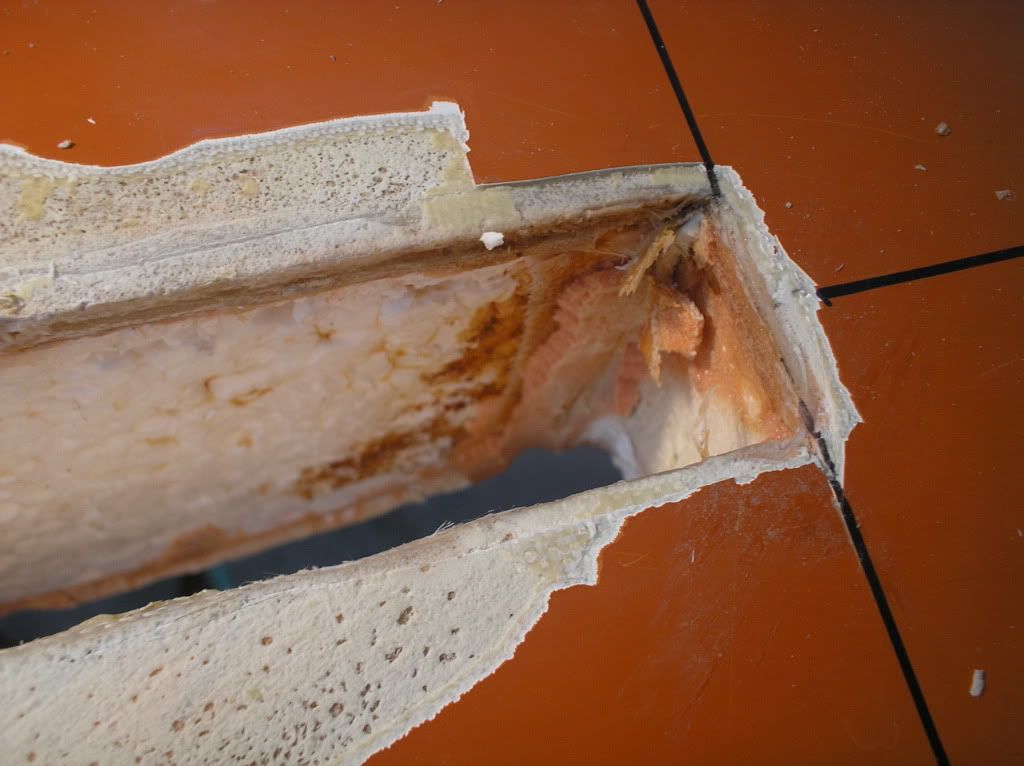
Presento la nueva caja de aleta.
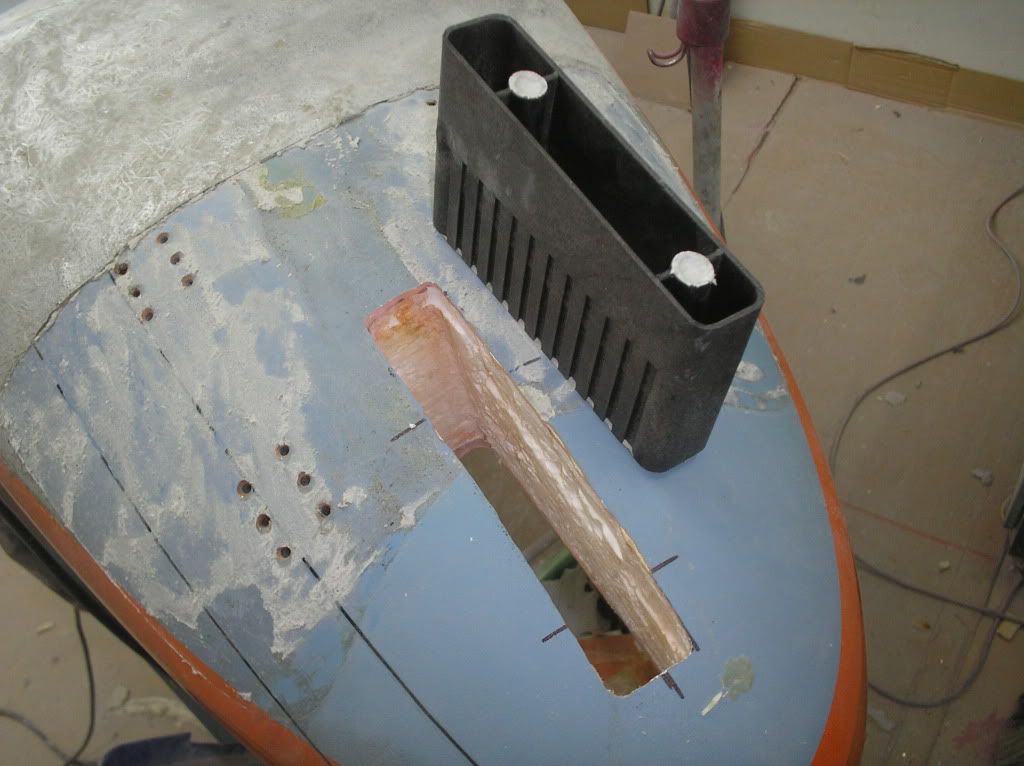
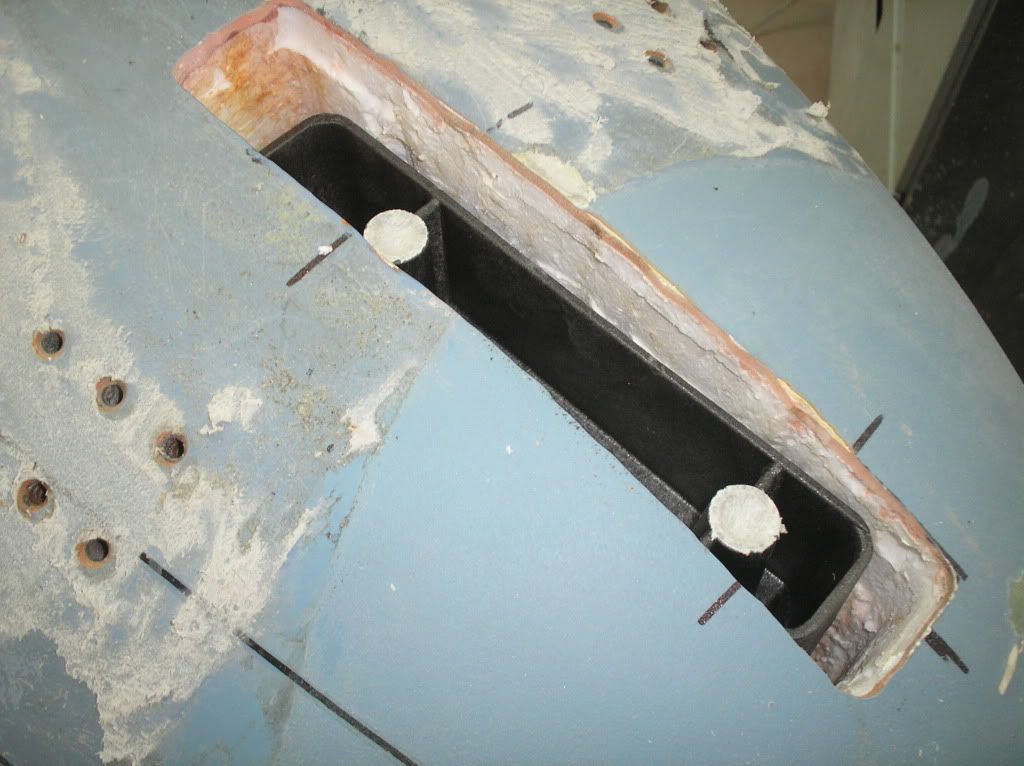
Relleno la parte superior de la caja (que aproveche en toda su altura interior ya que el grosor de la tabla en popa es superior) con espuma de poliuretano de dos componentes de alta densidad, “enfundo” la caja de aleta con PVC de 5mm en los costados y de 12mm en el fondo y los dos lados: frontal y posterior, pegadas con resina espesada con microbalones y que presiono con sargentos hasta el endurecimiento de la resina.
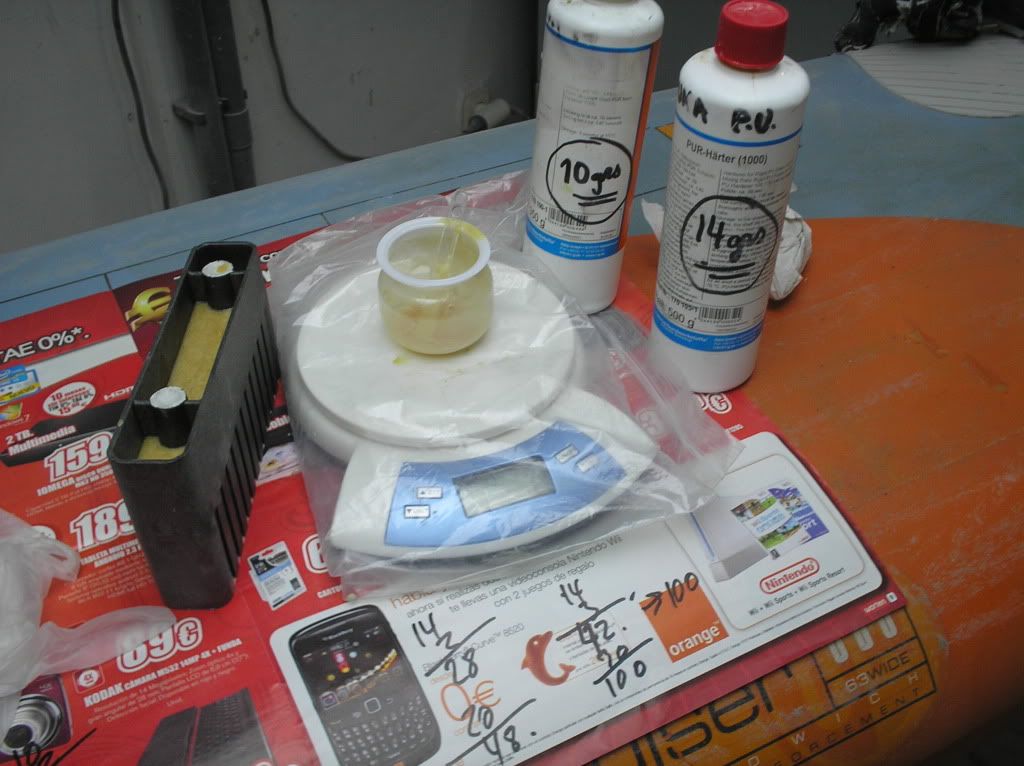
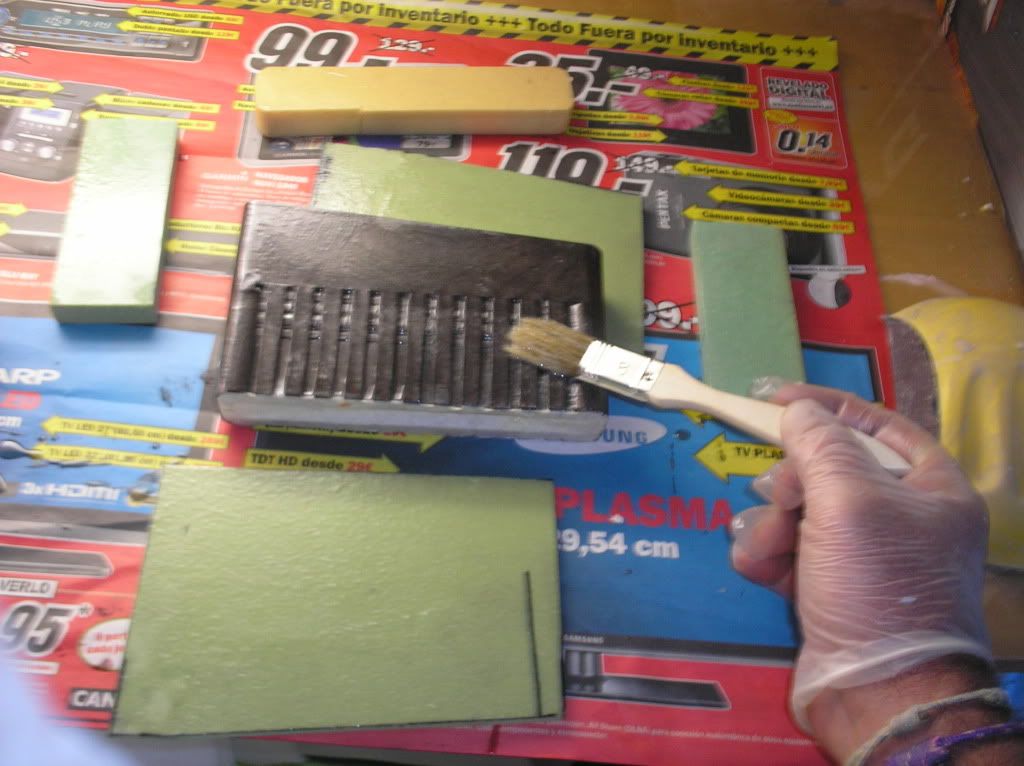
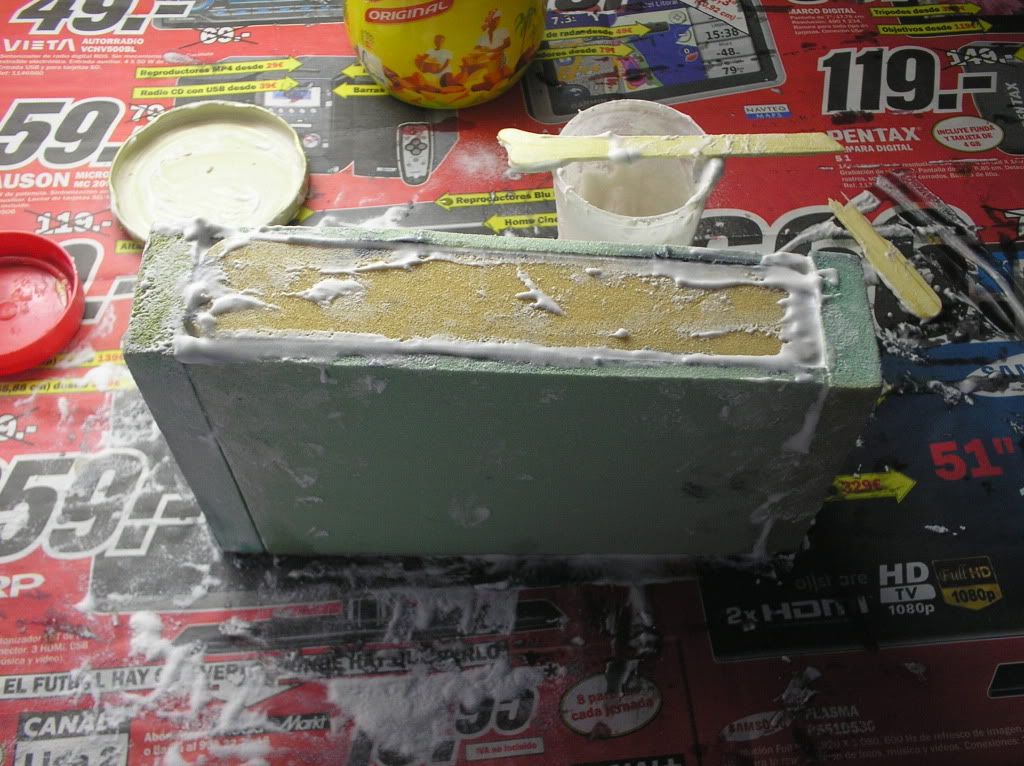
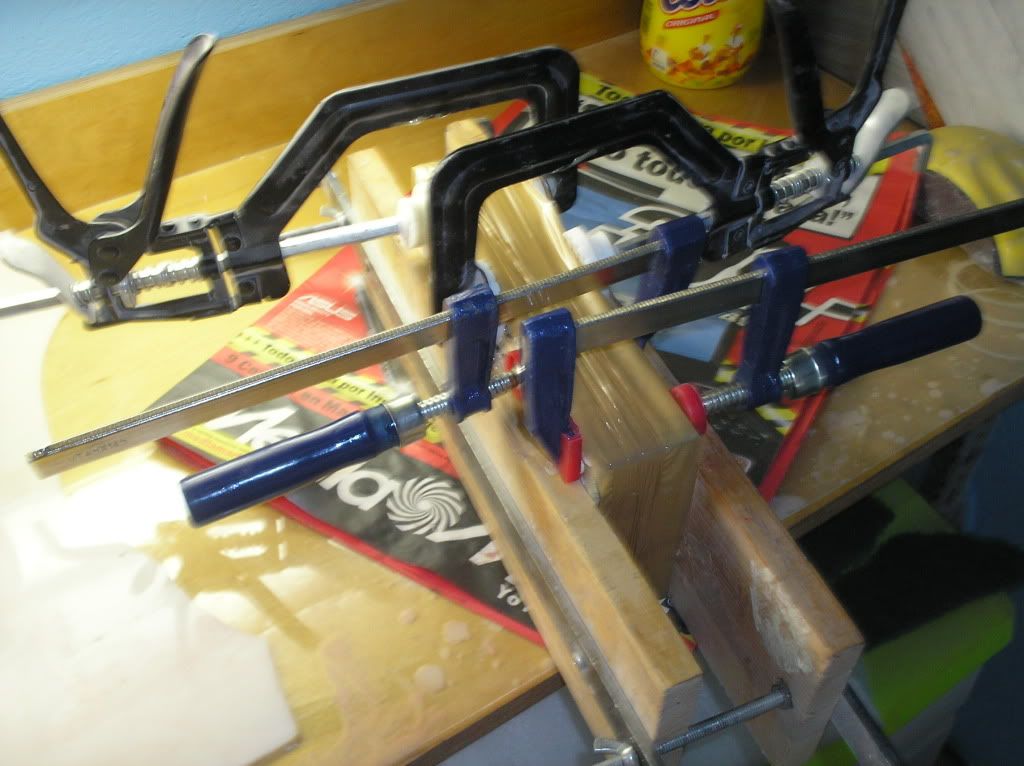
Vuelvo a fresar el hueco para adaptarlo al ancho y largo de la caja revestida de PVC, lijado interior de las paredes del EPS, preparación de materiales para embutir la nueva caja. “pintado” interior con resina, tapado del poro con resina espesada con microbalones, “pintado”de la caja de aleta con resina, revestido con carbono de 180g en sarga y otro laminado encima en fibra de vidrio de 165gr y embutido hasta dejar a nivel superficial en carena.
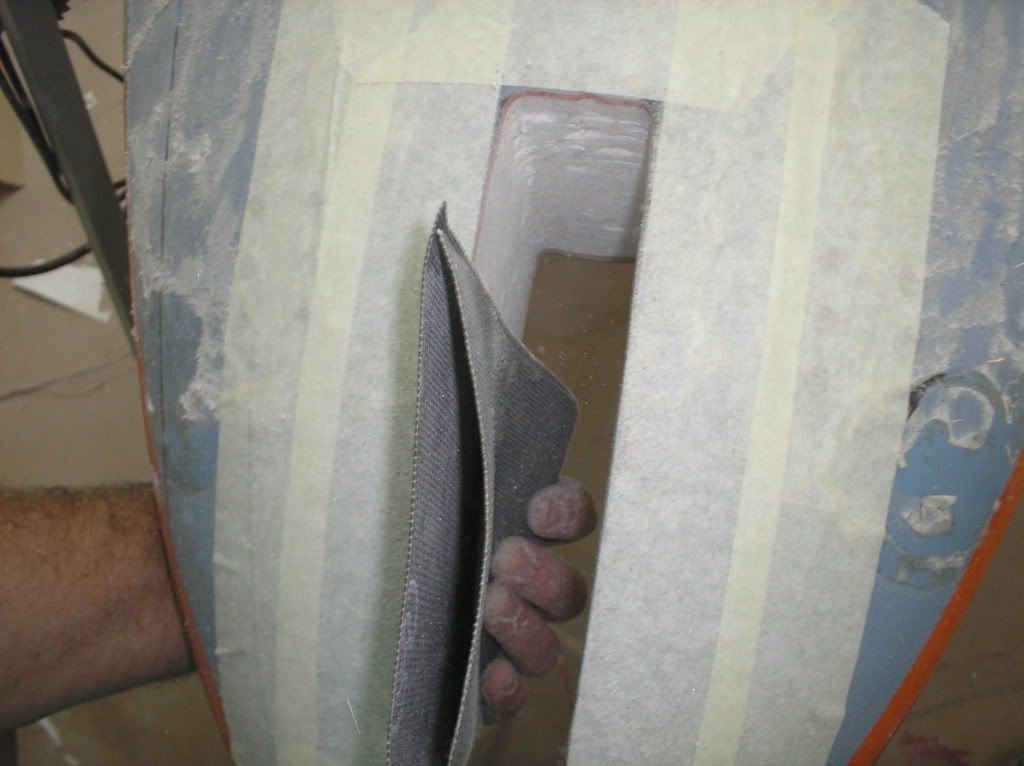
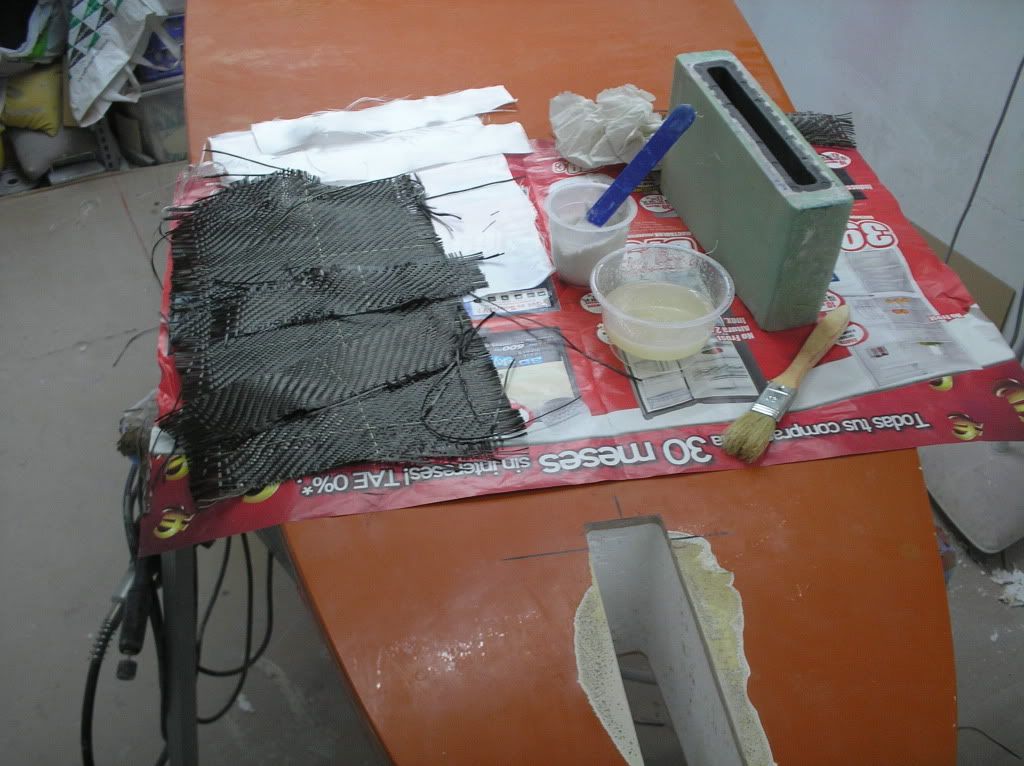
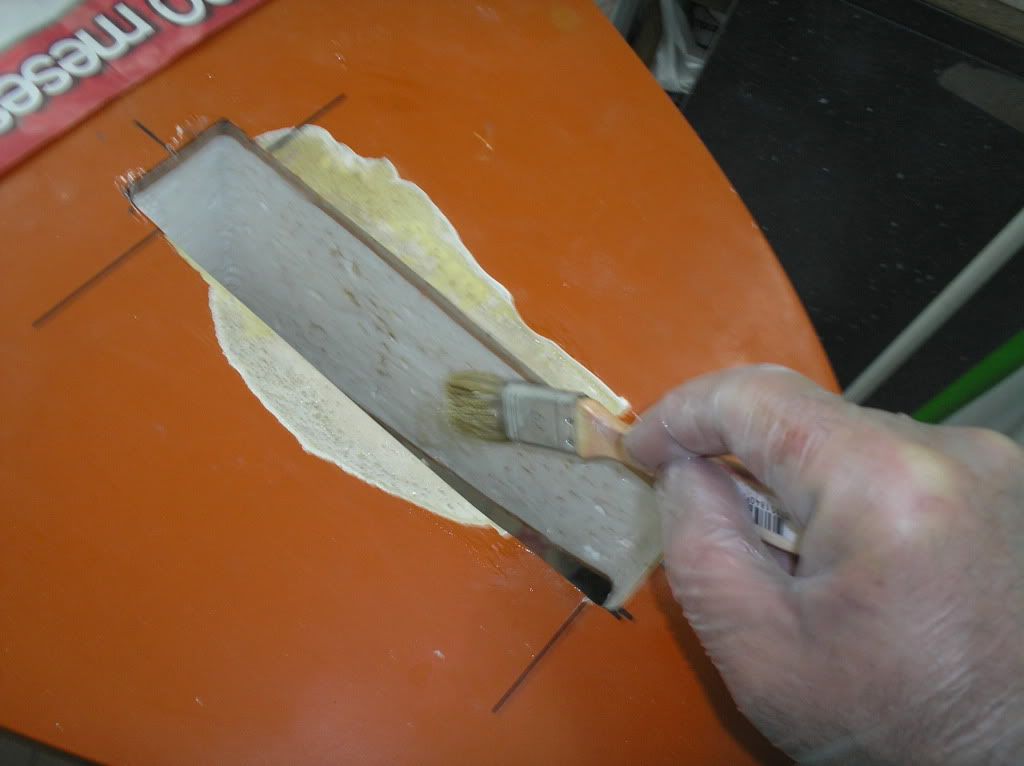
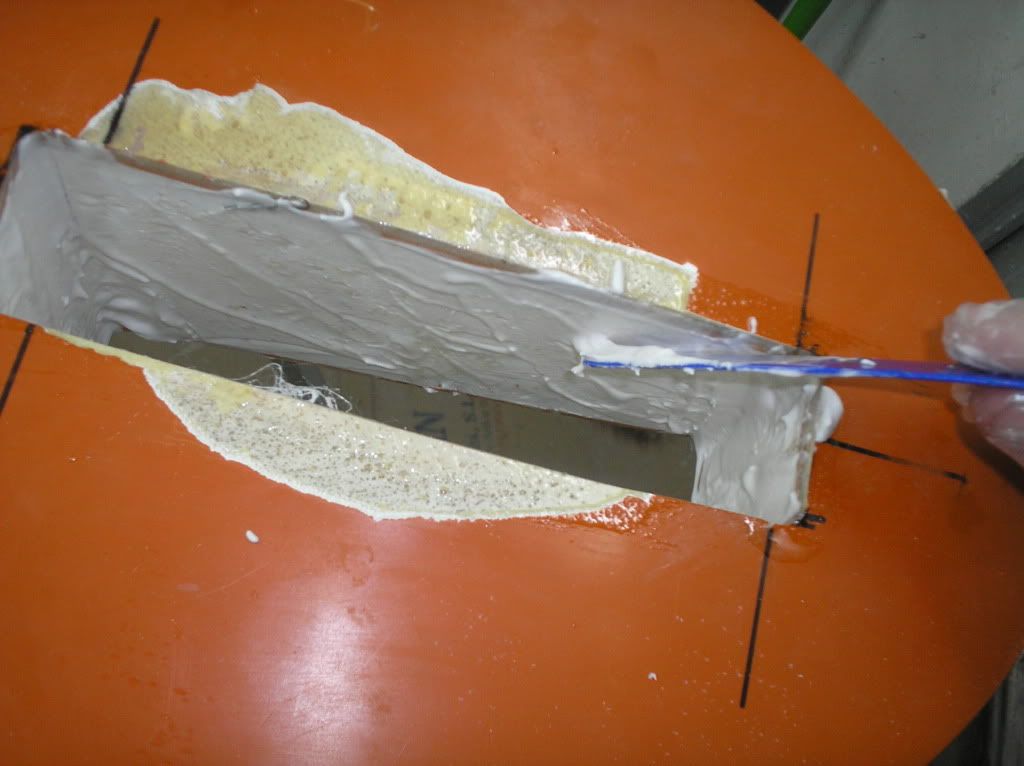
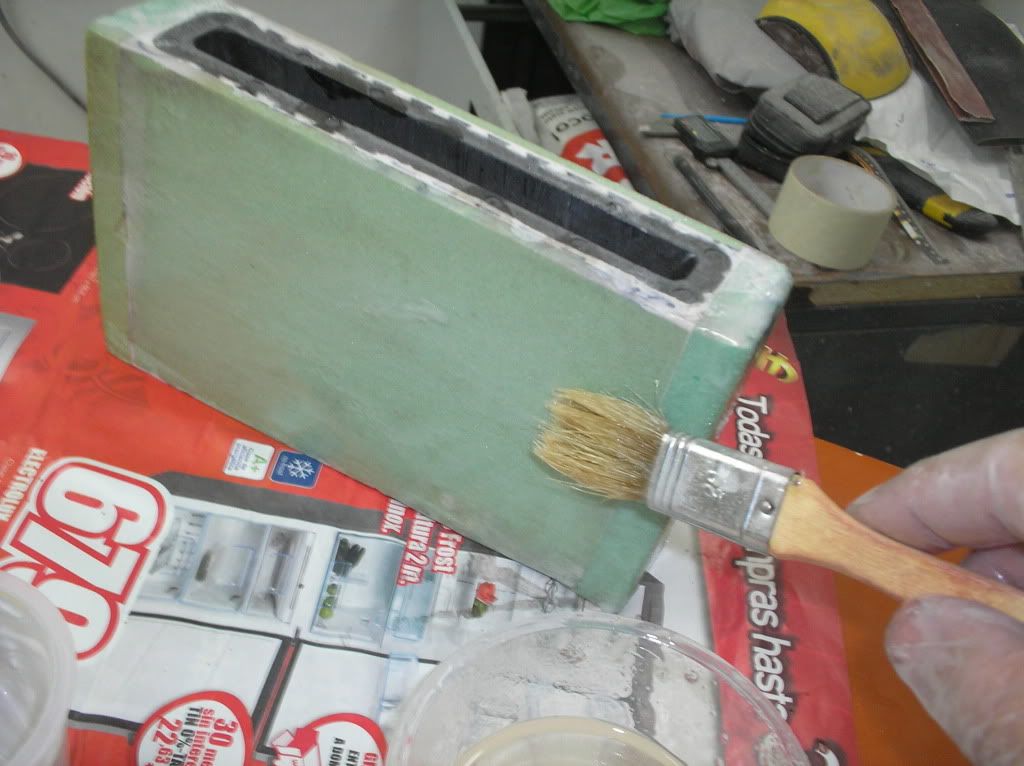
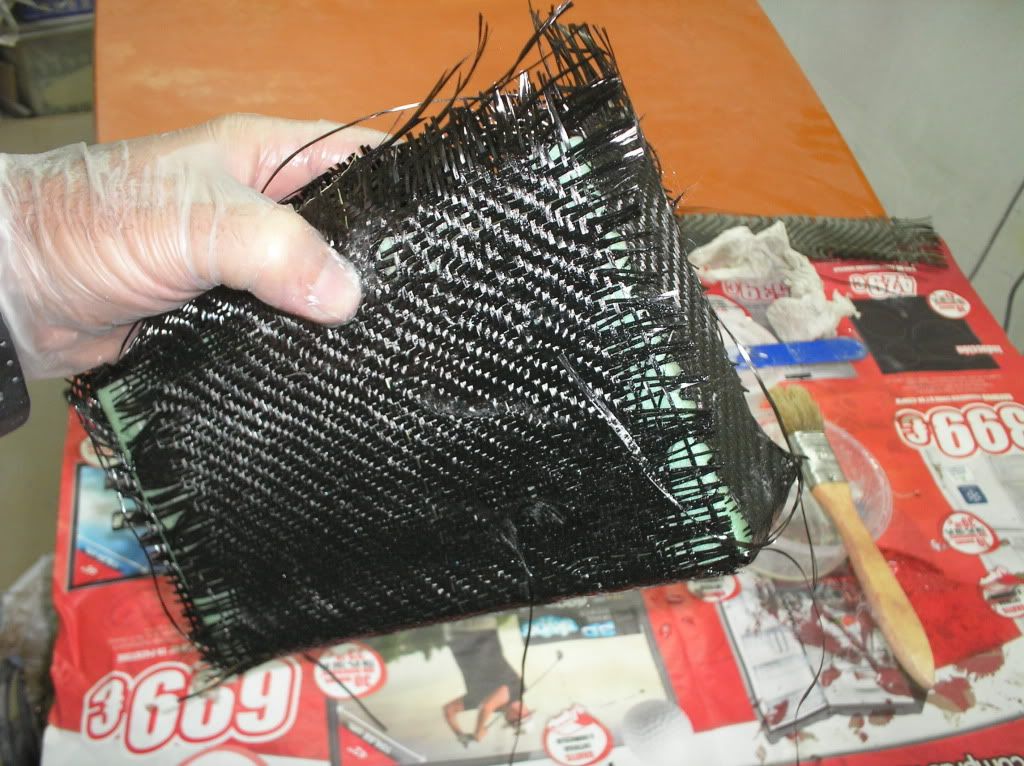
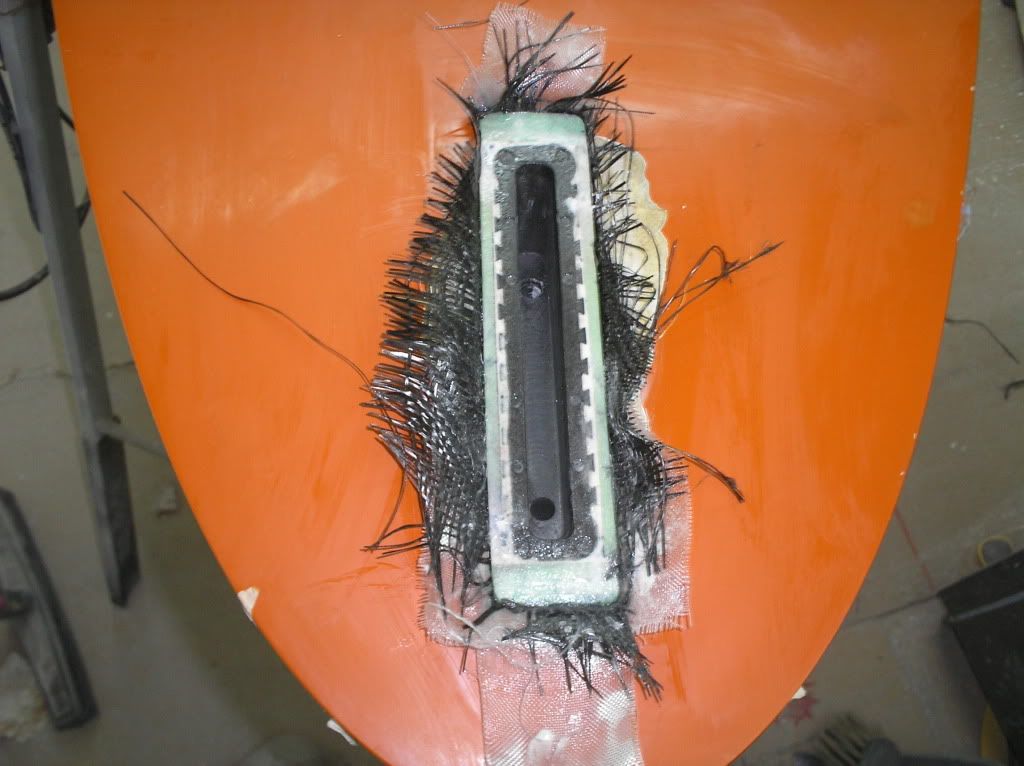
Colocación de la aleta para corregir la perpendicularidad de esta con respecto a la carena mediante un nivel láser.
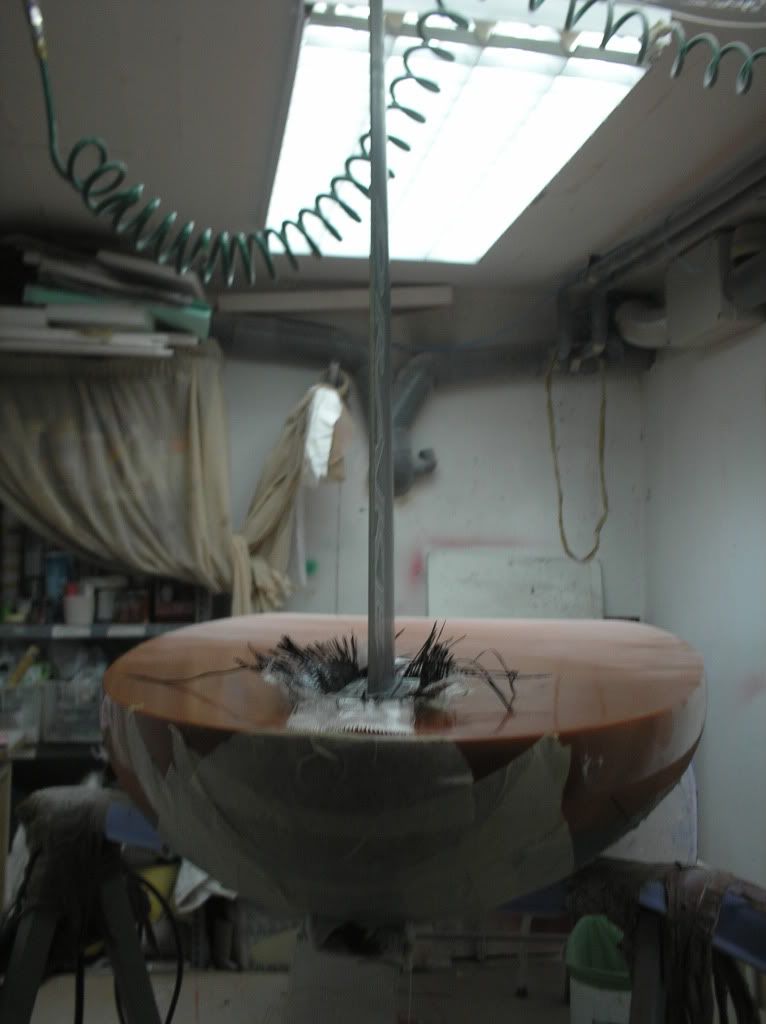
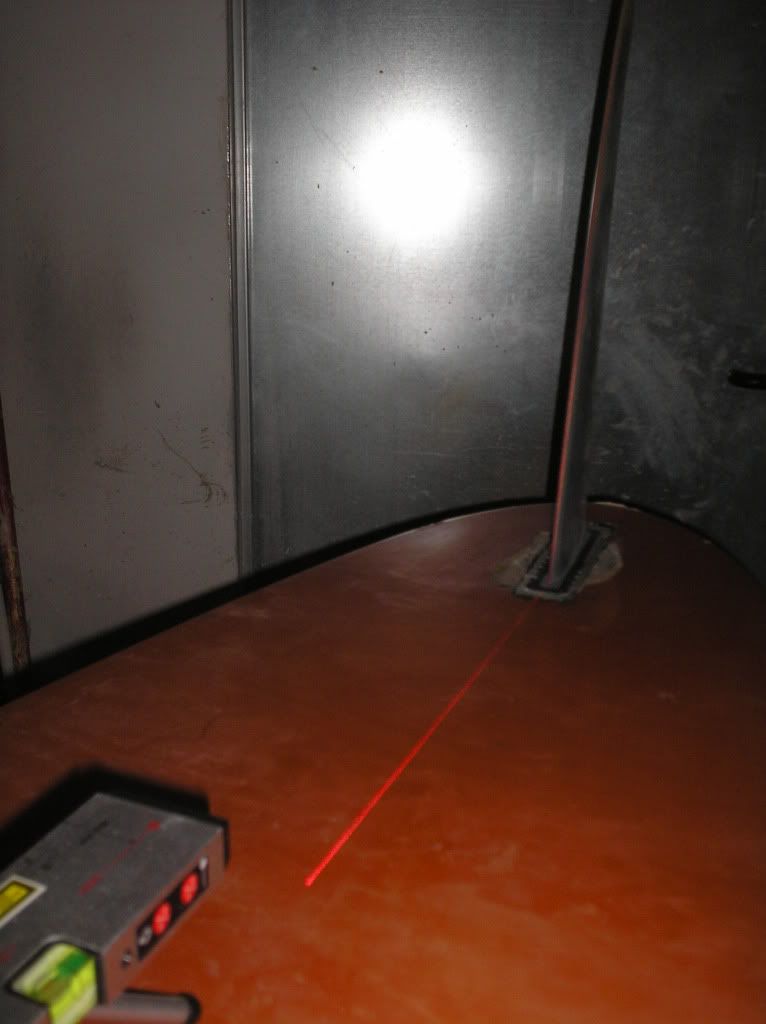
Tras el lijado del exceso el PVC sobrante en cubierta, repongo con doble sándwich en cubierta para conseguir el grosor original con dos capas de PVC de 3mm: Pintado con resina, relleno y nivelado con resina espesada con microbalones, laminado en fibra de vidrio de 165gr, Pieza de PVC de 3mm impregnada con resina, laminado en fibra de vidrio de 80gr, 2ª pieza de PVC de 3mm, cubro con tejido sangrador-pelable PEEL-PLY, manta de absorción, bolsa de vacío (que enfunda carena y cubierta) y compresión mediante bomba de vacío con depresión de 0,7, durante 9 horas con manta de calor durante 4 horas. Reposo hasta endurecimiento de 48 horas.
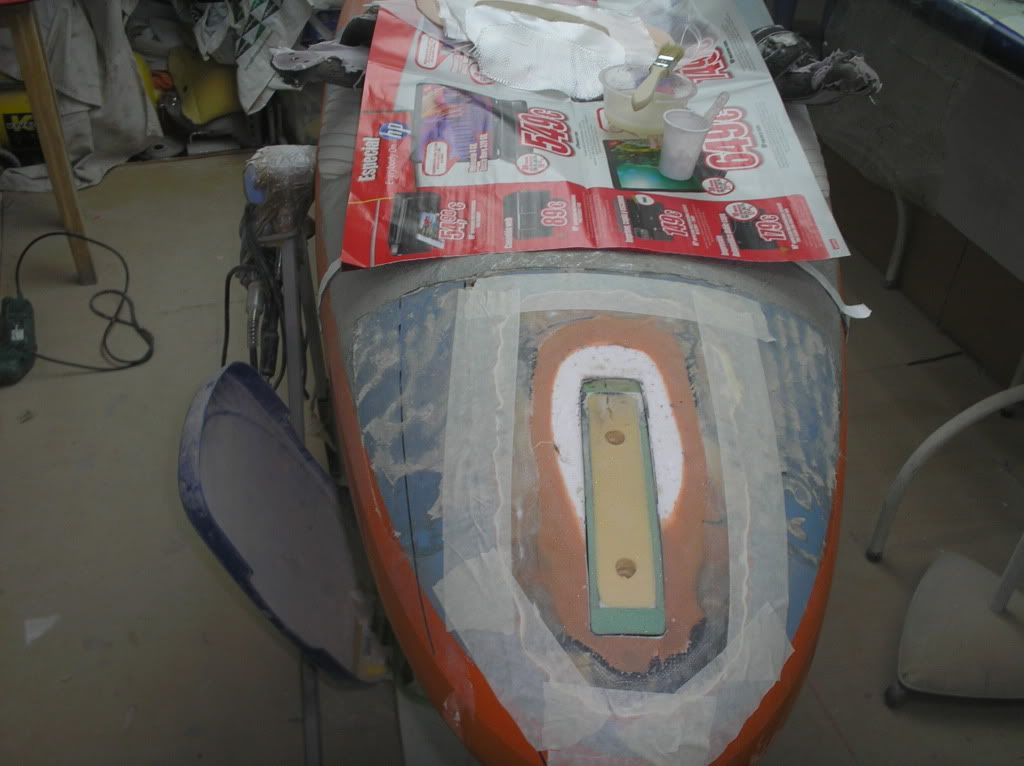
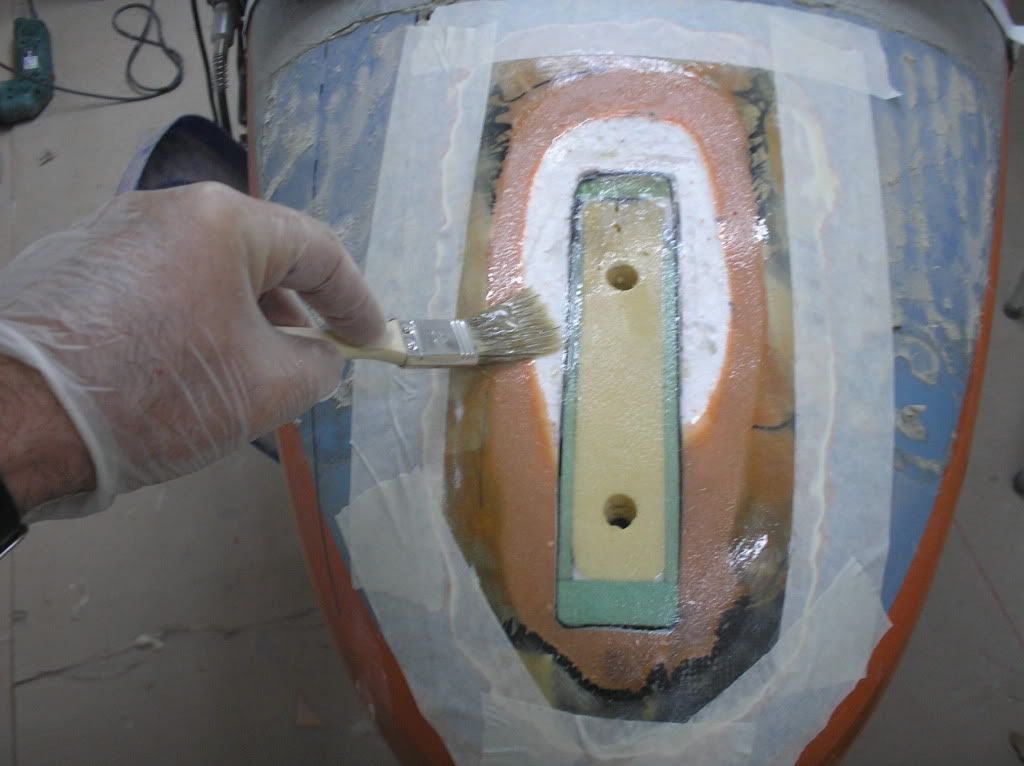
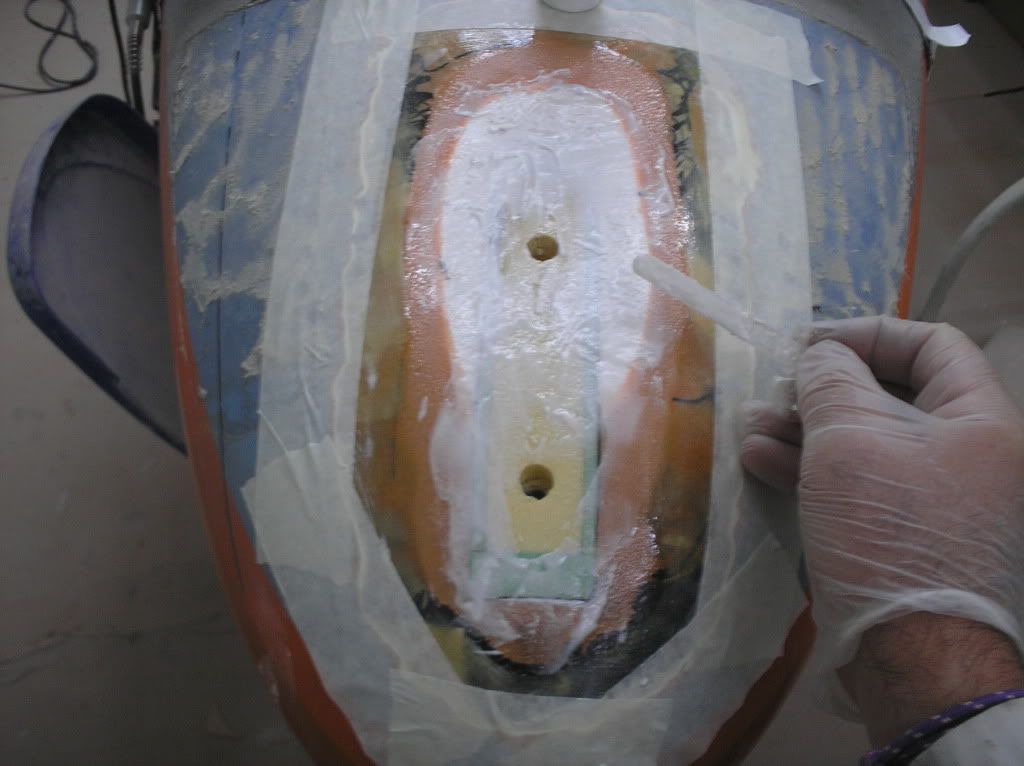
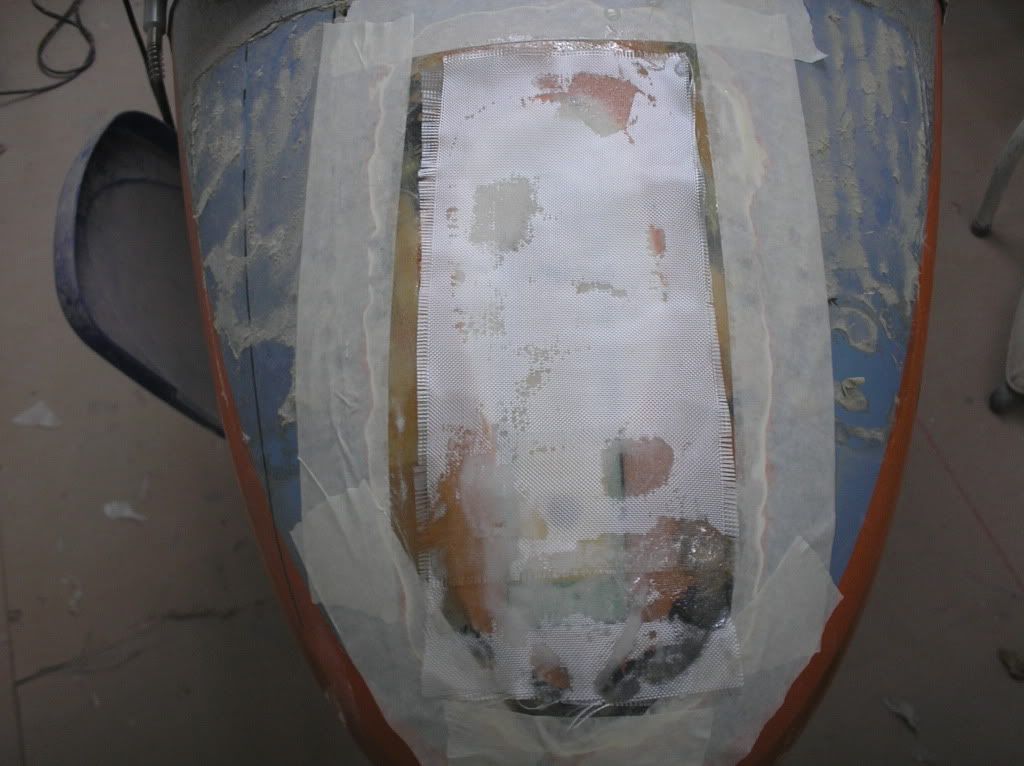
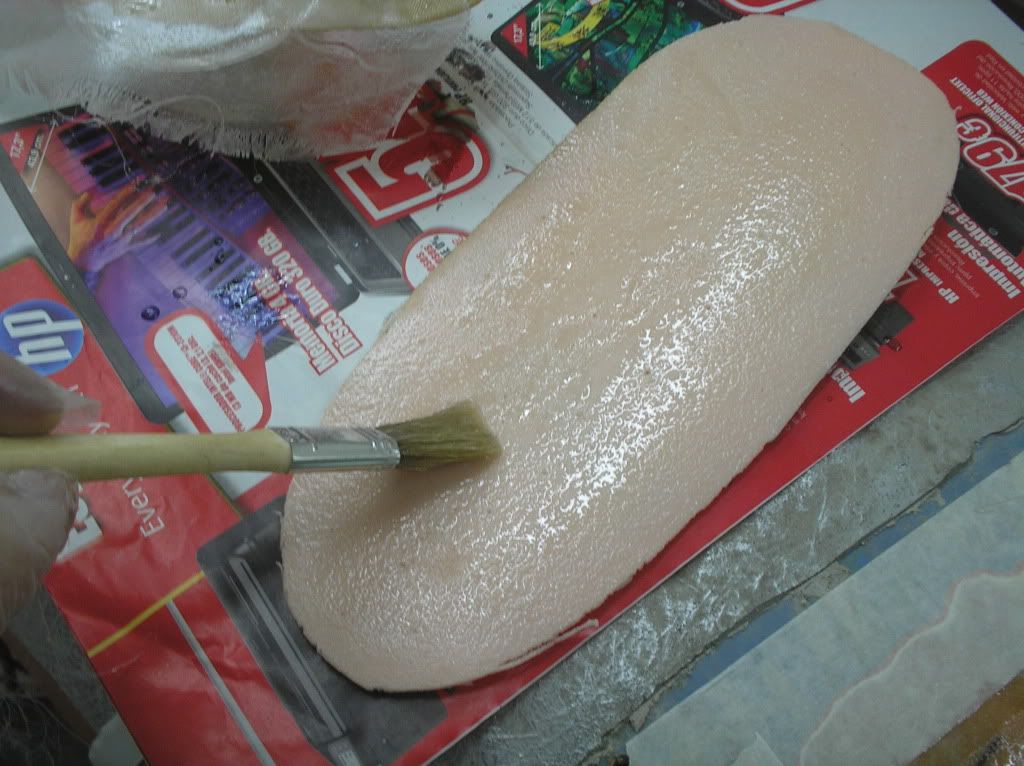
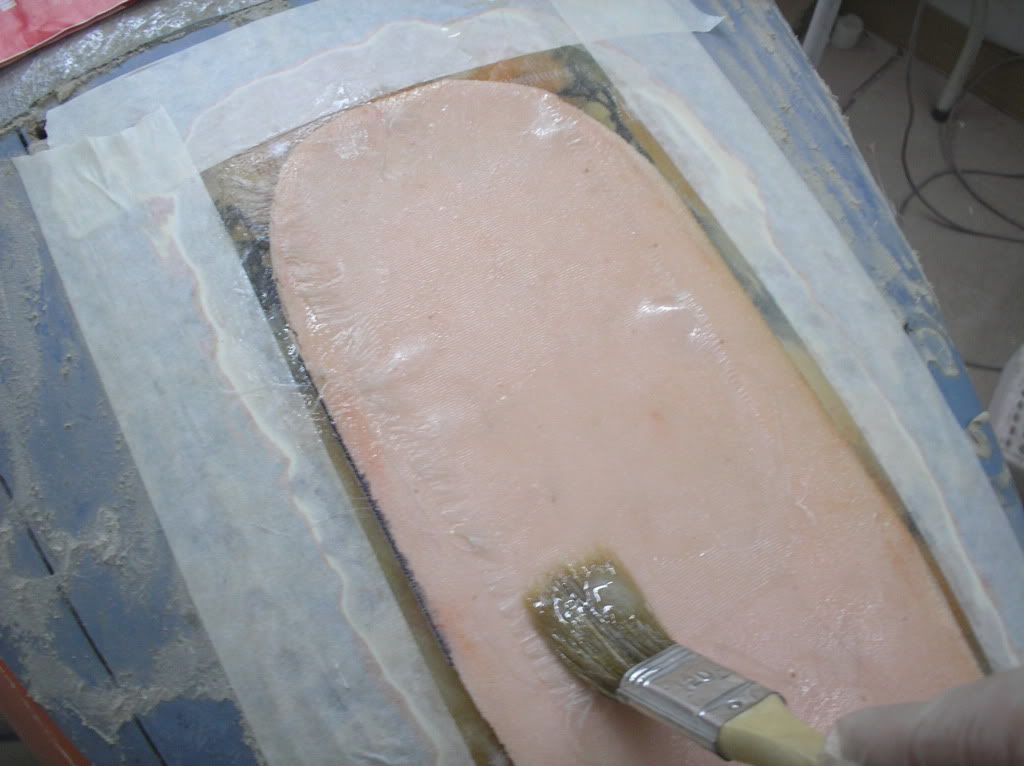

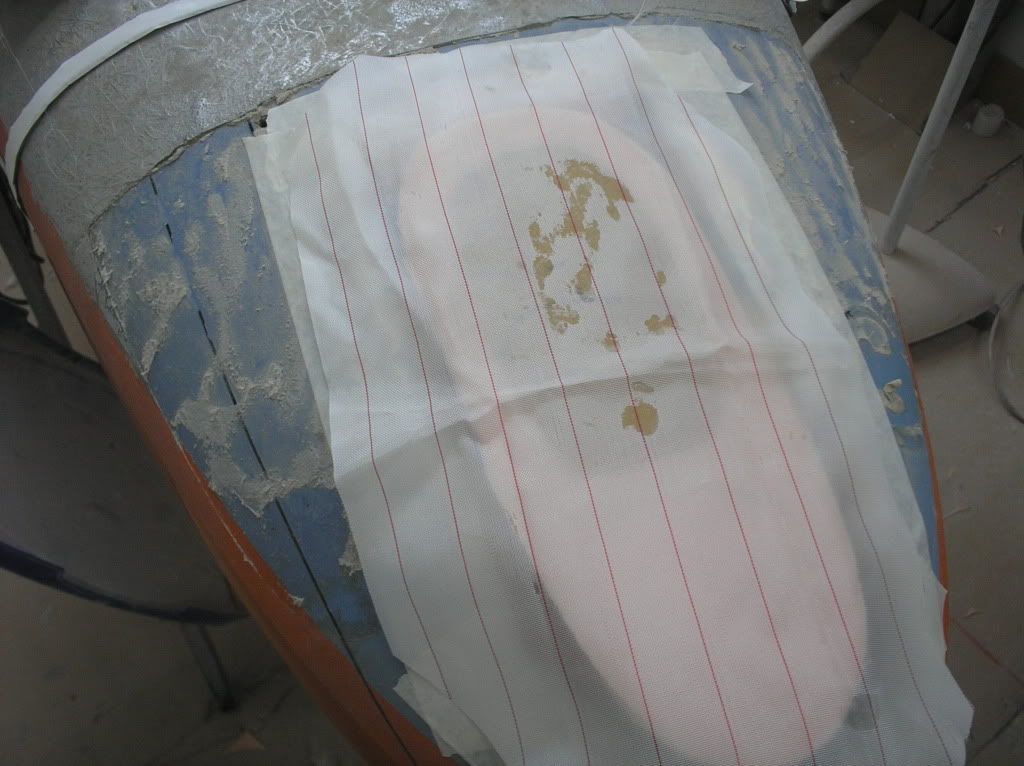
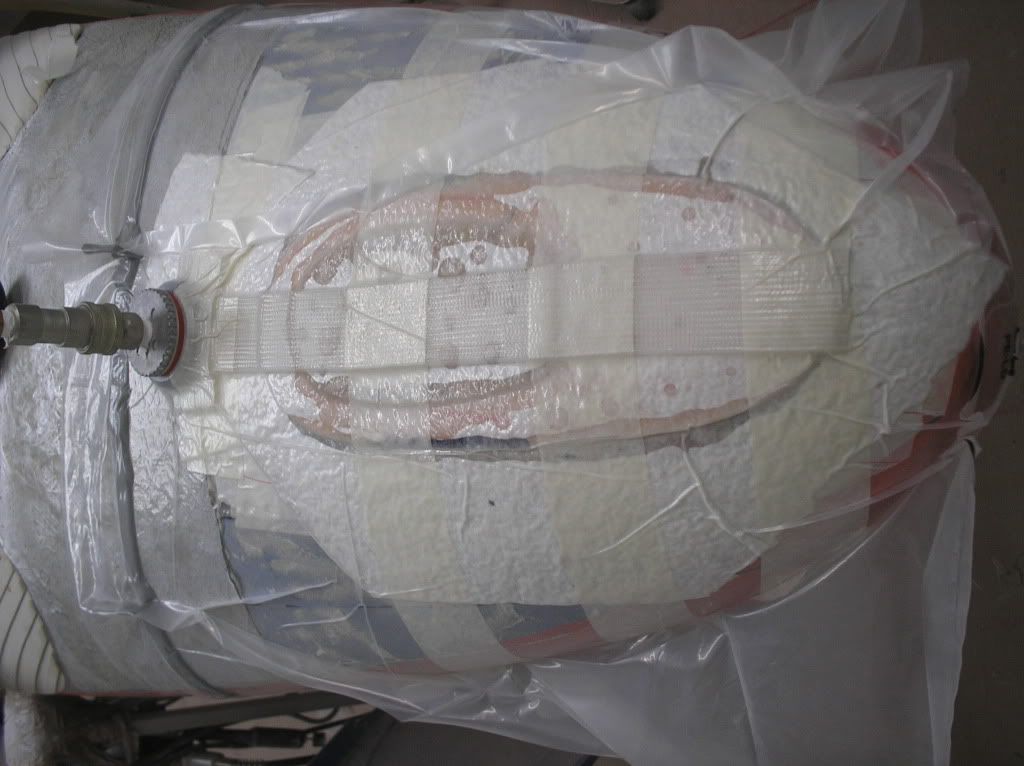
Lijado del nuevo PVC en cubierta dejándolo a nivel del original, señalado y fresado de los alojamientos de tornillos llegando hasta la superficie de plástico de la caja de aleta, preparación del laminado en carbono y fibra de vidrio del fondo y contorno interior de los alojamientos mediante machos recuperables (en carbono, de una vieja botavara) que se han enfundado con “dedos” cortados de guantes de vinilo, pintados con cera desmoldeante y a los que hemos enrollado los laminados, impreganandolos con resina, recorte en círculos de laminados en fibra de vidrio y carbono que asentaran en el fondo de los alojamientos de tornillos
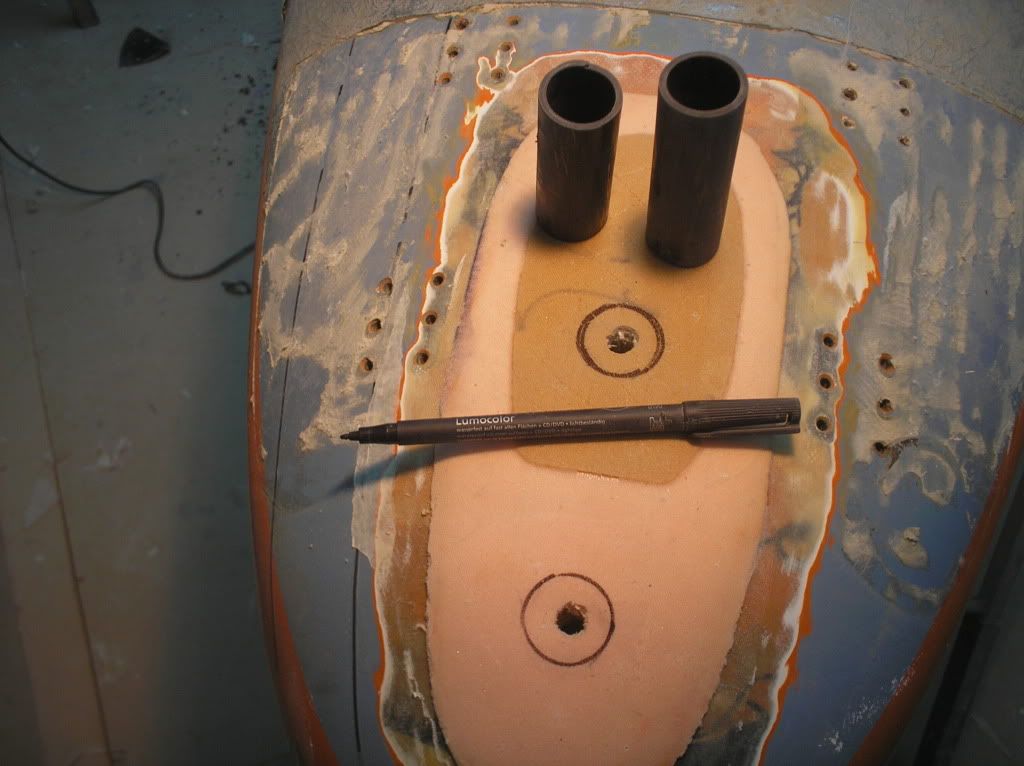
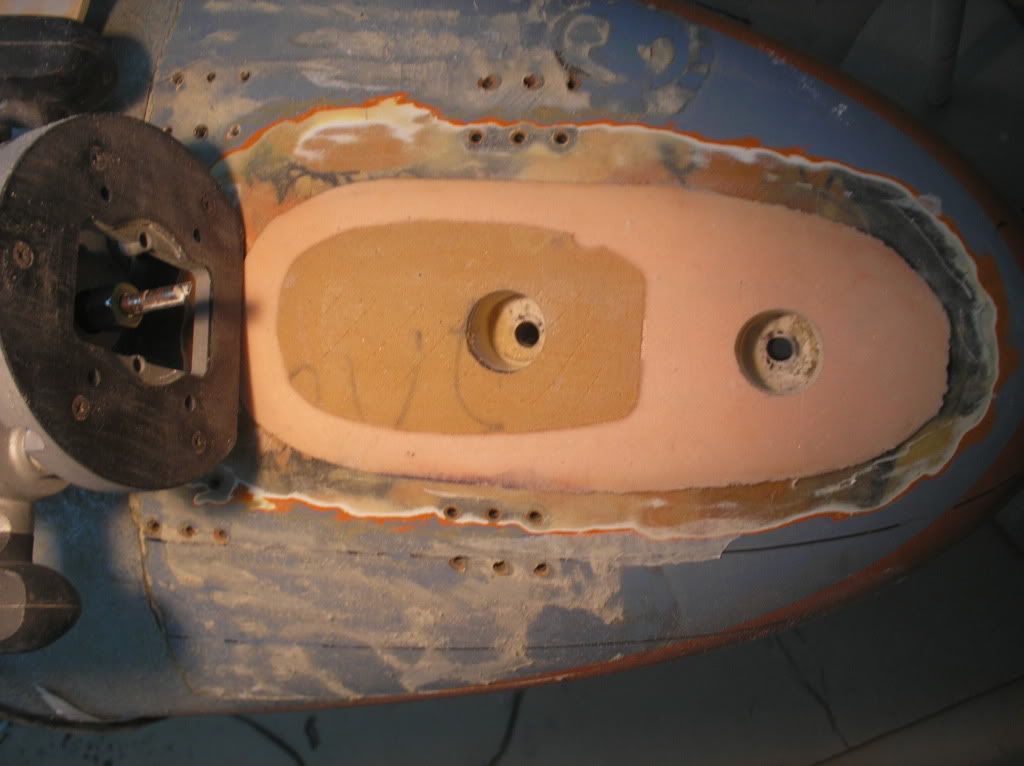
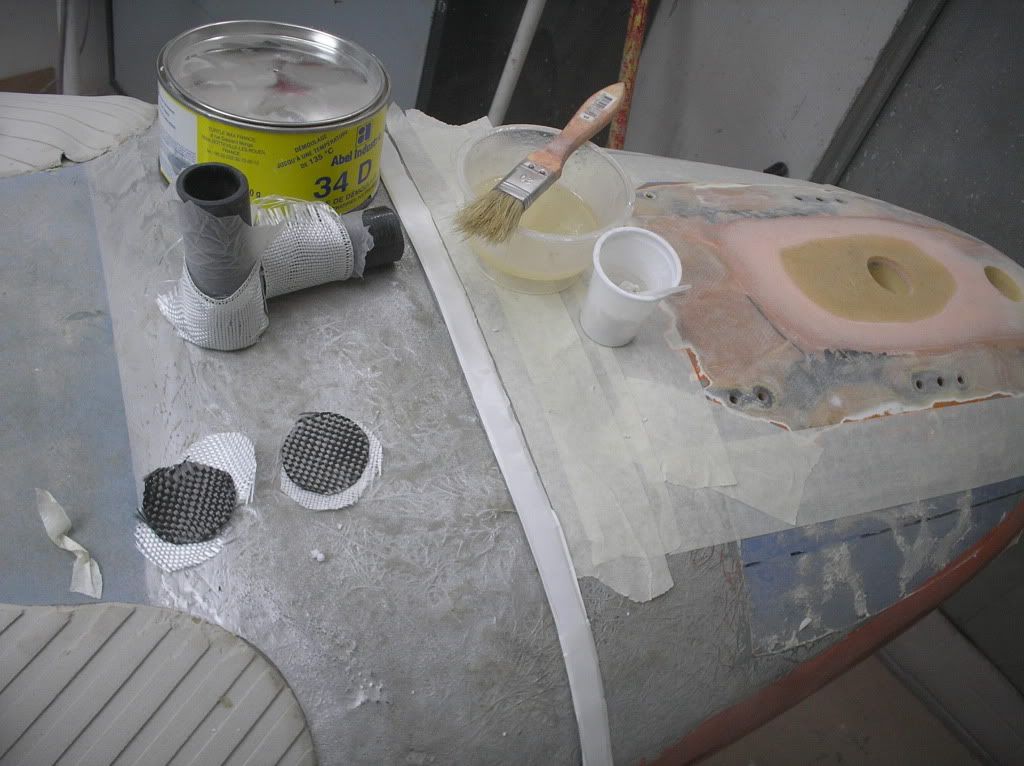
Pintado con resina de los alojamientos, relleno con resina espesada con microbalones, inserción del laminado del fondo y el de los machos con el laminado a su alrededor, presión con sacos de arena durante 48 horas.
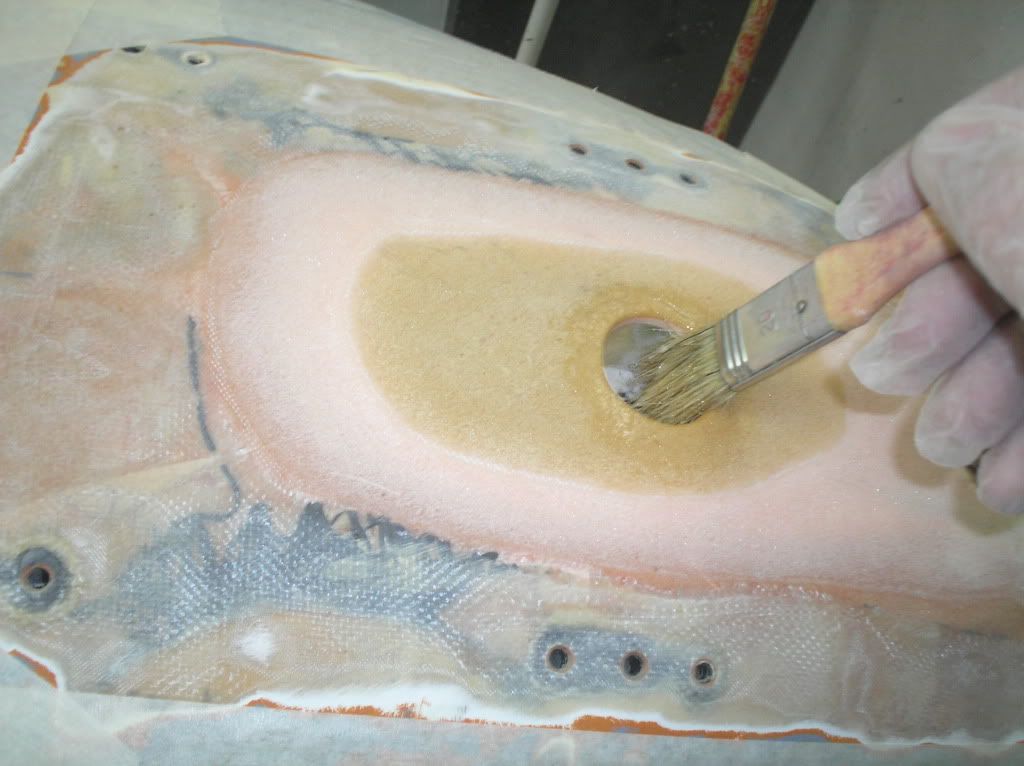
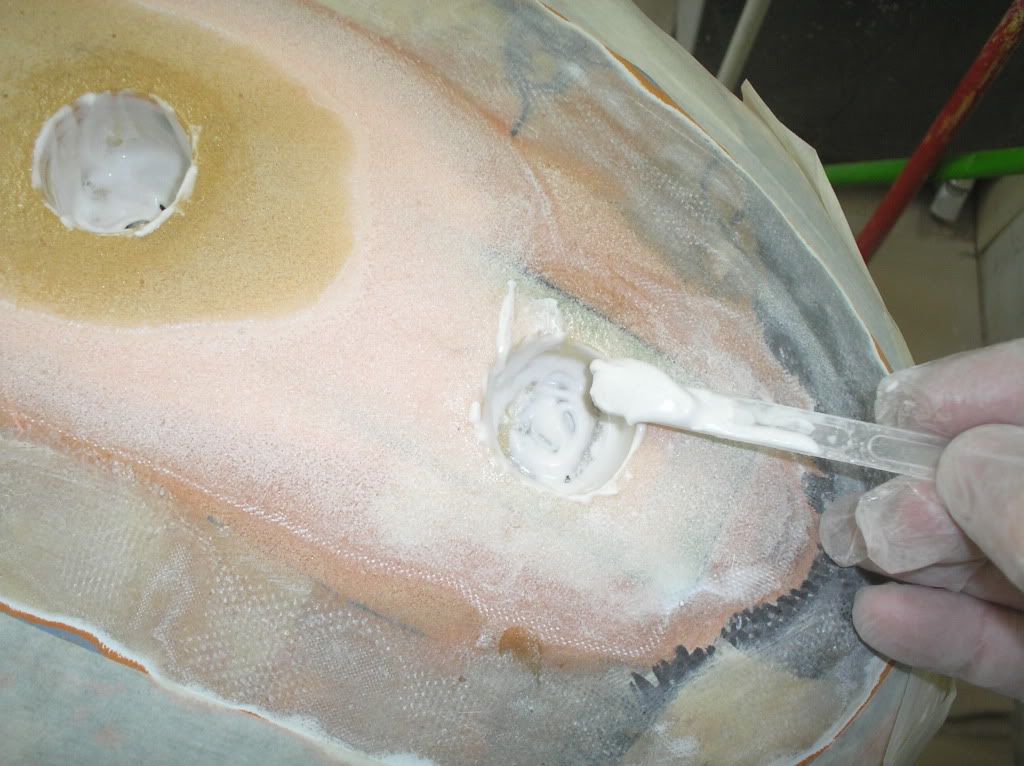
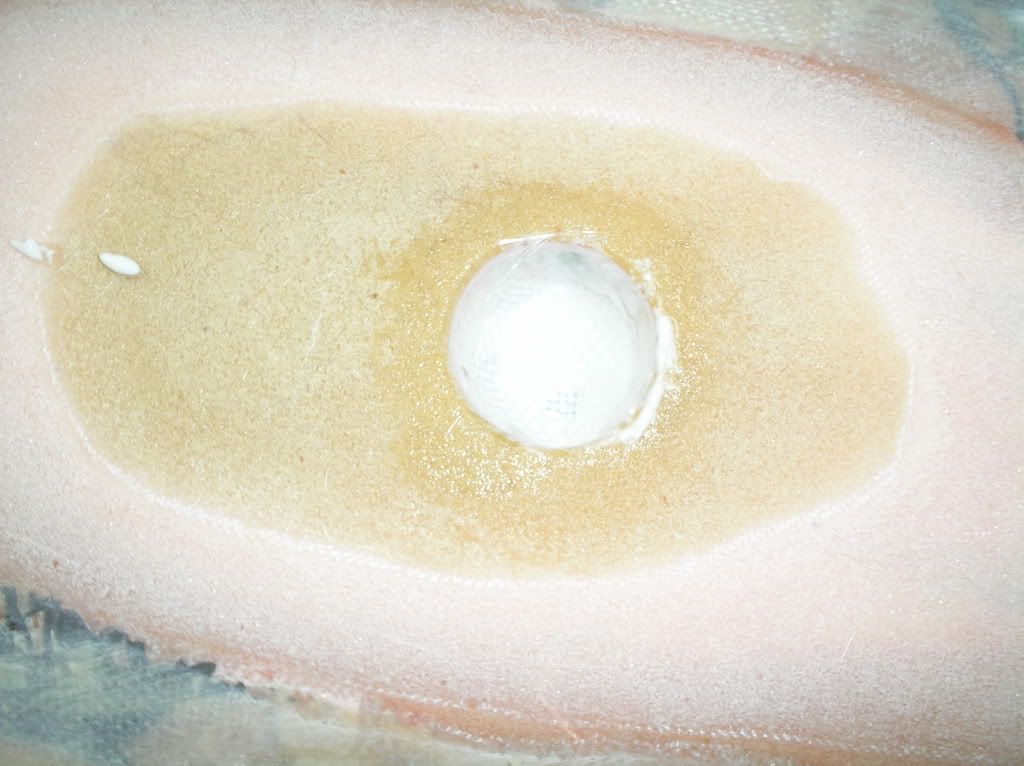
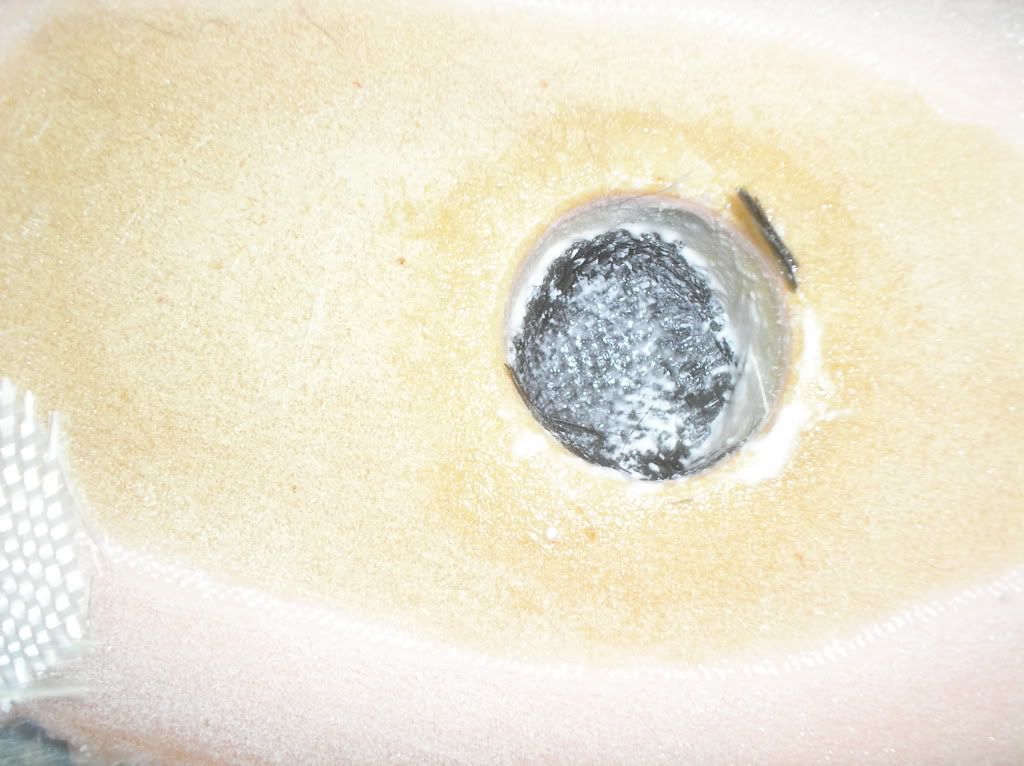
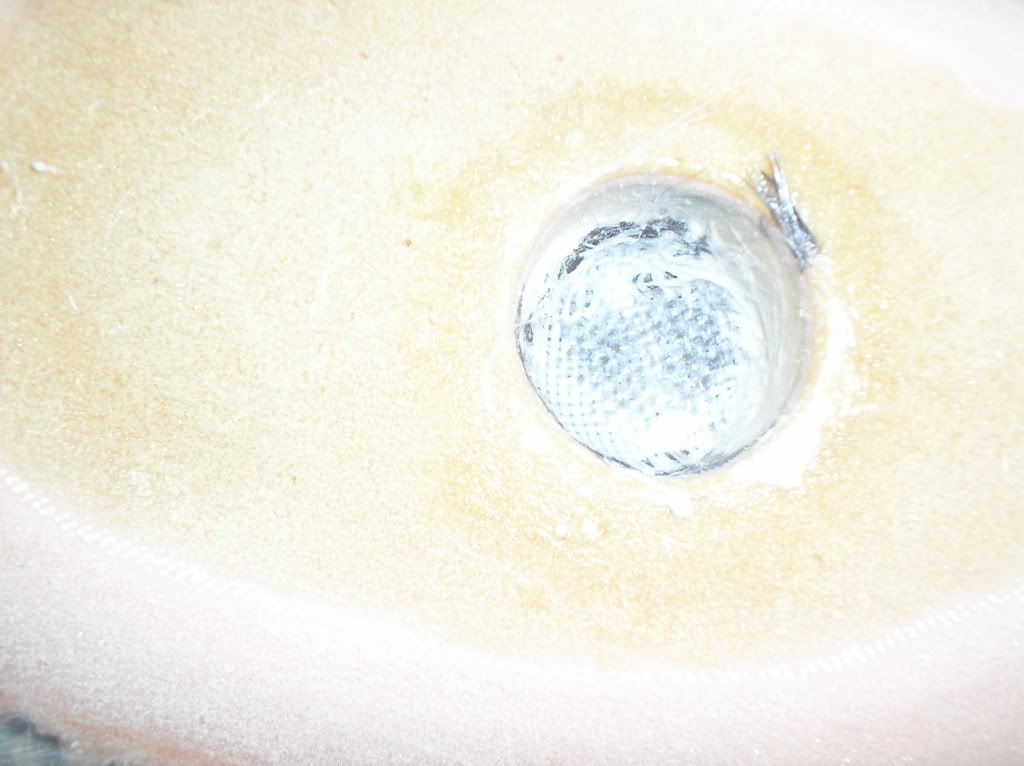
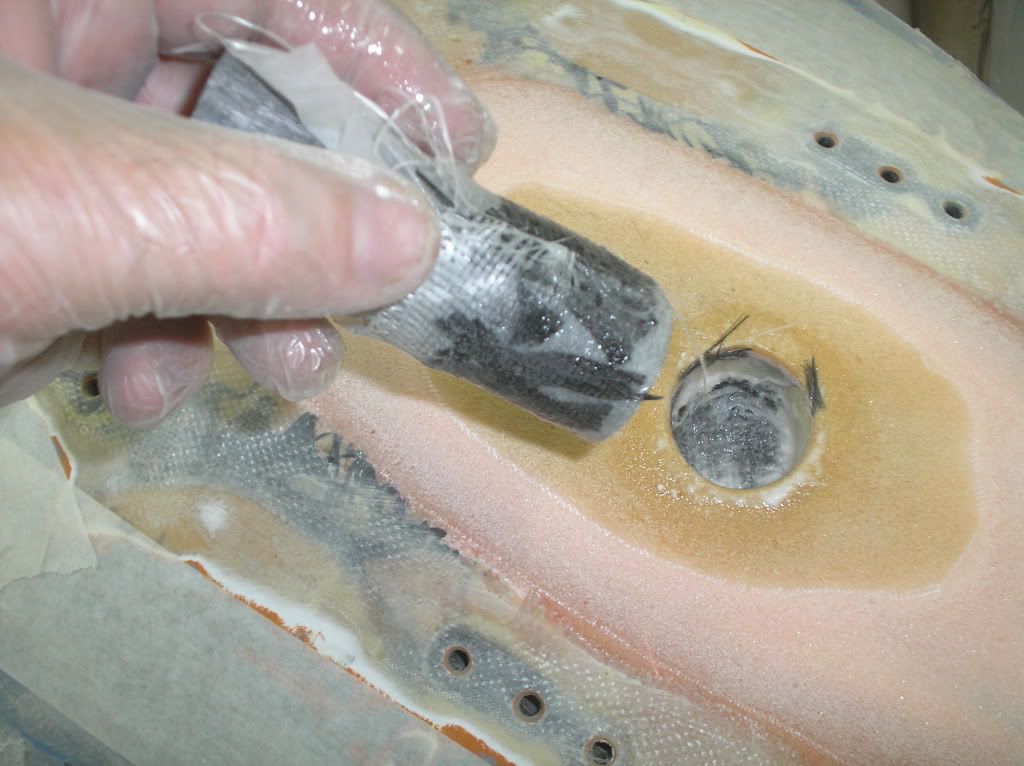
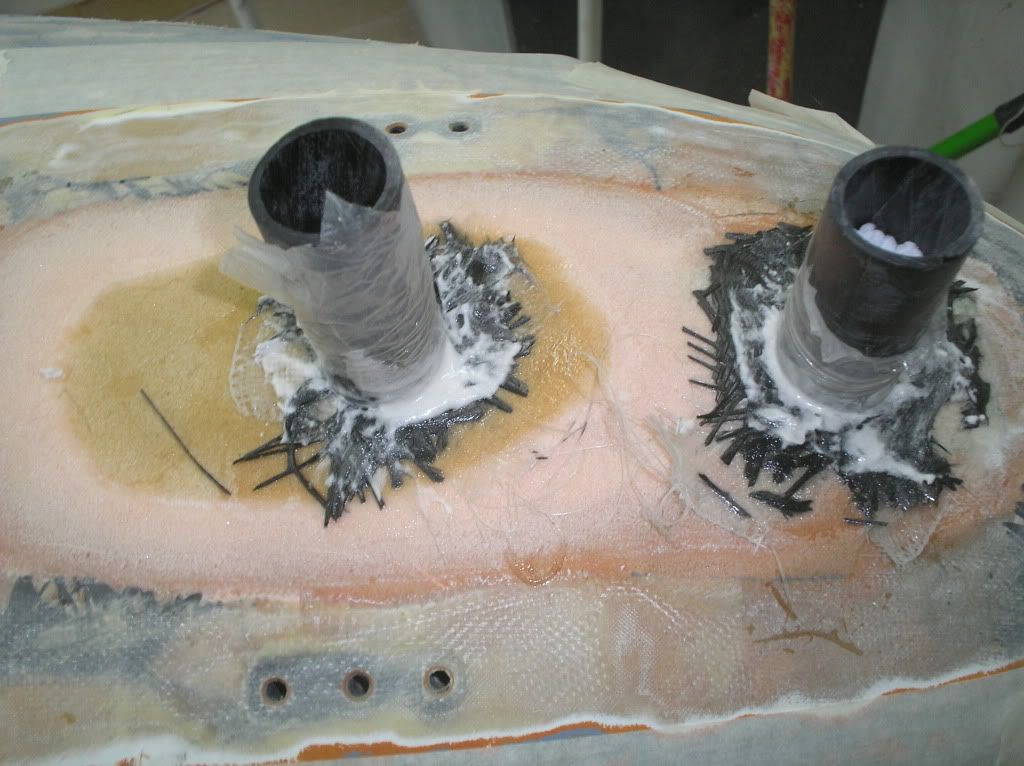
Resultado al extraer los machos.
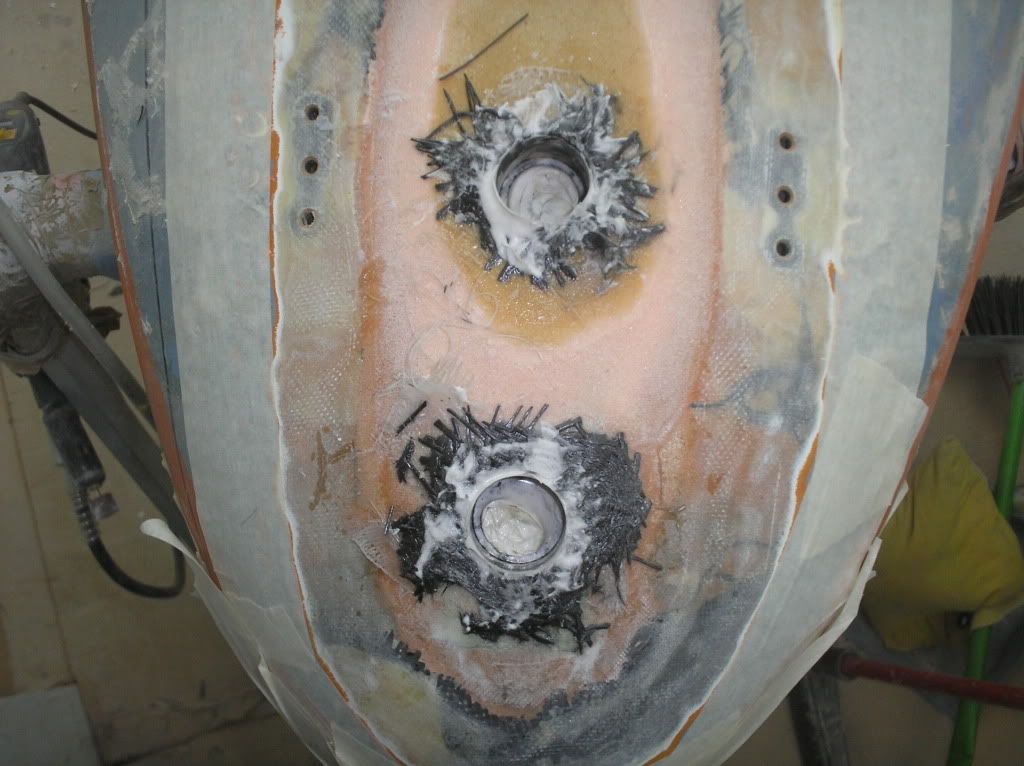
Preparación del laminado exterior en carena y cubierta, una vez lijada y nivelada la boca de caja de aleta: En carena pintamos el contorno de la caja con liquido acoplador de plásticos para conseguir mejor adherencia con resina y la minados, pintamos toda la zona con resina, tapamos el poro y nivelamos con resina espesada con microbalones, laminamos Cuatro paños alternos en carbono y fibra de vidrio de menor a mayor (carbono 180grs sarga, fibra de vidrio 165gr, carbono 175gr satin y fibra de vidrio 80gr. Cubrimos con tejido sangrador-pelable PEEL-PLY, manta de absorción y sujetamos con cinta de carrocero para dar la vuelta a la tabla y trabajar en cubierta.
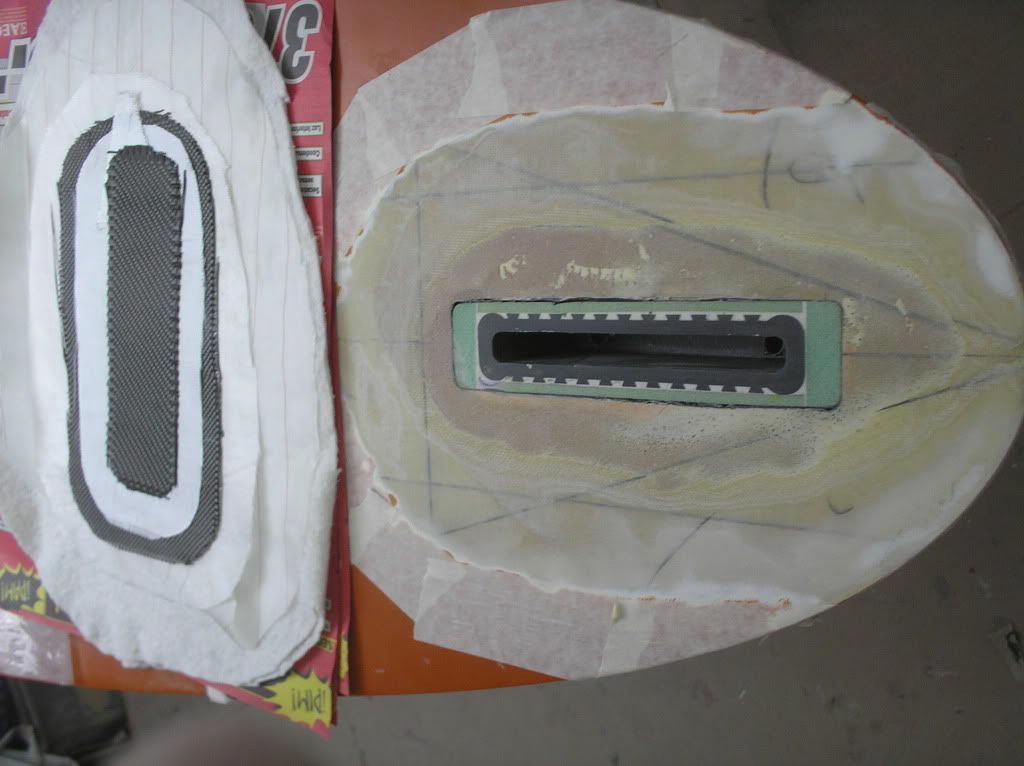
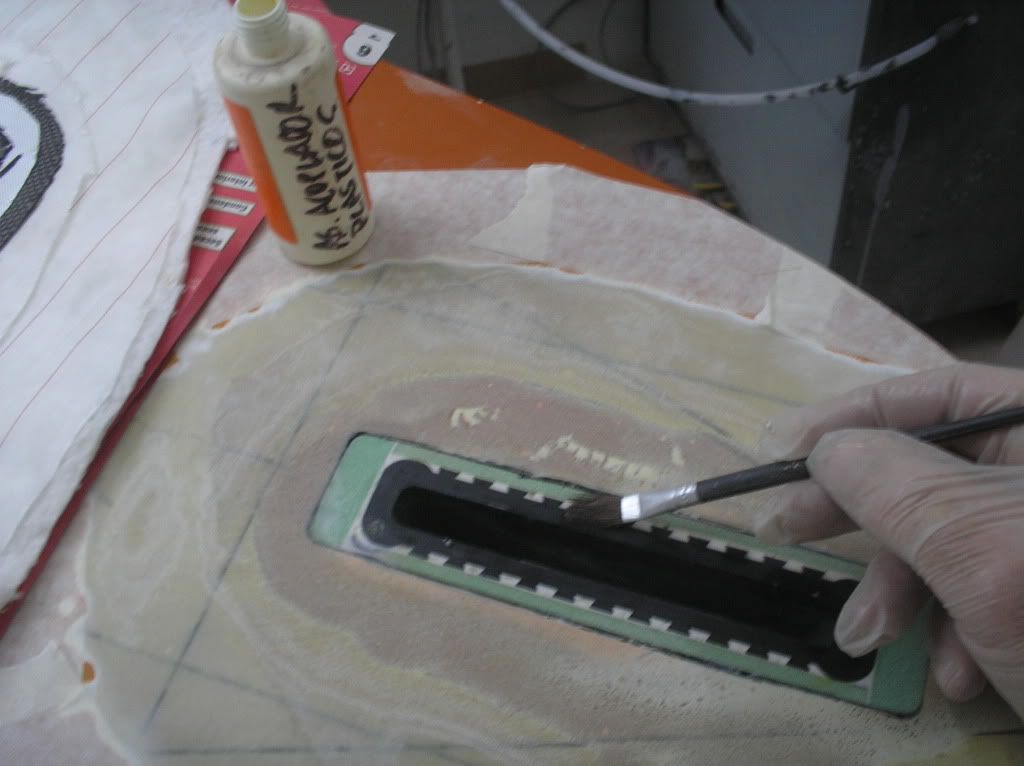
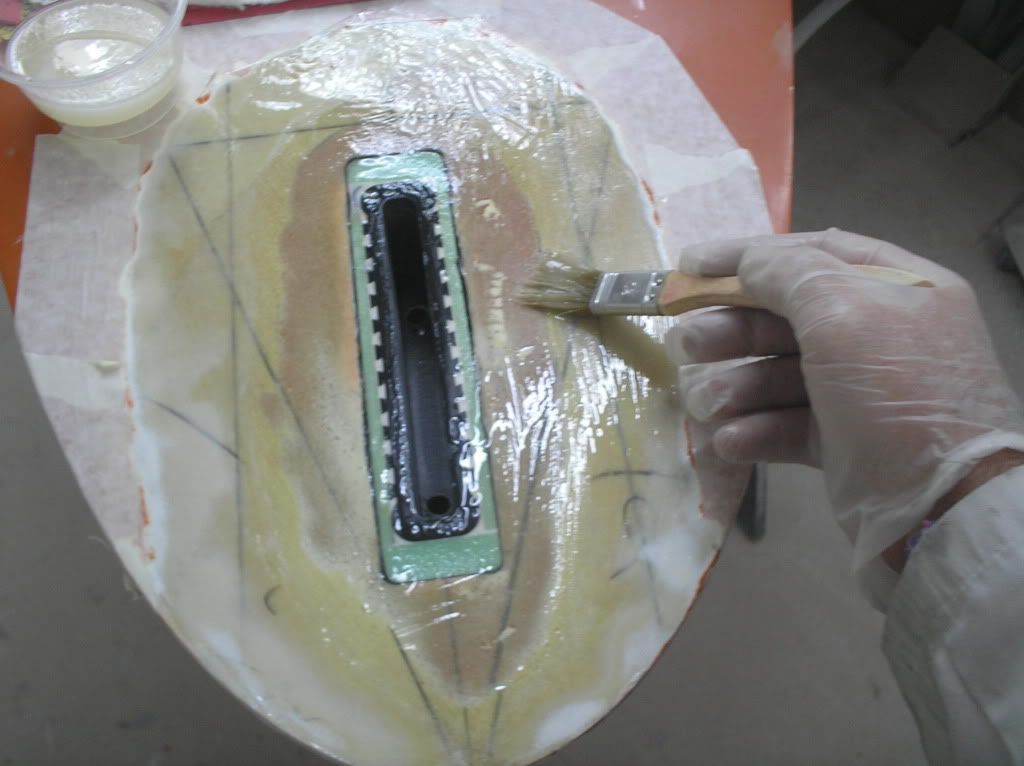
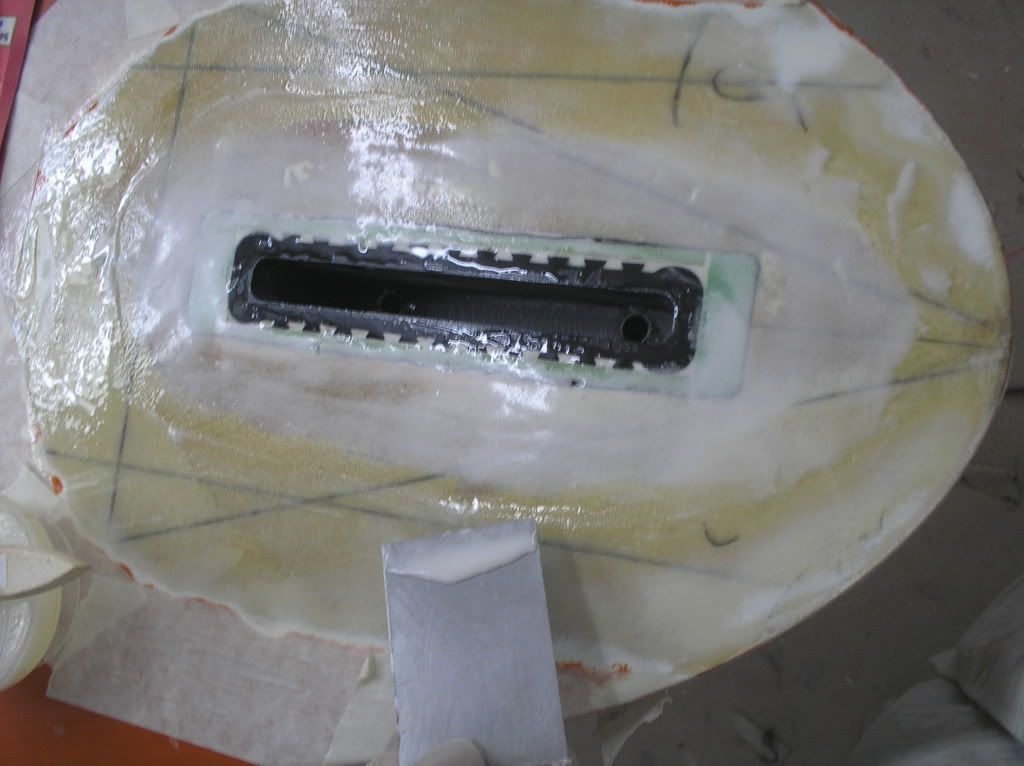
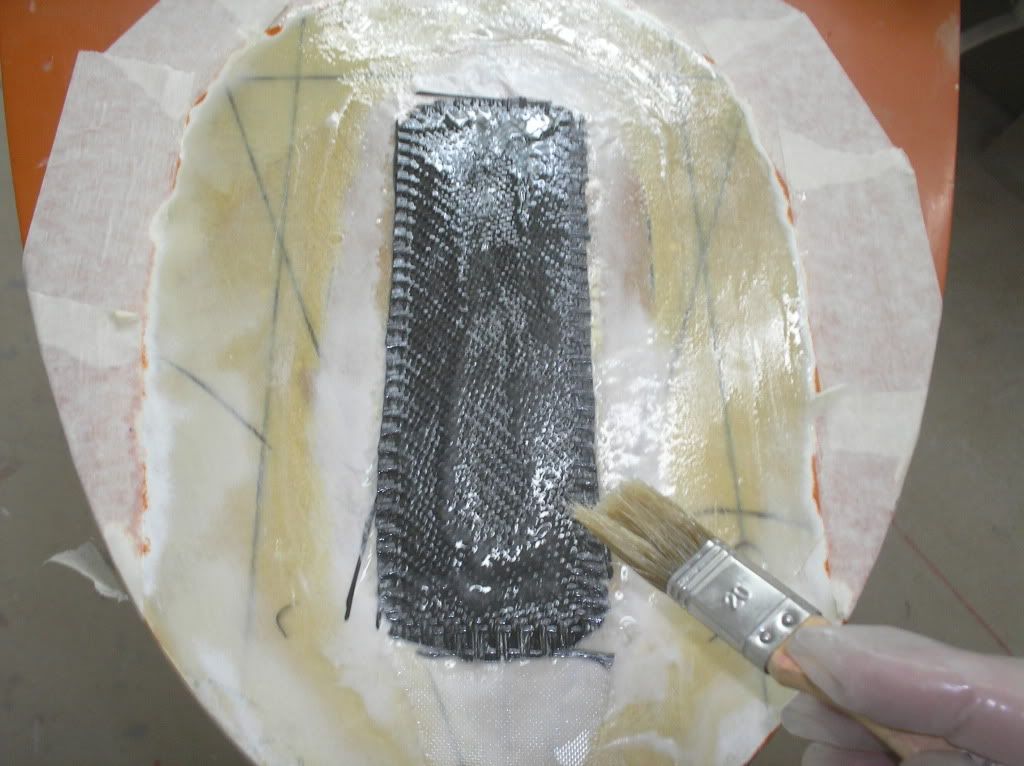
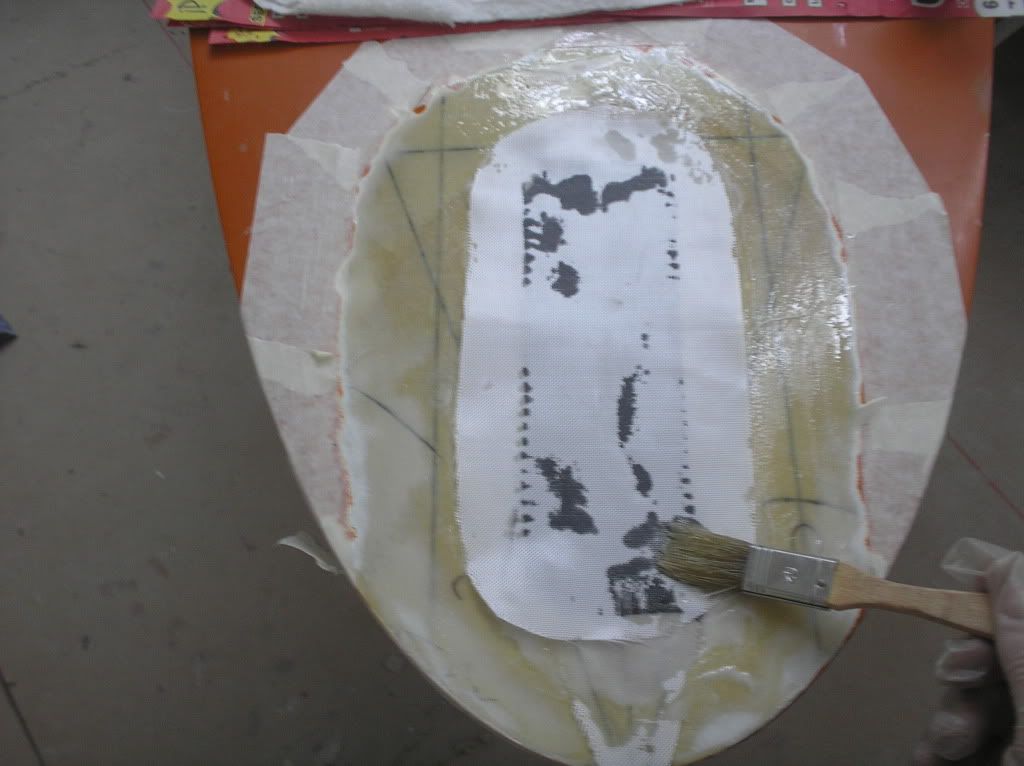
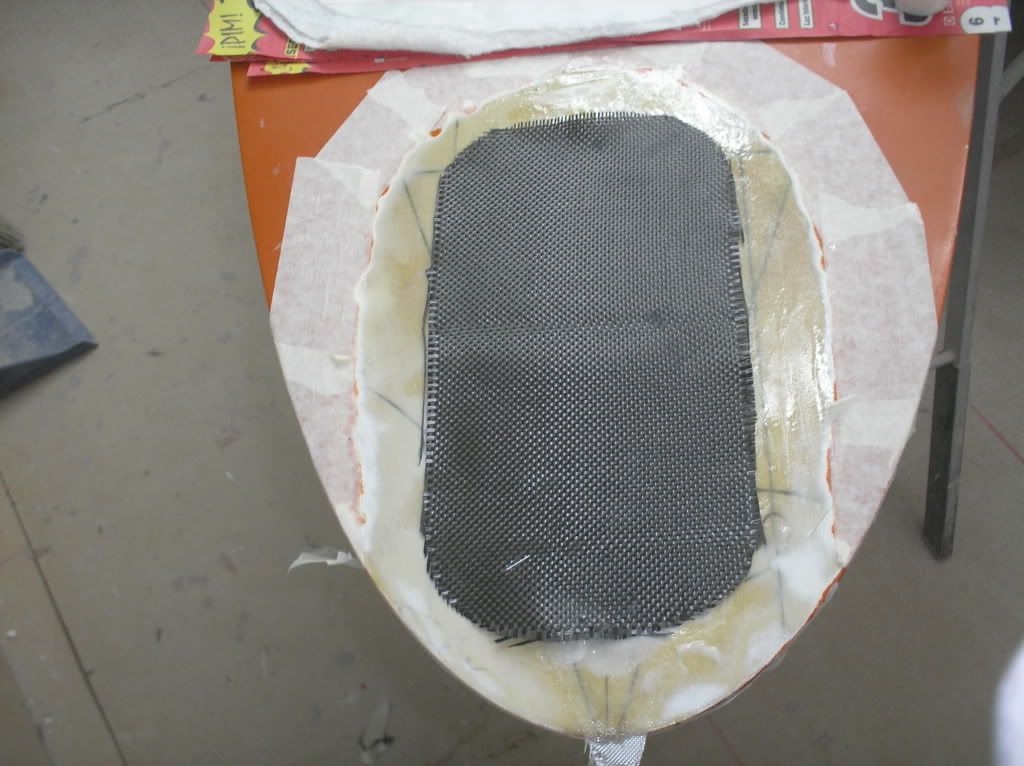
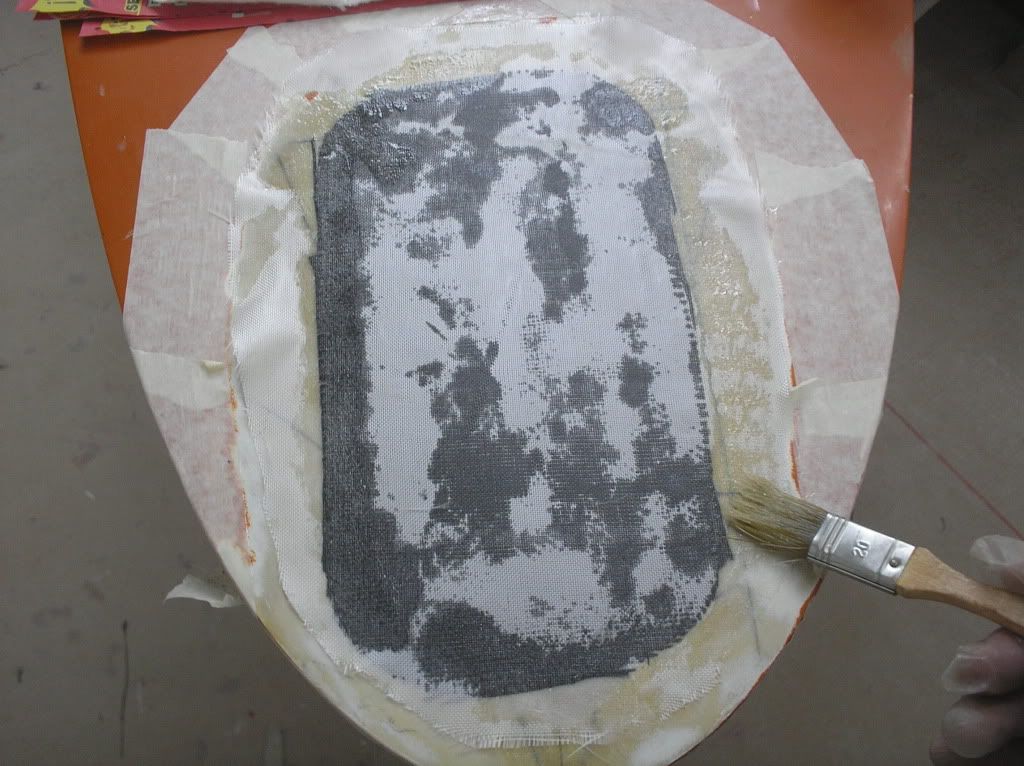
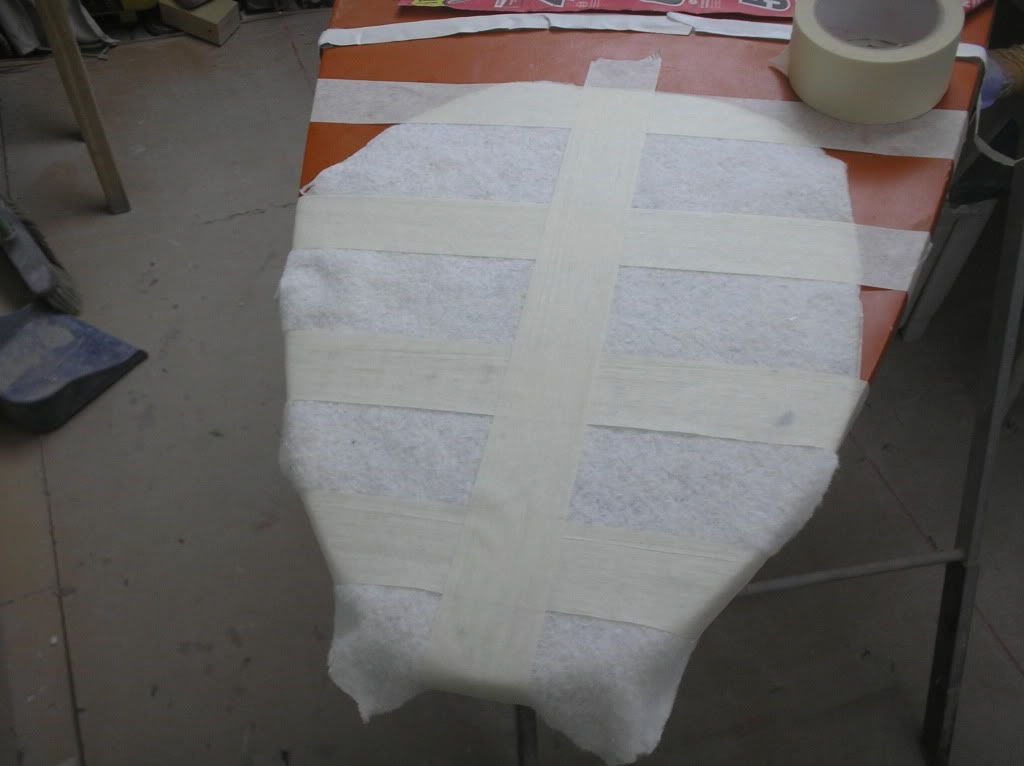
Reposición laminado en cubierta: Preparación del laminado, pintado con resina y tapado del poro con resina espesada con microbalones, laminado en fibra de vidrio 165grs a la que hacemos unos cortes a la altura de los alojamientos de tornillo, laminado en sarga 200gr, hacemos los cortes, laminado en fibra de vidrio 80gr, hacemos los cortes, ponemos encima Tejido sangrador-pelable PEEL-PLY, manta de absorción y embolsamos cubierta y carena, depresión de 0,6 con bomba de vacío durante 8 horas aplicando calor alternativamente en carena y cubierta mediante bombilla de rayos infrarrojos durante 4 horas, dejo endurecer la resina de 48 horas.
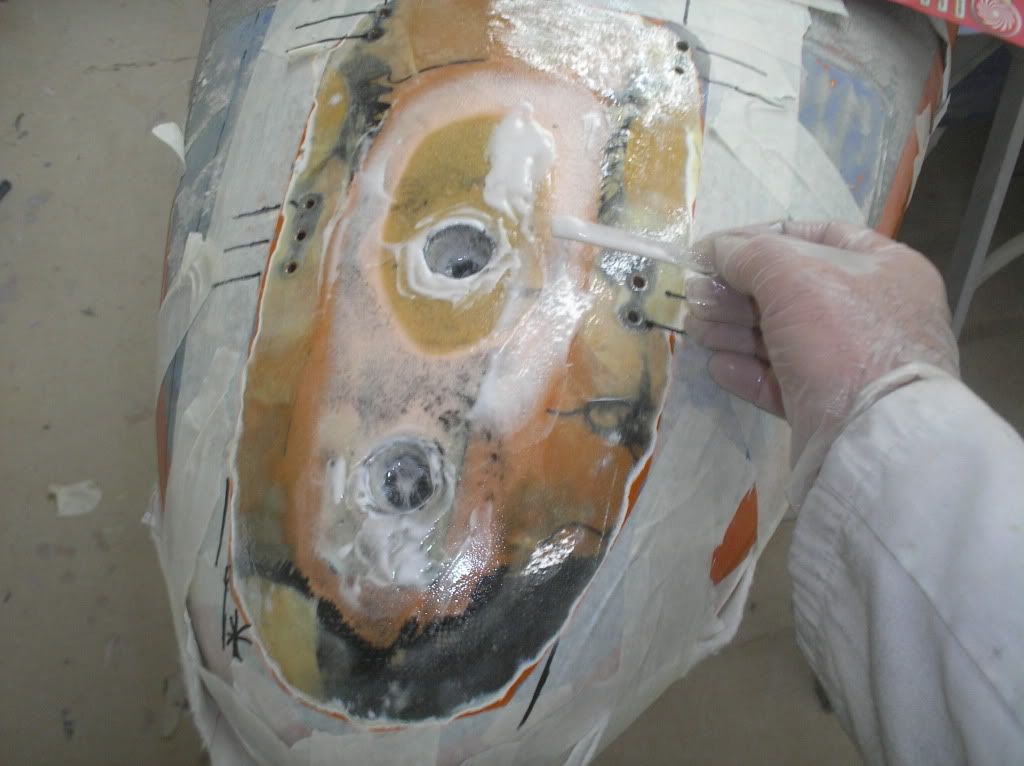
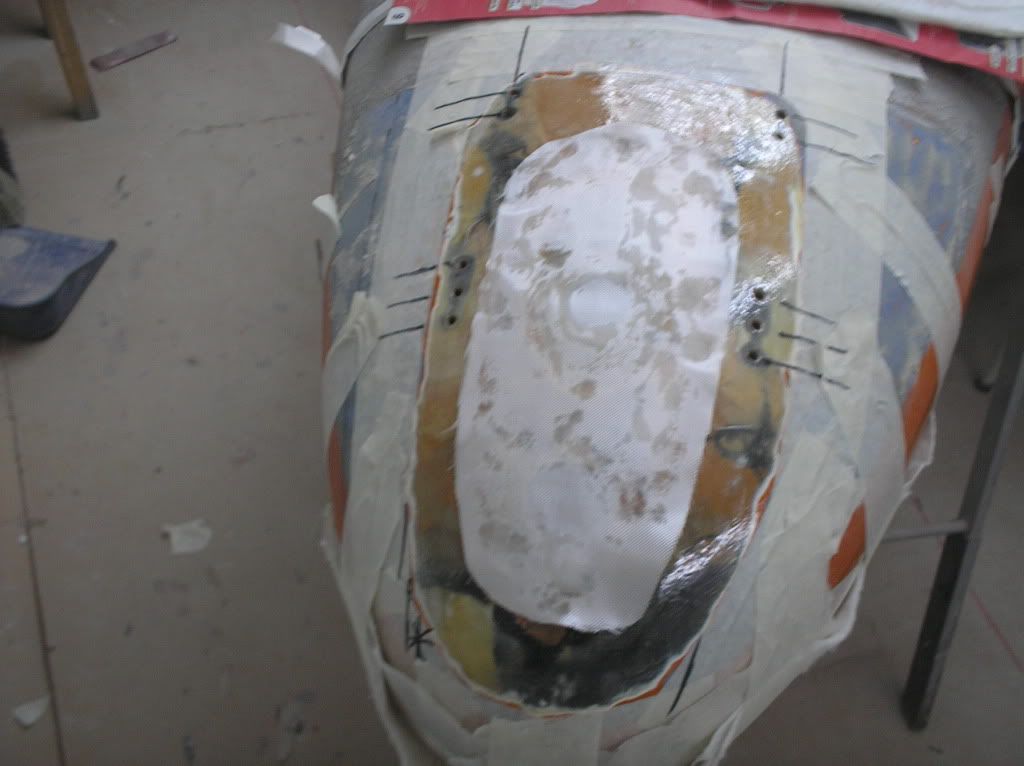
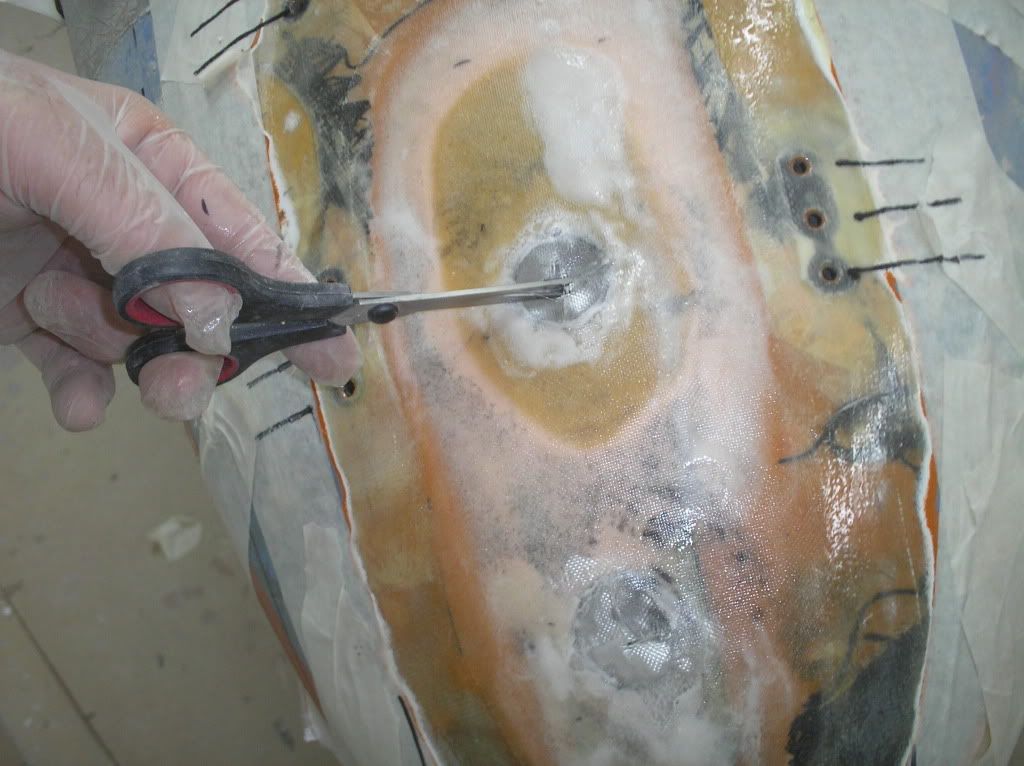
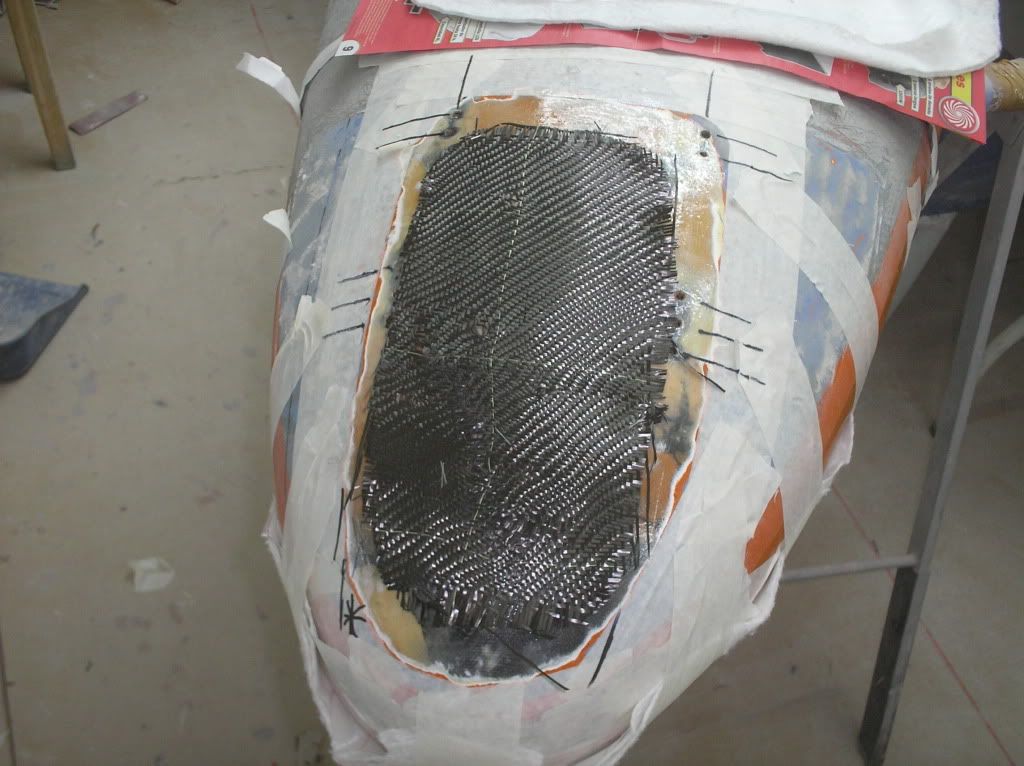
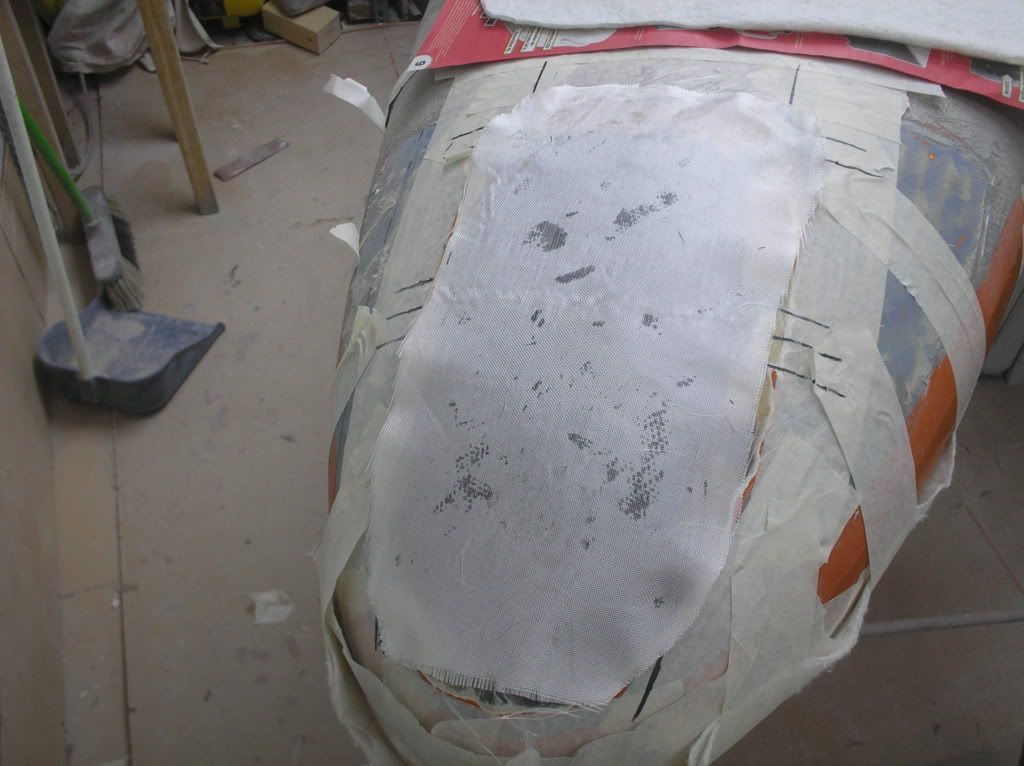
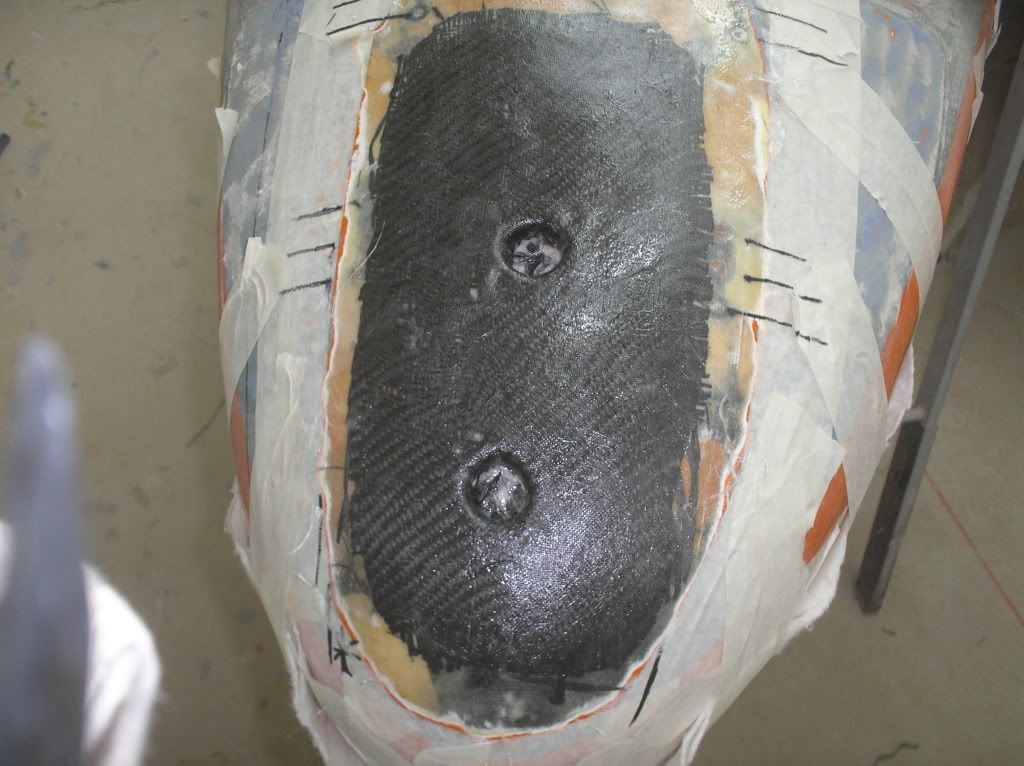
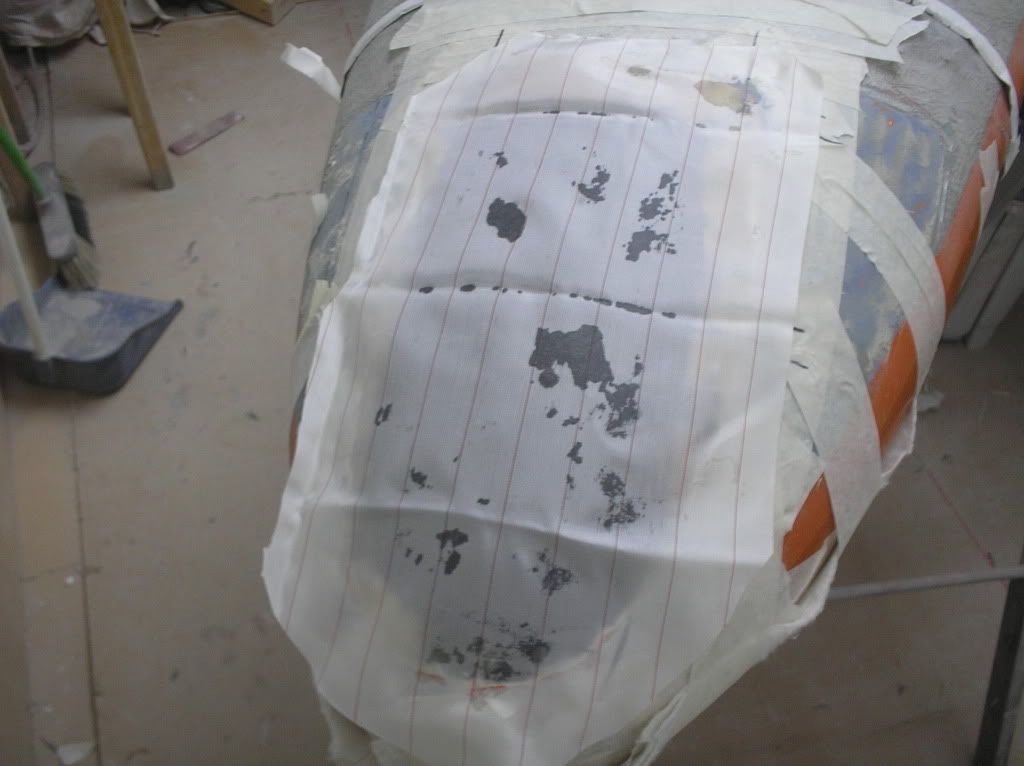
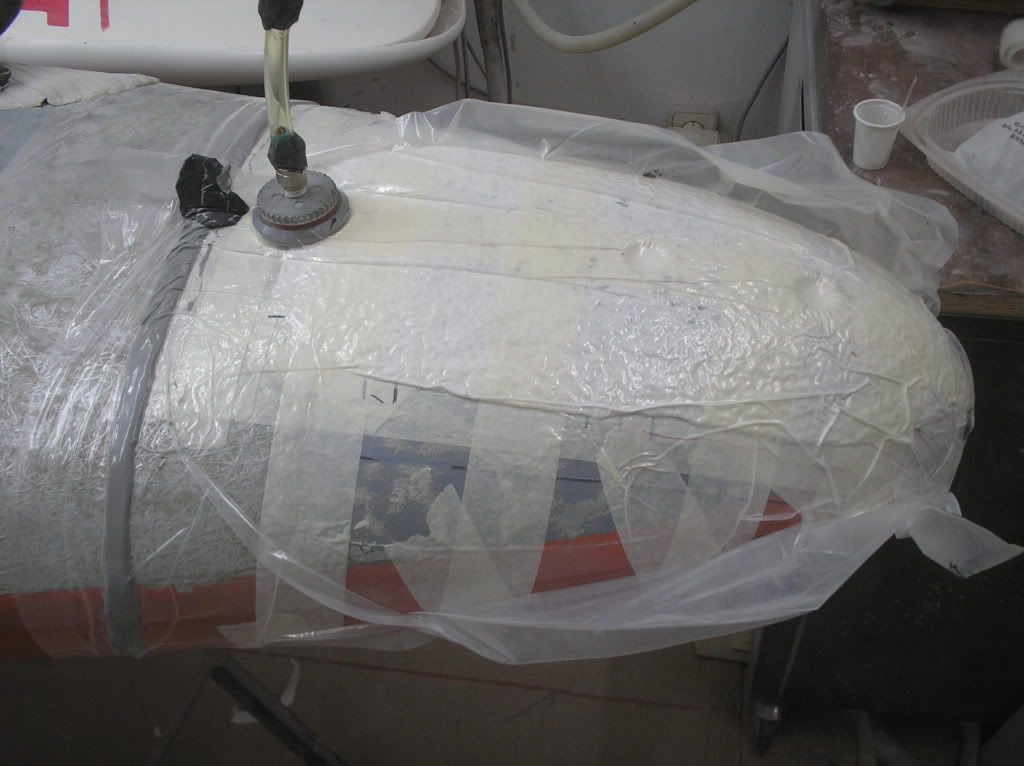
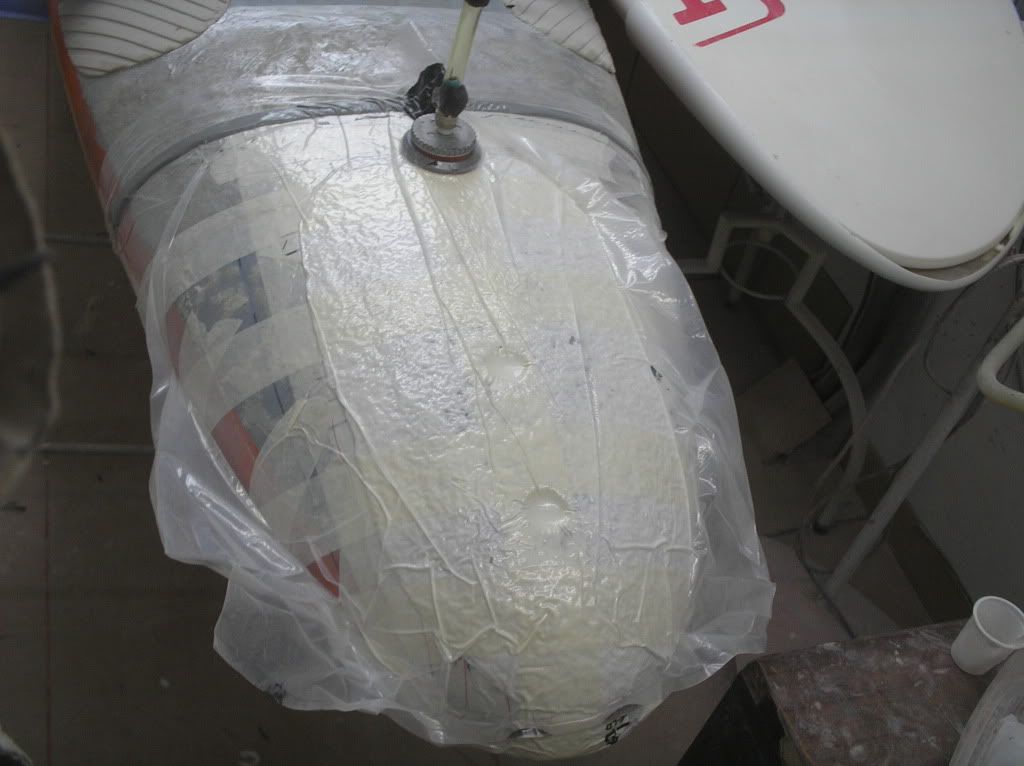
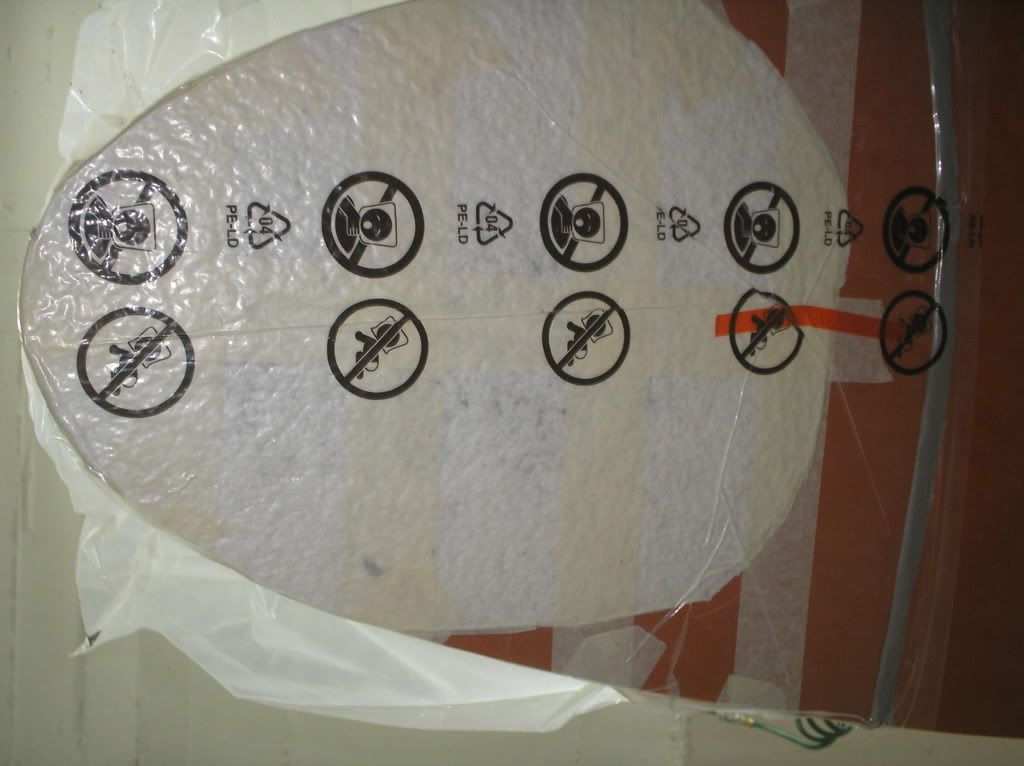
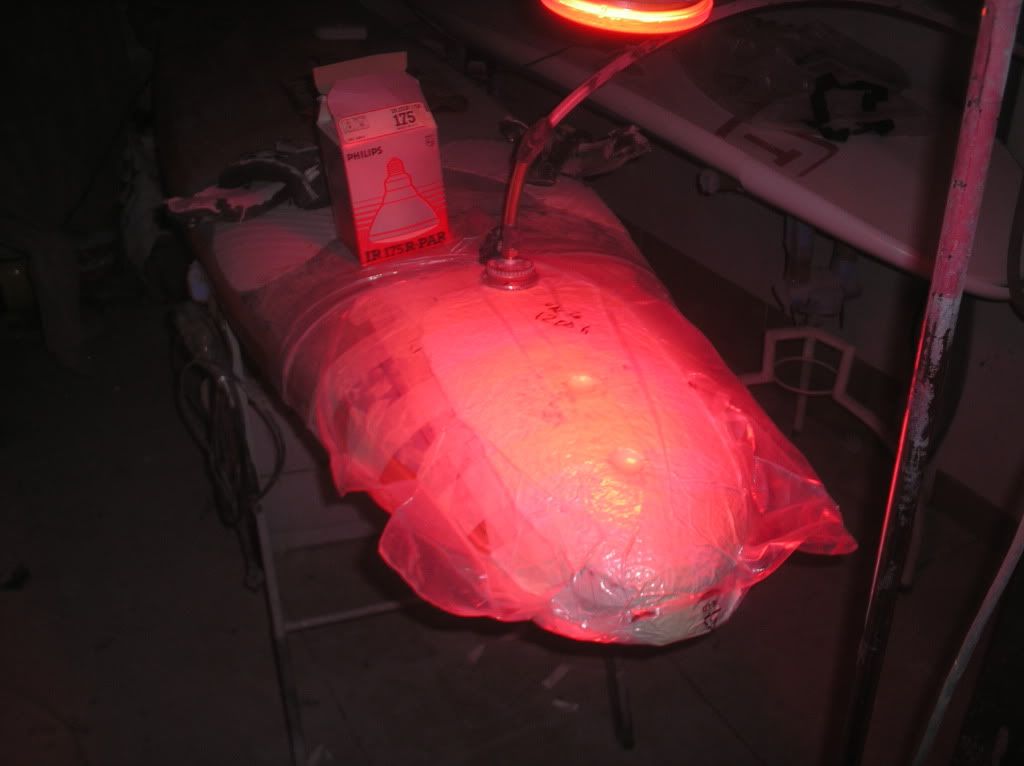
Fresado del laminado en la entrada en la caja de aleta y esmerilado del laminado con dremel para evitar que la aleta al salir levante el laminado en los vértices.
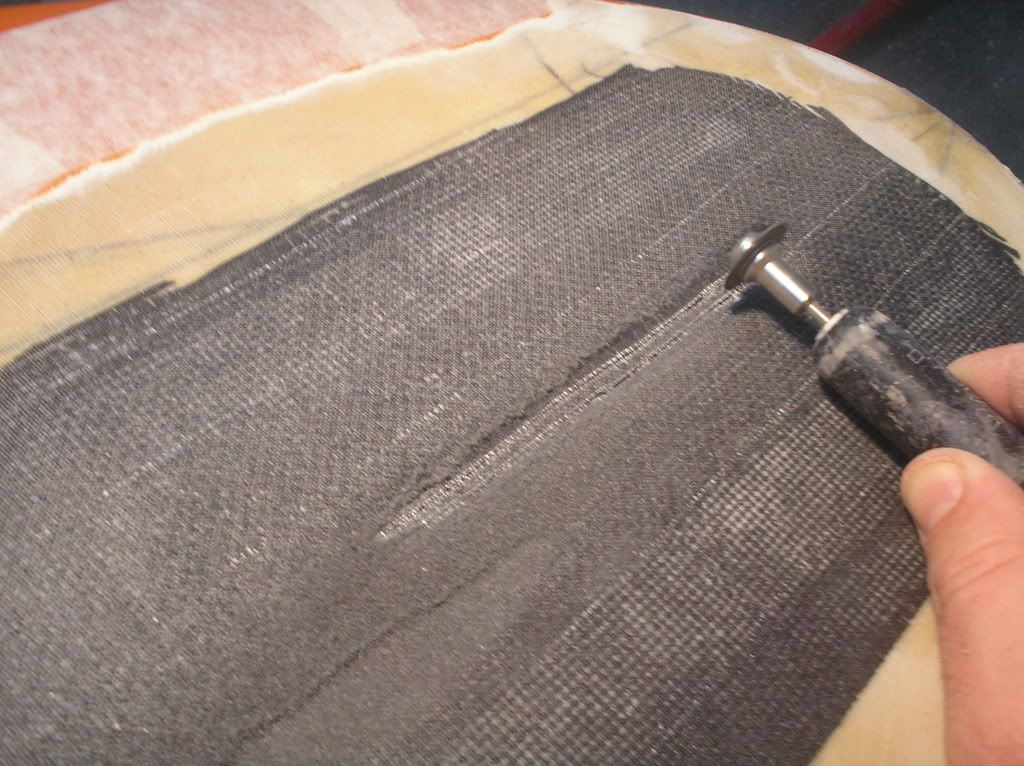
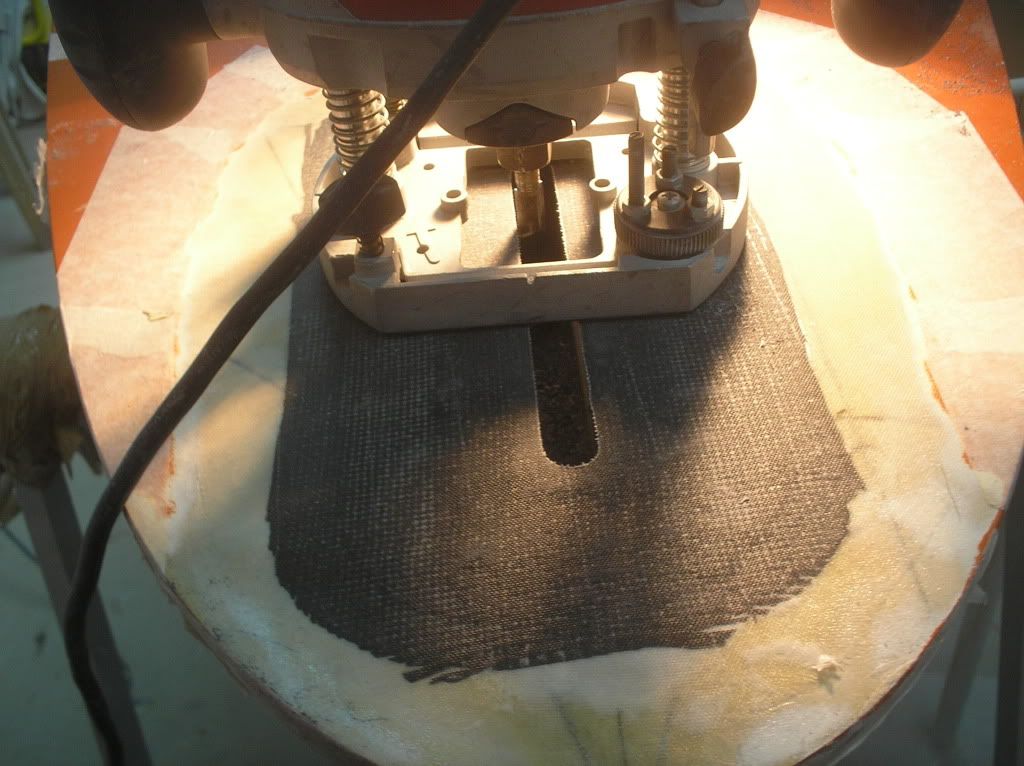
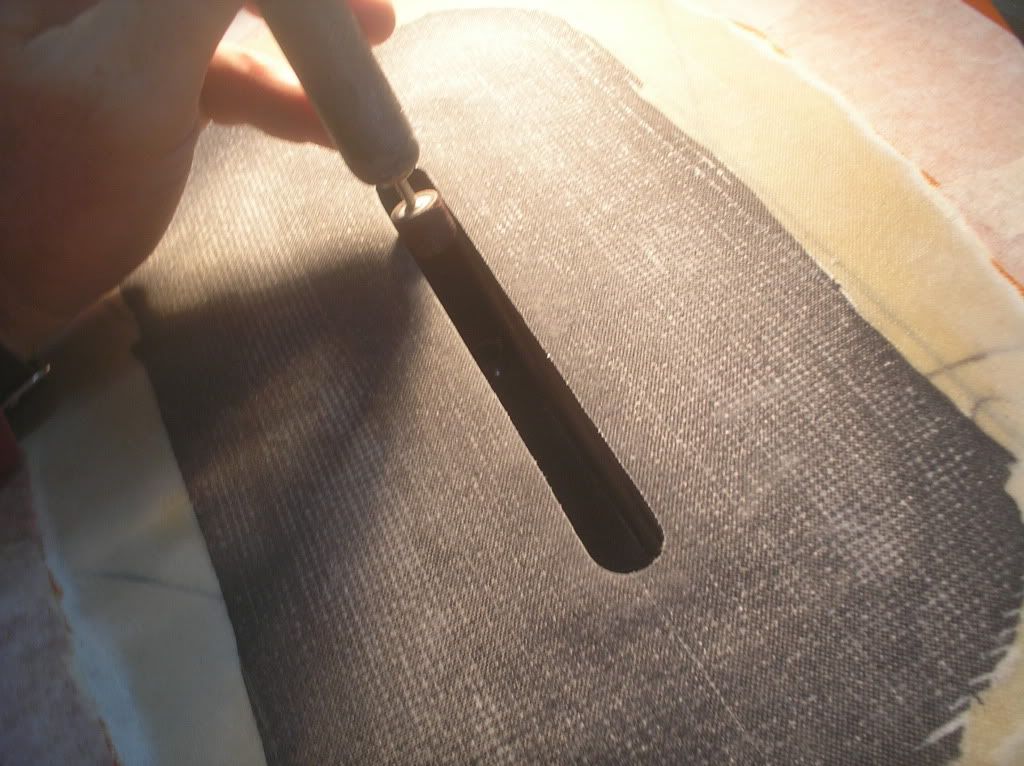
Lijado del laminado sobrante en cubierta, se hacen los taladros en el fondo alojamientos tornillos, se taladra y avellanado taladros tornillos footstrps, tapado de poro y nivelar con pasta de carrocero, lijado al agua imprimación y pintura.
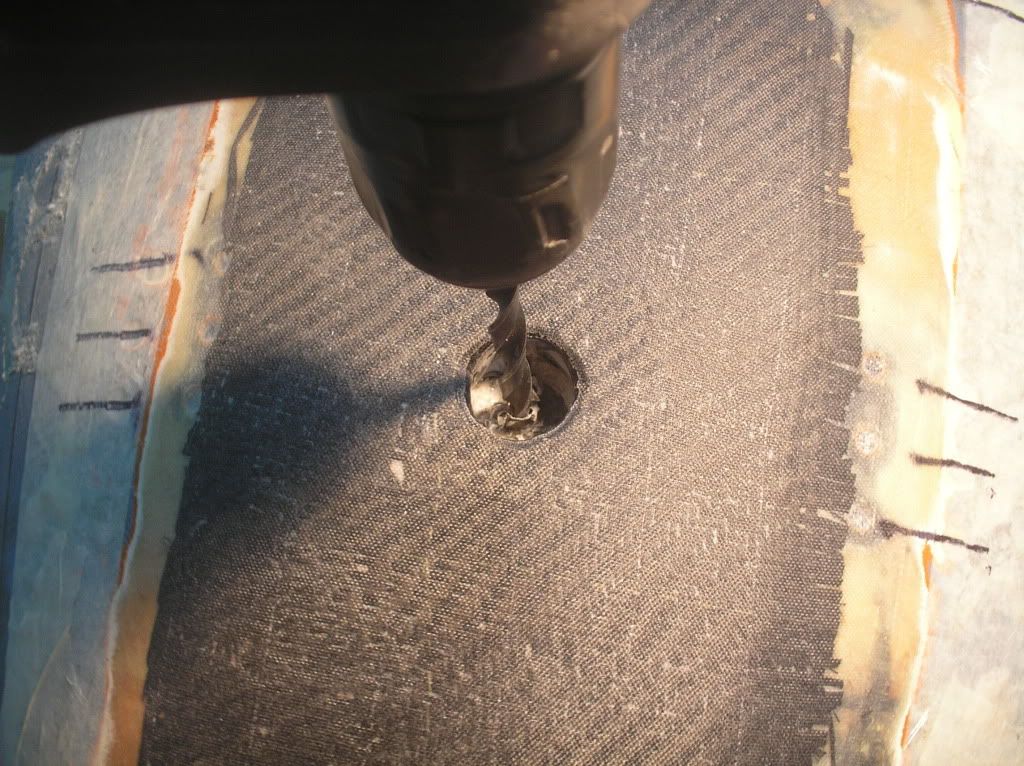
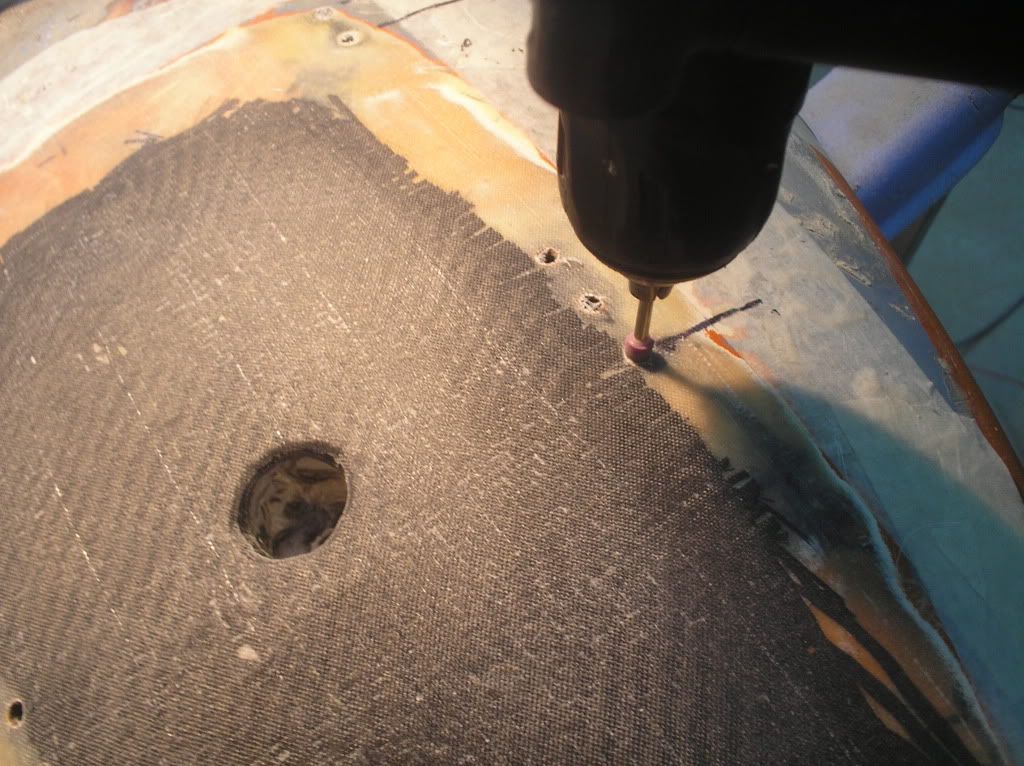
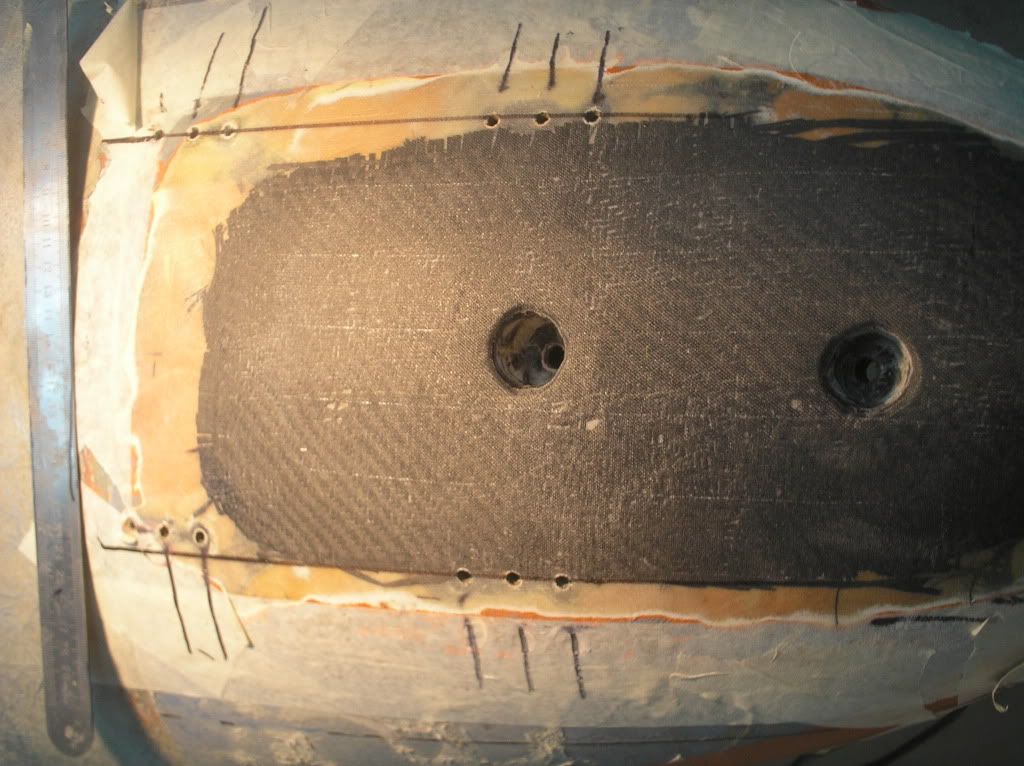
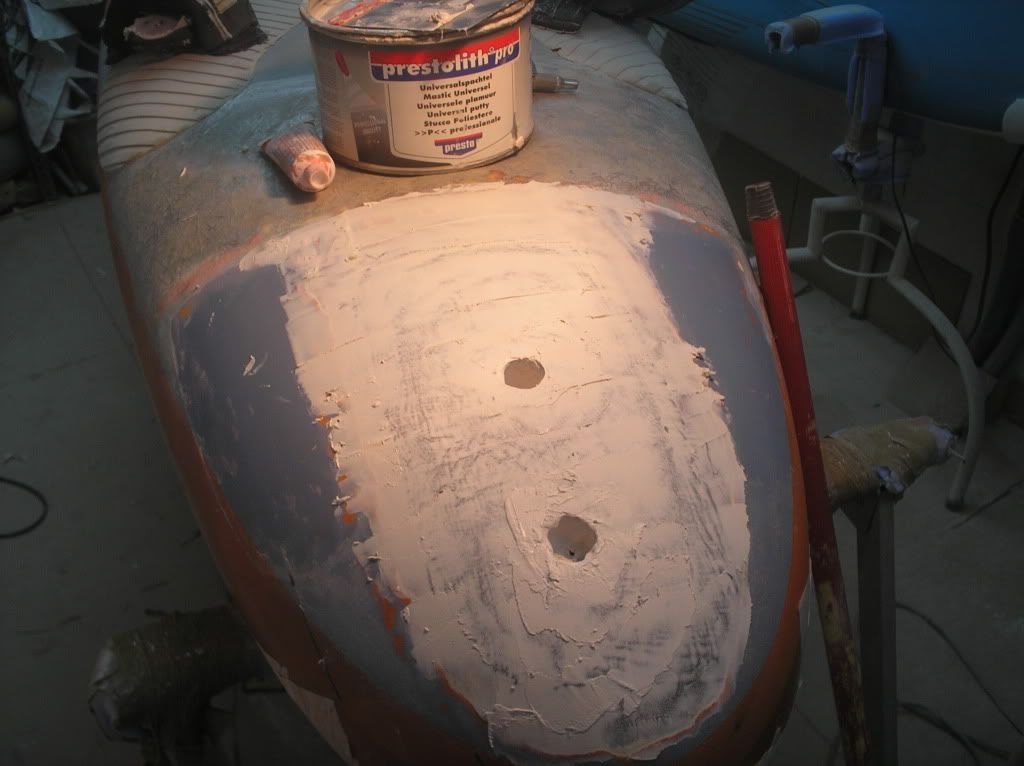
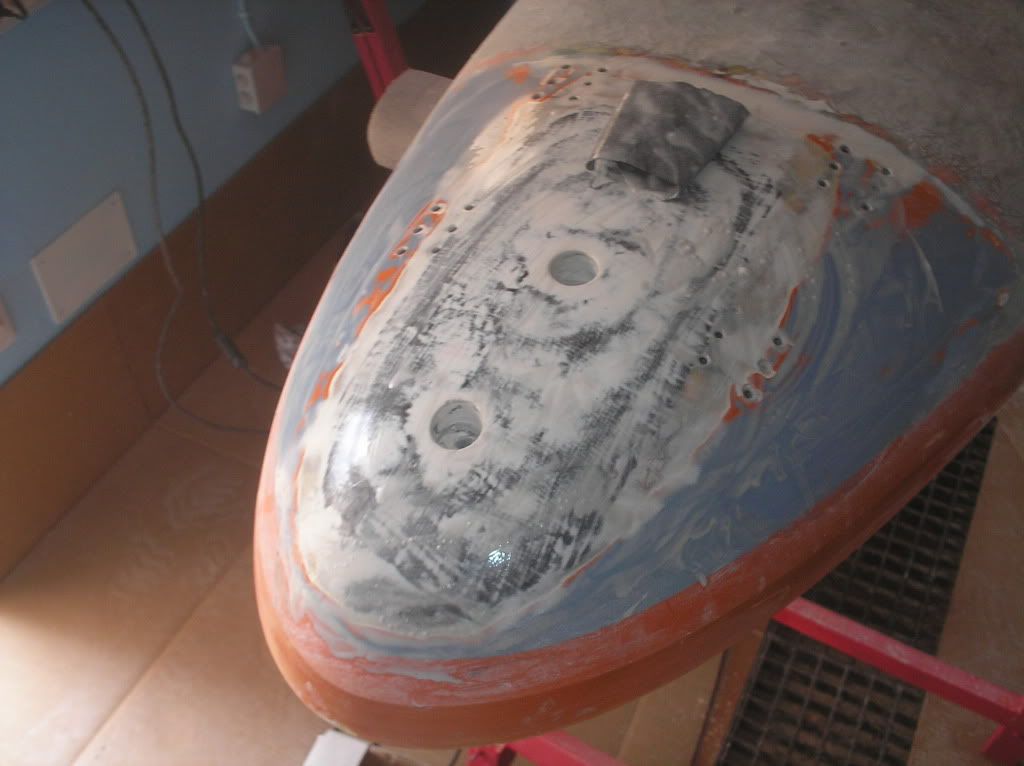
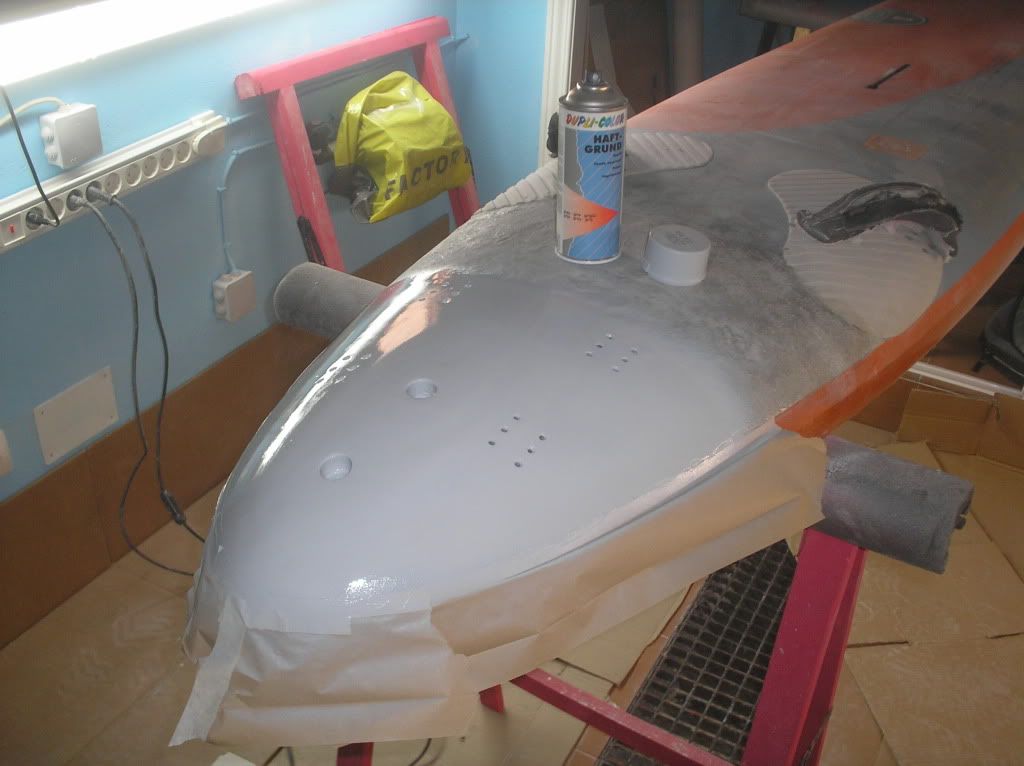
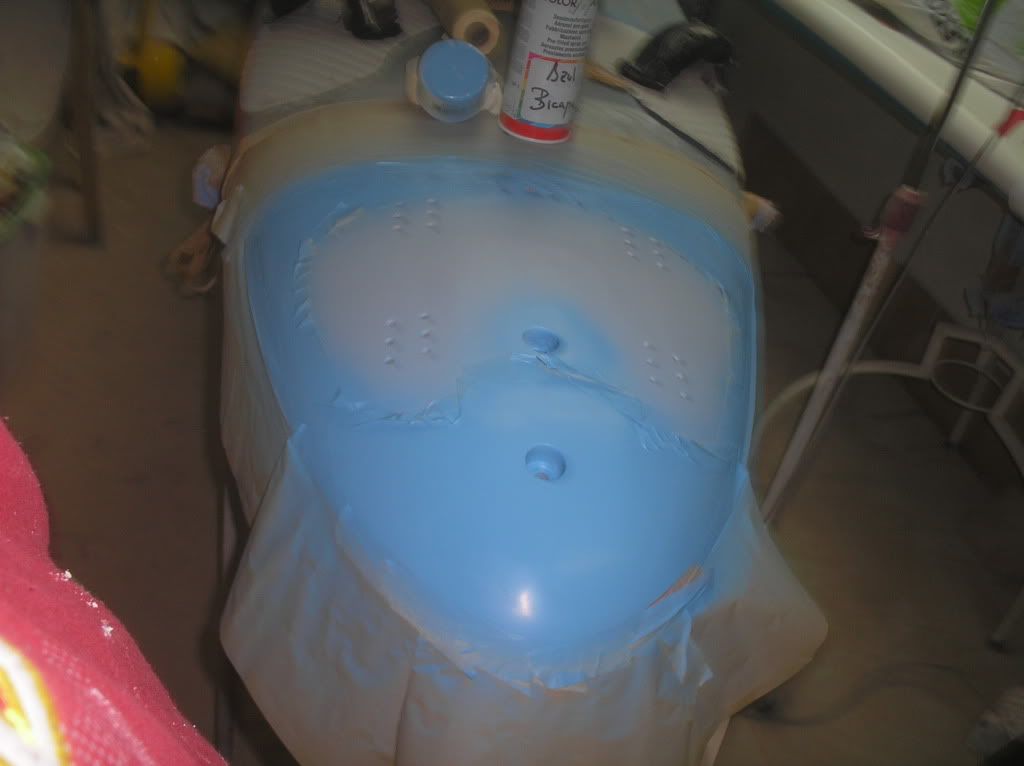
Colacacion de pad reciclado, señalado de taladros con remaches cortados y metidos en los huecos para que atraviesen el pad y poder señalar su sustitución, pegado de pad con cola de contacto especial poliestireno (esta no hace reaccionar la pintura al no tener disolventes), compresión con cinta de embalar y sacos de arena para garantizar el pegado, reposición del antideslizante con laca y polvo de corindón.
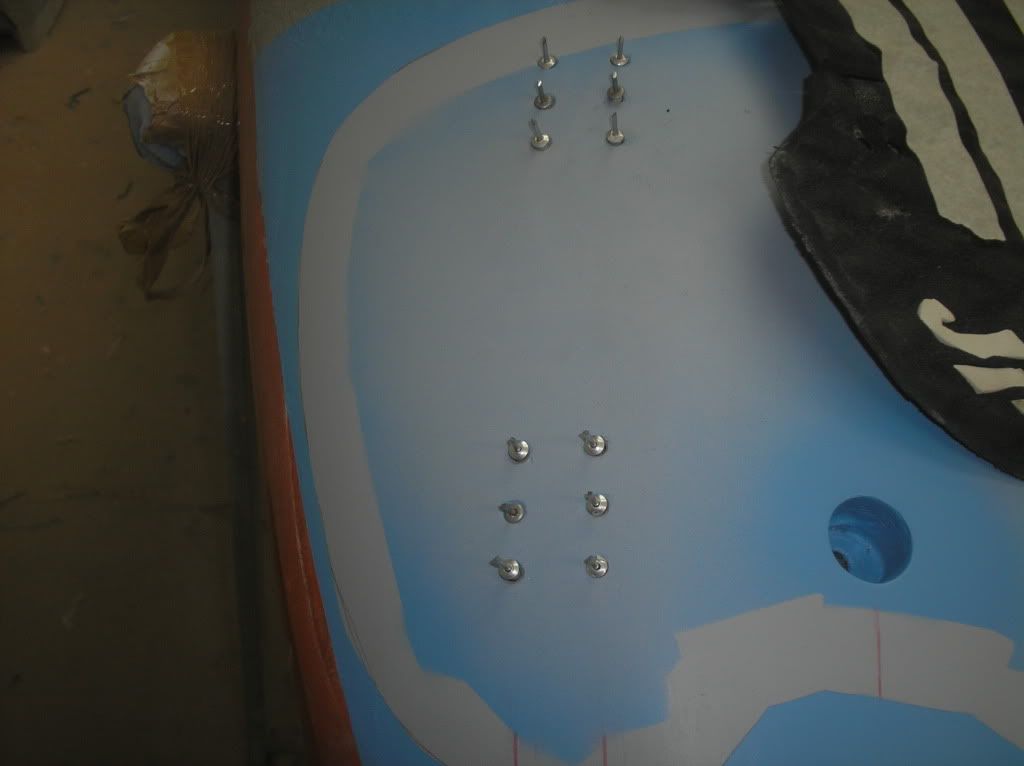
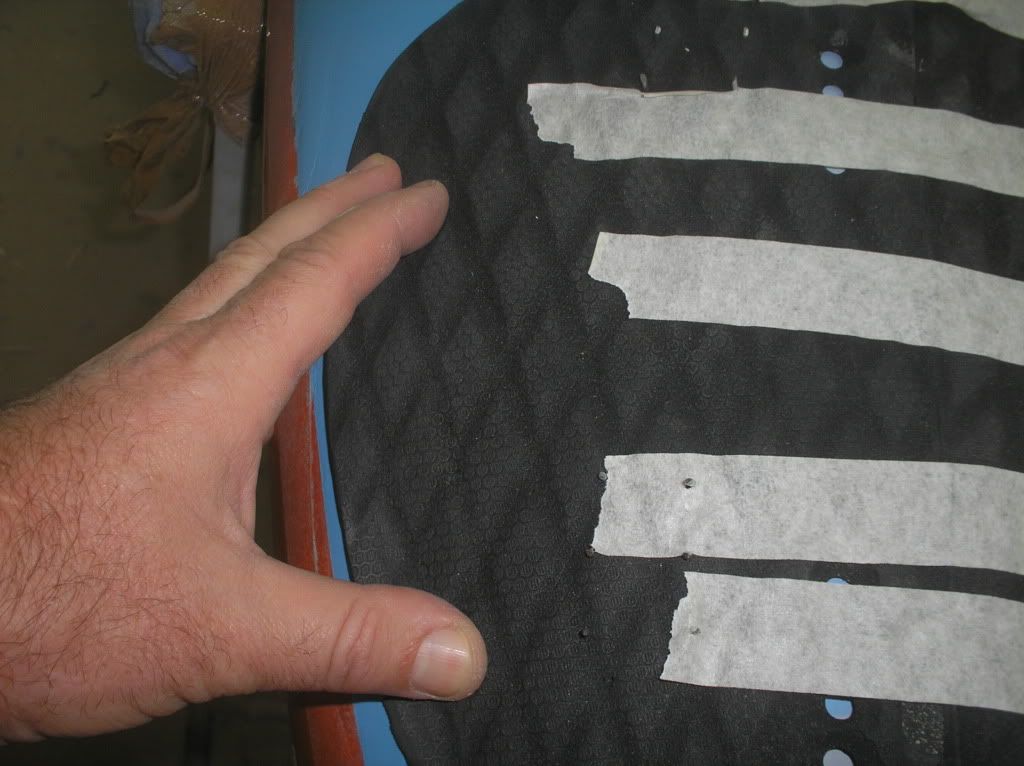
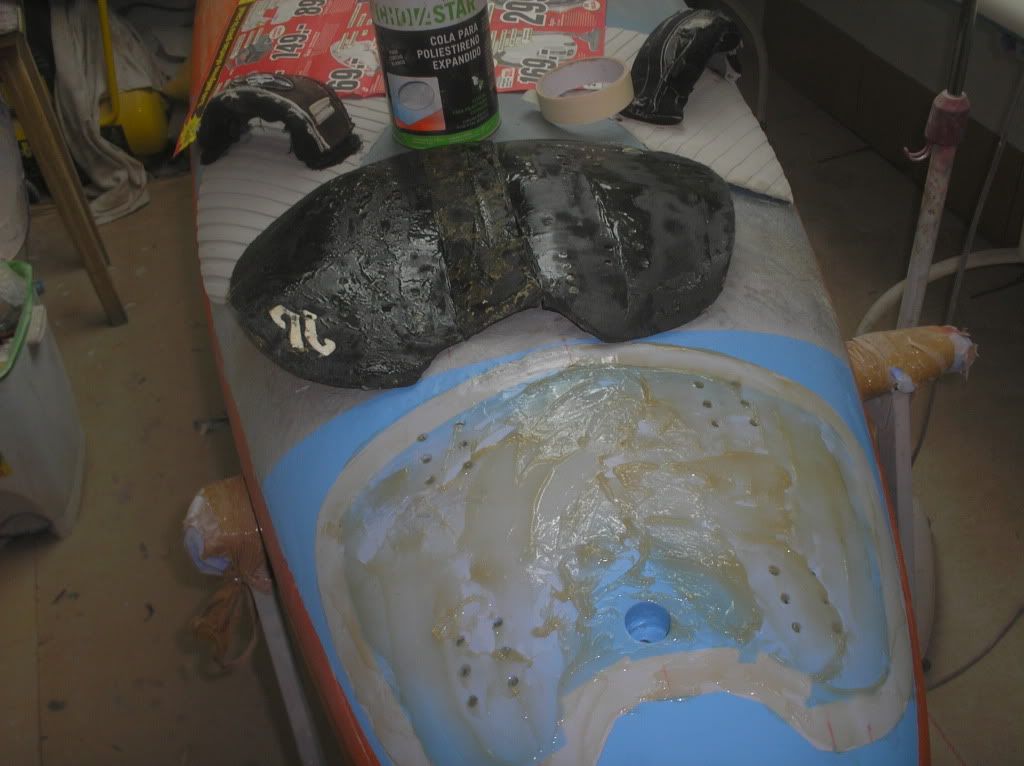
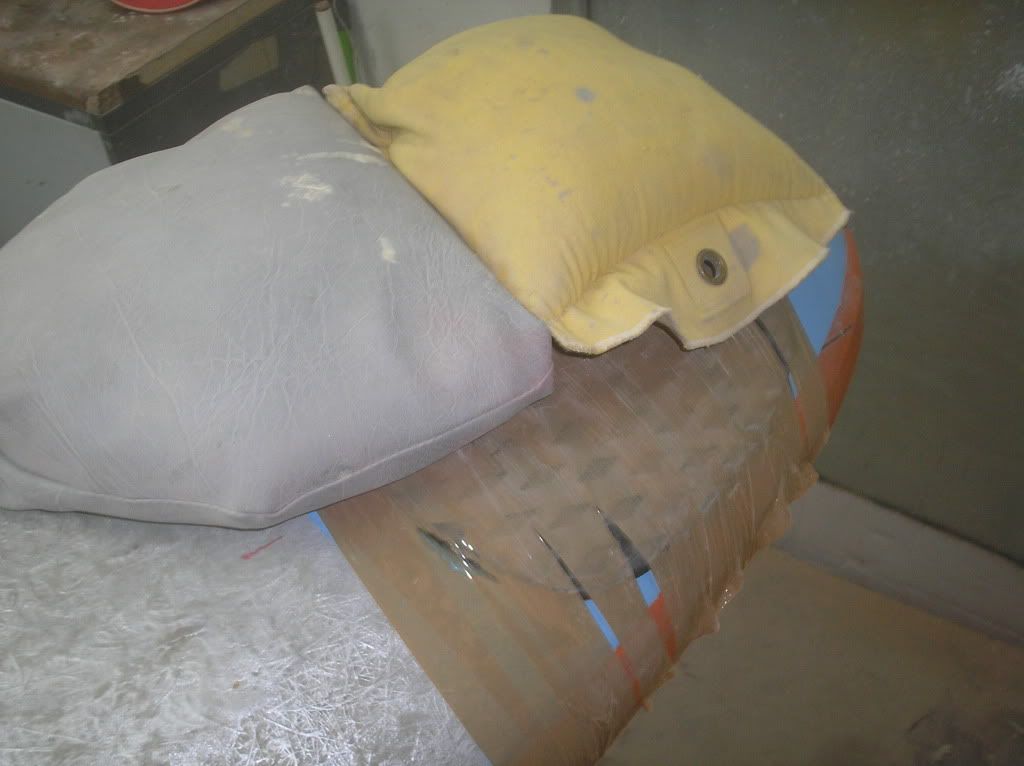
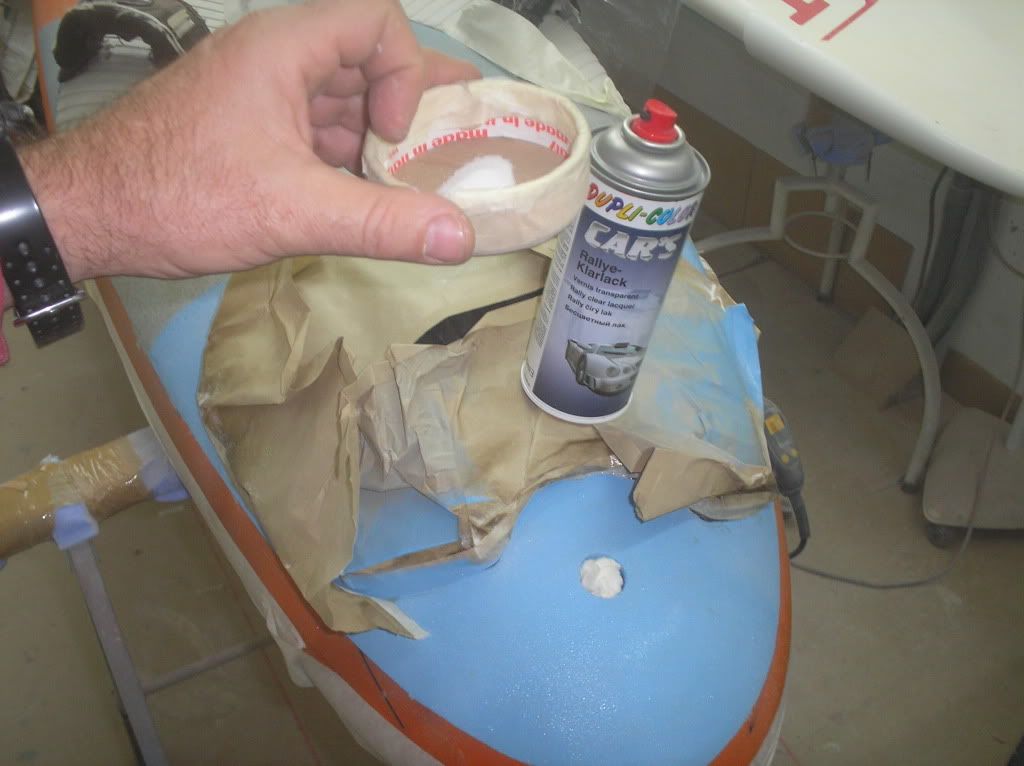
Eliminación del sobrante de laminado en carena con cuter, lijado con orbital, tapado de poro y nivelación con pasta de carrocero, lijado al agua, imprimación, pintura y laca mate.
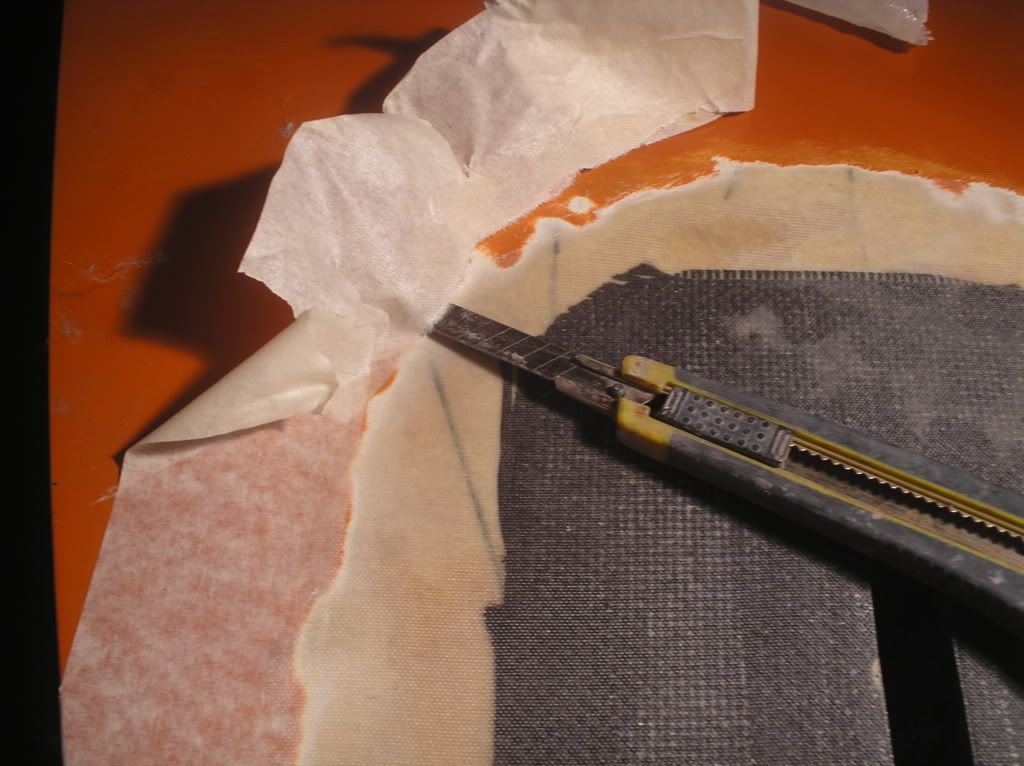
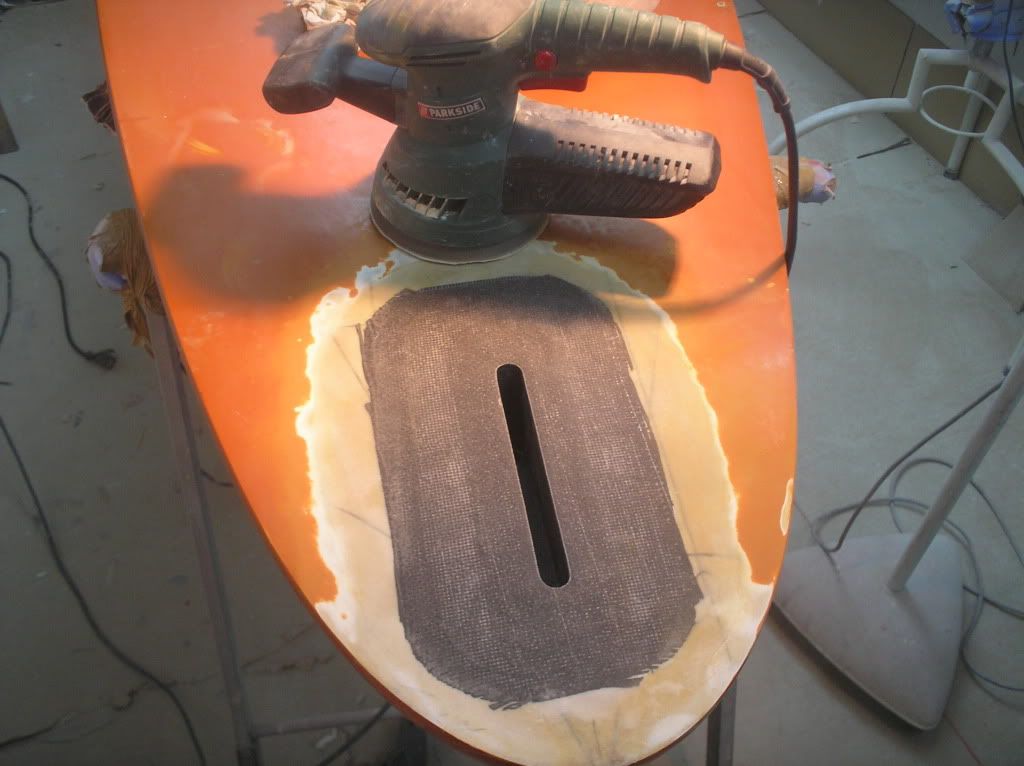
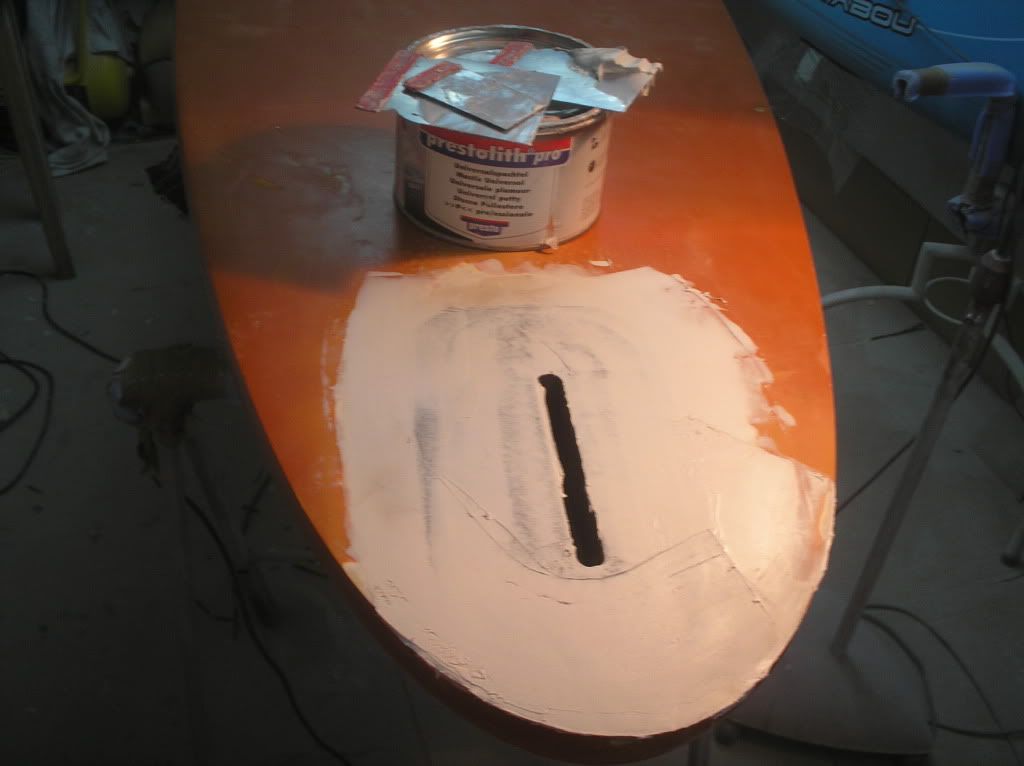
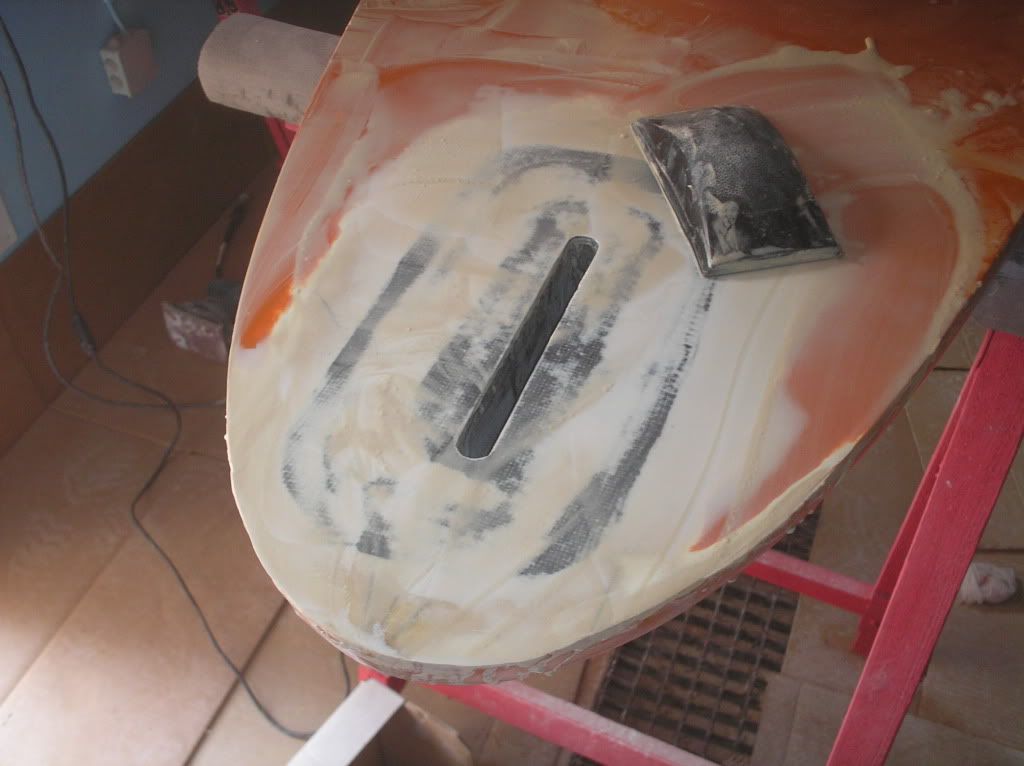
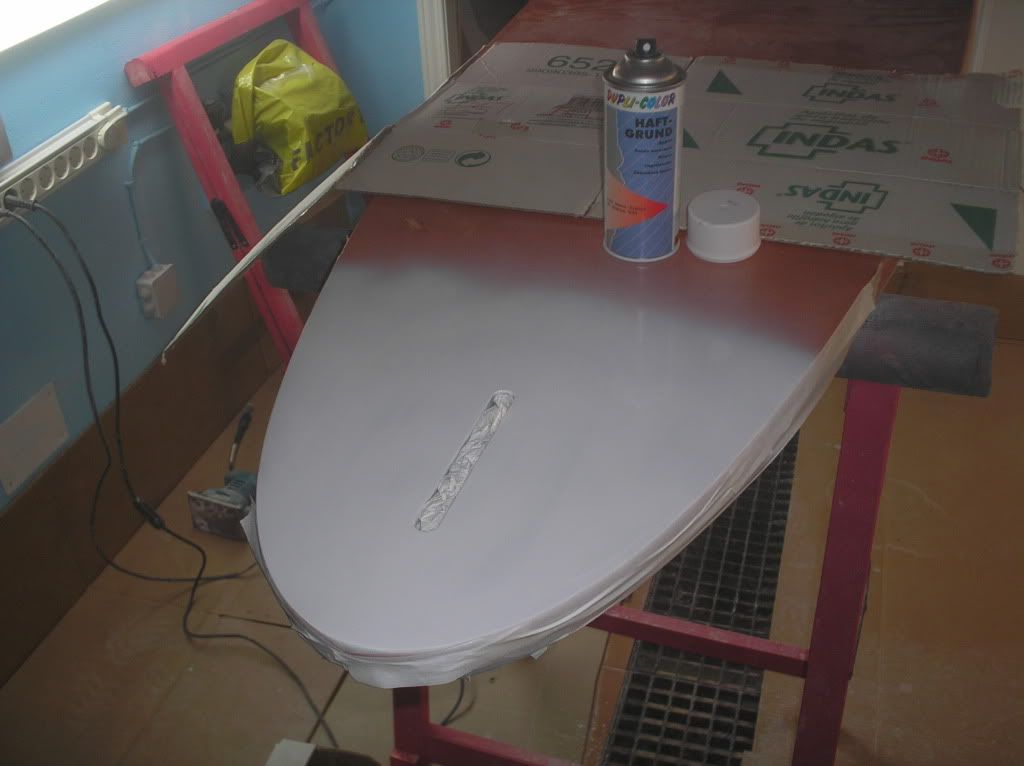
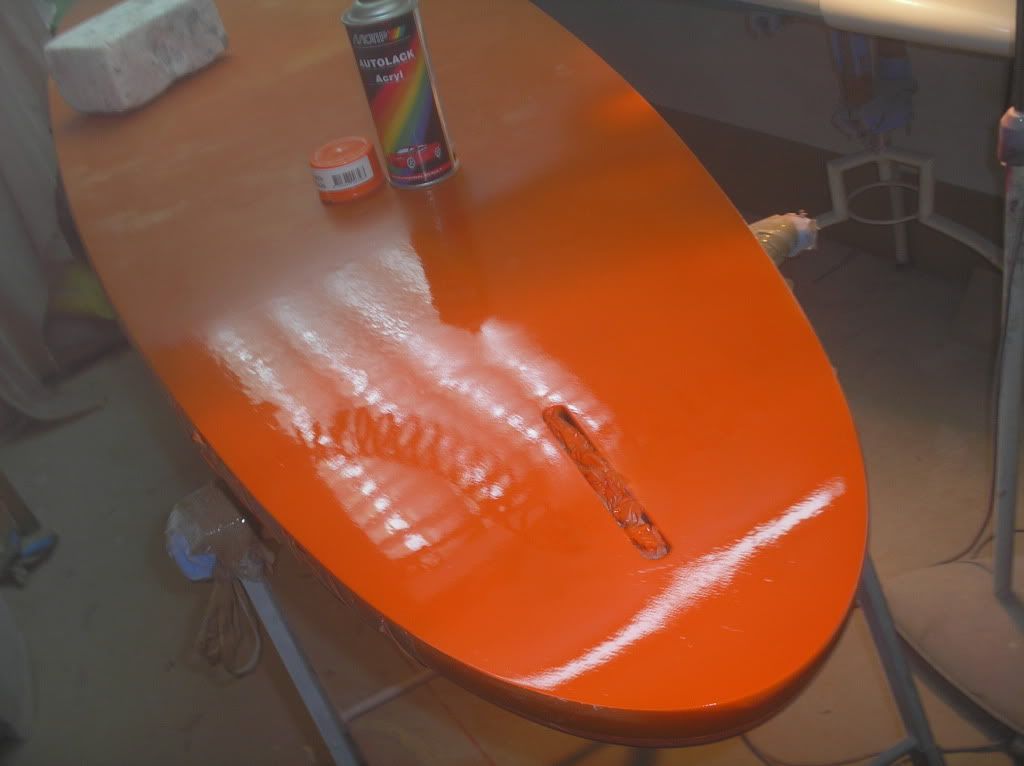
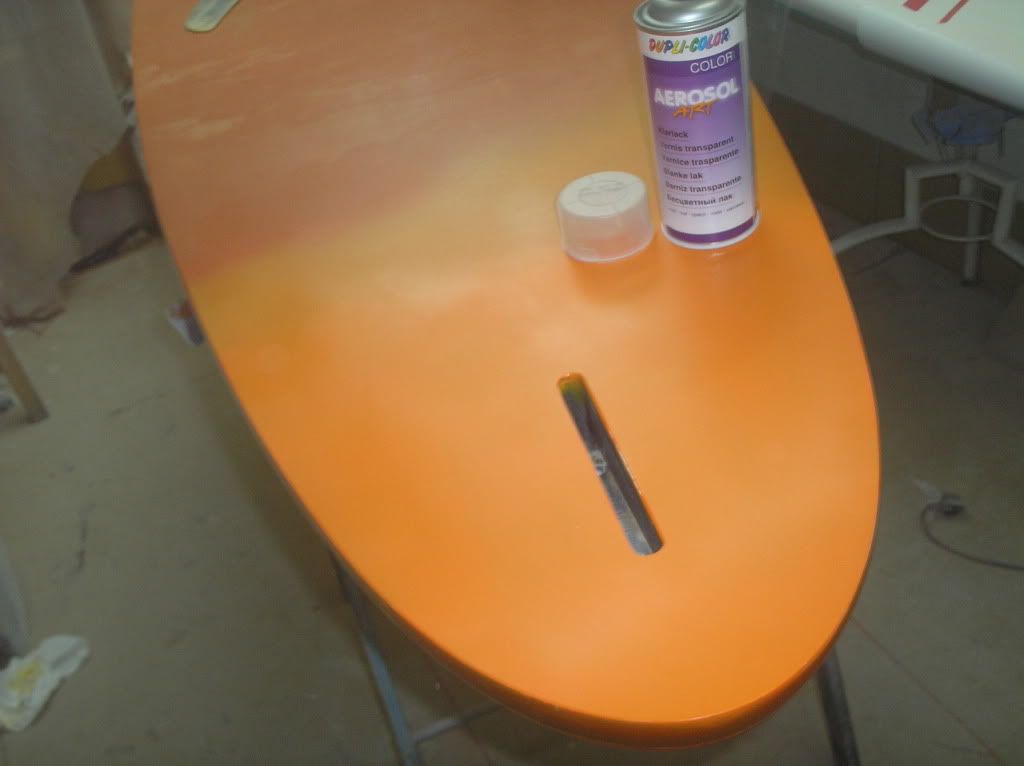
Resultado en cubierta popa
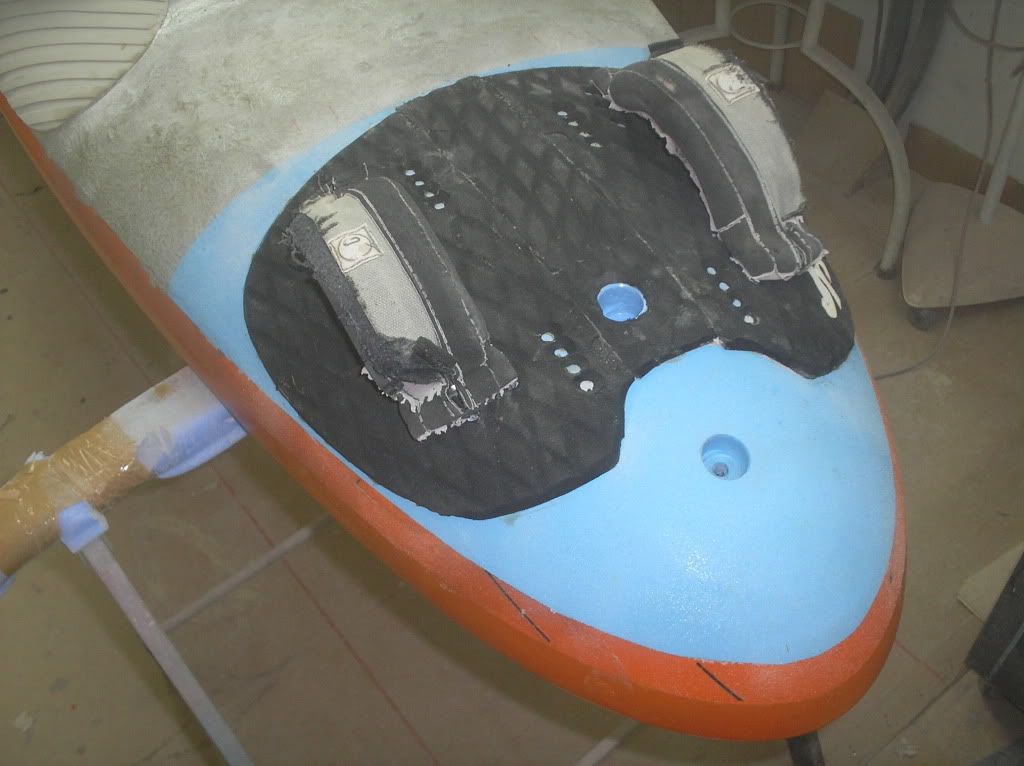
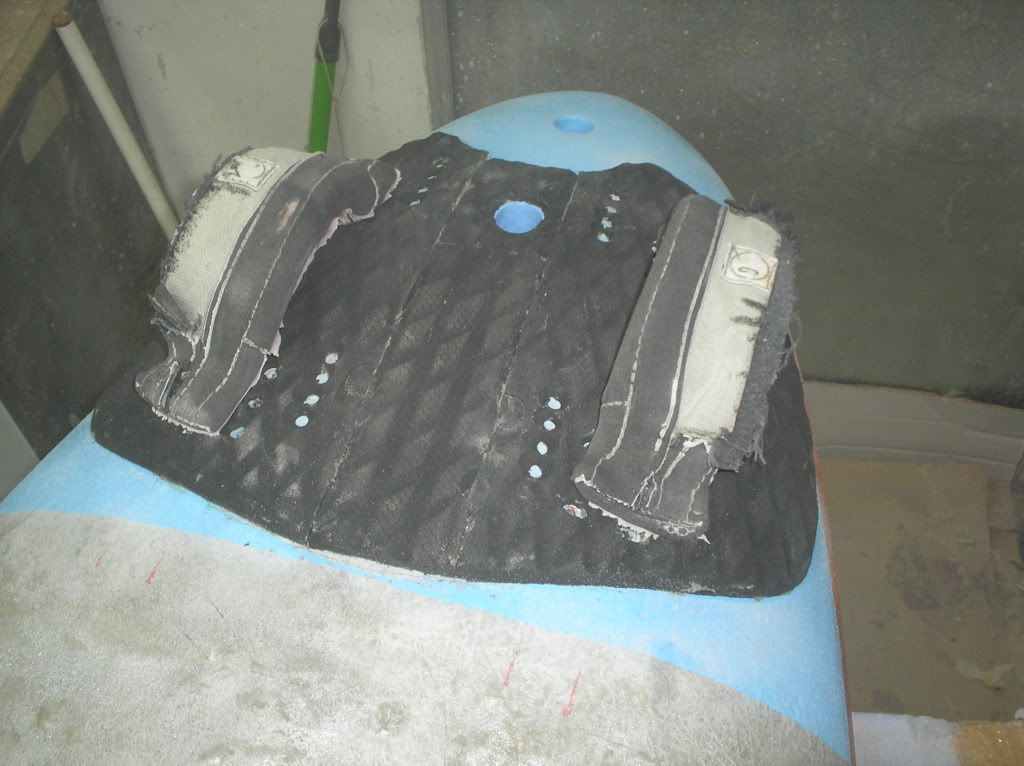
Resultado en carena popa con la aleta insertada quedando a nivel.
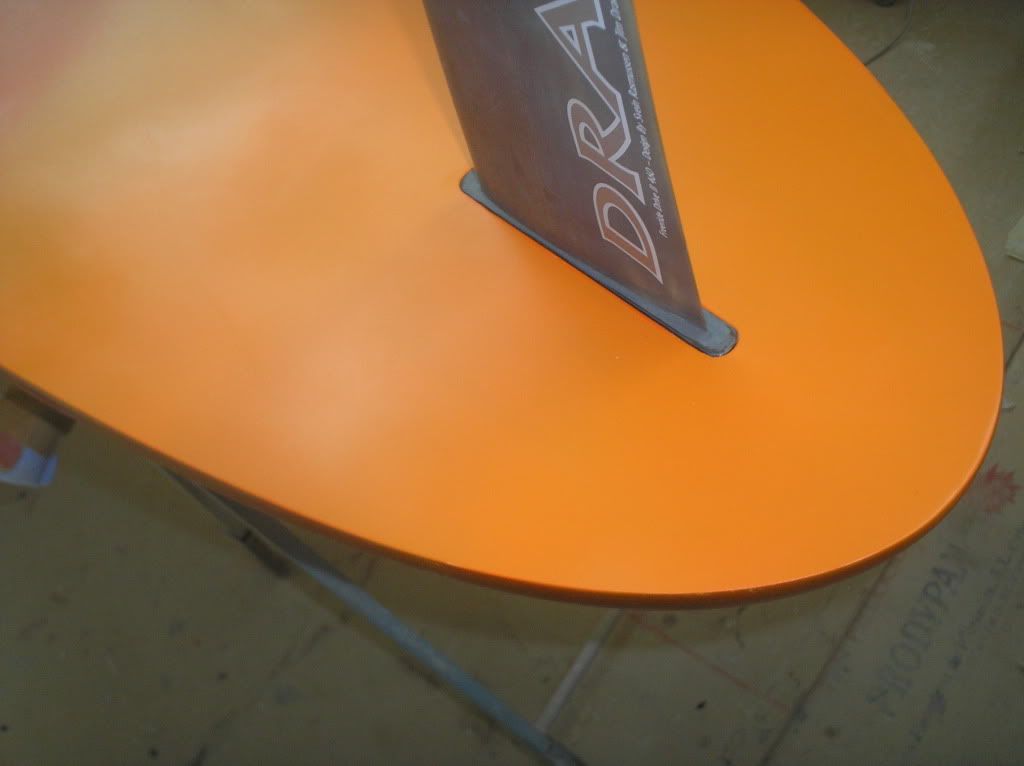
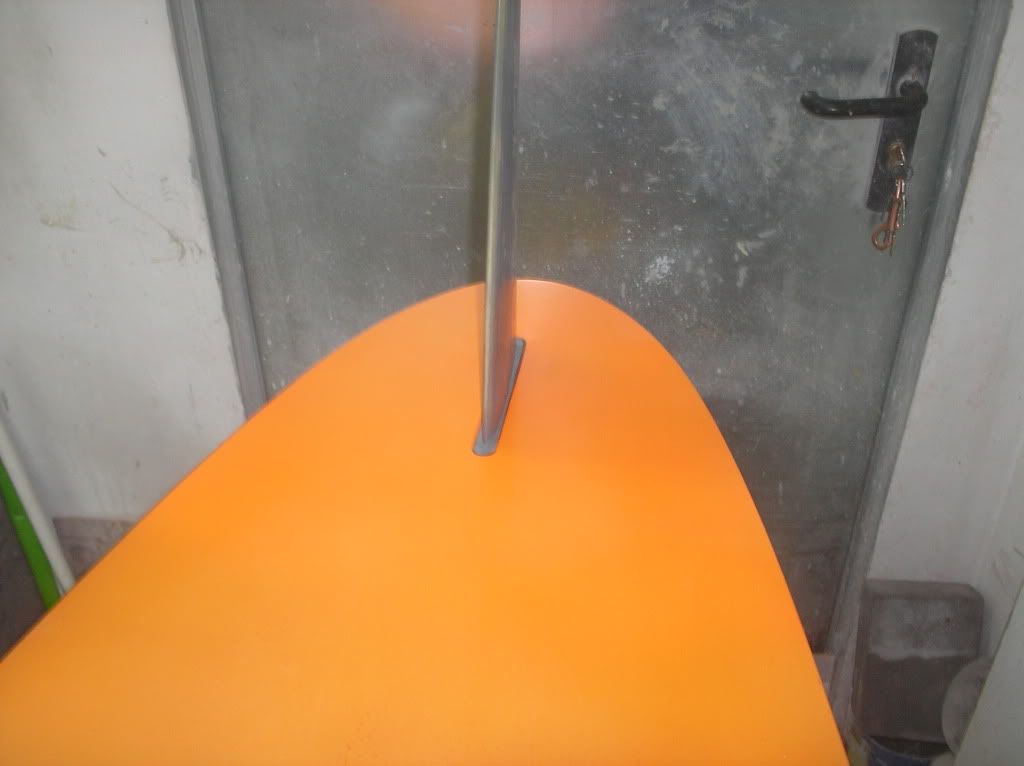
Los tornillos son mas largos ya que la caja es mas alta
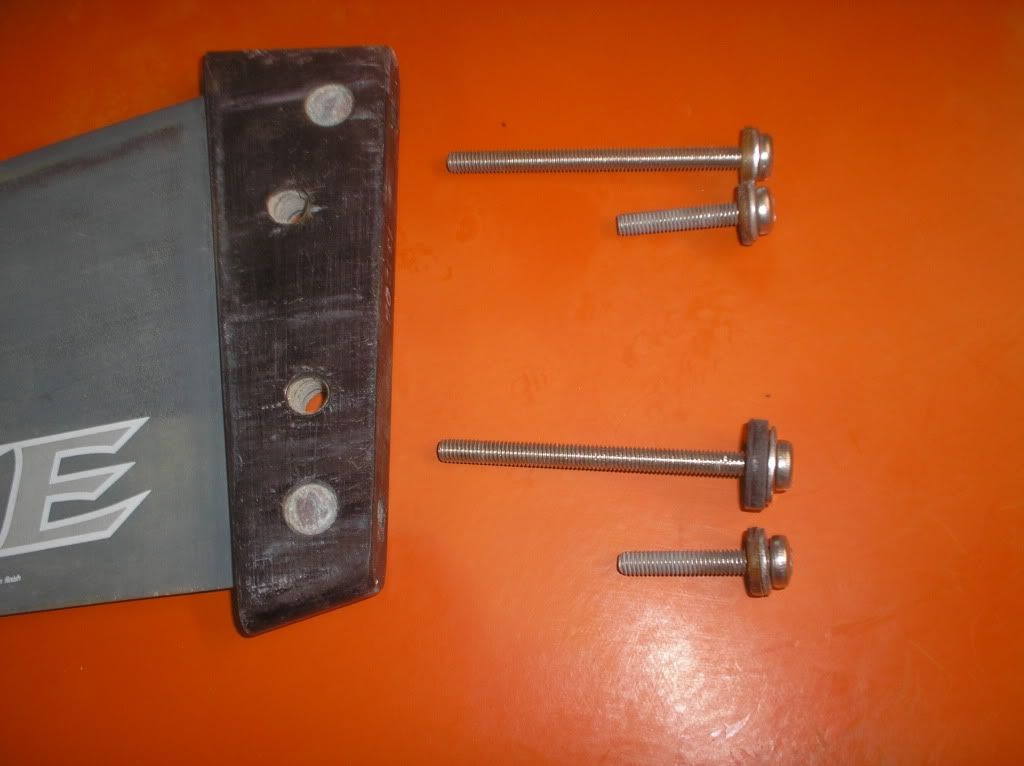