Hace unos dias la he terminado. El outline es similar al de la RRD Freestyle wave 96 y el rocker de diseño propio. Mide 237 x 63 x 11,7 cm. Lo de los 98 L es una suposicion, pero lo más probable es que esté entre 95 y 100 litros. El peso sin aletas ni straps 7,5 kg.
Aqui van fotos y comentarios del proceso, por si puede serle util a alguien. Vamos por partes:
1. Plantillas de contrachapado de 5 mm (dos del perfil i medio outline). No utilizo ningun programa para dibujar e imprimir las plantillas. Utilizo un proyector para dibujar sobre papel continuo la forma a tamaño real. Después termino bien las lineas, sobre una mesa, con ayuda de unos sables y pesas para que las curvas salgan perfectas.
Es muy importante que el contorno curvo de las plantillas sea perfecto y que los dos perfiles sean exactamente iguales.
Es mejor que la longitud de los perfiles sea mayor que la eslora de la tabla, para que sobresalgan por los dos extremos del bloque de eps, facilitando la entrada y salida del hilo caliente para cortar.
2. Corte del eps con hilo caliente. Si el bloque de eps es irregular, es decir que las caras no son exactamente paralelas, hay que asegurarse que los planos de corte sean paralelos y perpendiculares a las plantillas del perfil, a lo largo de todo el bloque. Para ello, situé las plantillas midiendo a partir de dos reglas paralelas situadas encima del bloque. El eps es de 20 g/l
3. Forma de la carena. En este caso v plana en unos 3/4 de la carena hasta popa.
Para formar la v corto con hilo caliente deslizandolo, en un costado sobre la plantilla del perfil un poco desplazada, y cerca del centro de la carena sobre la parte recta de la plantilla del medio outline. Después se afina la forma con surform i rejilla o papel de lija.
4. Primer laminado y pegado del pvc de carena. Primero corto el outline +2 cm en el eps. Después corto una capa de fibra de vidrio hueca de 160g con la forma del outline +2 cm y la misma forma +1 cm de lámina de espuma de pvc de 5 mm, de densidad 100 g/l
Lamino la fibra con resina epoxi directamente sobre el eps. Impregno con espátula una cara del pvc con epoxi espesado con sílice y microbalones y lo situo encima de la fibra. Bloqueo con cinta de pintor. Situo el contrascoop por la parte del puente, para no marcar la carena. Embolsado y vacio a -0,3 atm durante 18 h
El contrascoop es una regla de aluminio con una tira de xps con la forma del puente, sujeta con cinta de pintor.
5. Forma de cantos y cubierta. Primero dibujo y cotro el outline definitivo. Después dibujo la linea que delimita la entrada del canto en la carena y también la linea que corresponde a la manga máxima. Las herramientas utilizadas aparecen en la foto.
6. Insertar bloque de refuerzo para la caja del mástil. Hecho con piezas de pvc de 5 mm pegadas con epoxi espesado (no tenia de mas grosor). Empiezo el hueco fresando con una fresa normal y termino profundizando con una broca para madera montada en la fresadora. Inserto el taco envuelto en una capa de fibra de vidrio hueca 160 g, con epoxi espesado con microbalones, tambien hay una capa de fibra de vidrio hueca bajo la última capa de pvc.
Dejo curar con peso encima.
Continuará.
Aqui van fotos y comentarios del proceso, por si puede serle util a alguien. Vamos por partes:
1. Plantillas de contrachapado de 5 mm (dos del perfil i medio outline). No utilizo ningun programa para dibujar e imprimir las plantillas. Utilizo un proyector para dibujar sobre papel continuo la forma a tamaño real. Después termino bien las lineas, sobre una mesa, con ayuda de unos sables y pesas para que las curvas salgan perfectas.
Es muy importante que el contorno curvo de las plantillas sea perfecto y que los dos perfiles sean exactamente iguales.
Es mejor que la longitud de los perfiles sea mayor que la eslora de la tabla, para que sobresalgan por los dos extremos del bloque de eps, facilitando la entrada y salida del hilo caliente para cortar.

2. Corte del eps con hilo caliente. Si el bloque de eps es irregular, es decir que las caras no son exactamente paralelas, hay que asegurarse que los planos de corte sean paralelos y perpendiculares a las plantillas del perfil, a lo largo de todo el bloque. Para ello, situé las plantillas midiendo a partir de dos reglas paralelas situadas encima del bloque. El eps es de 20 g/l
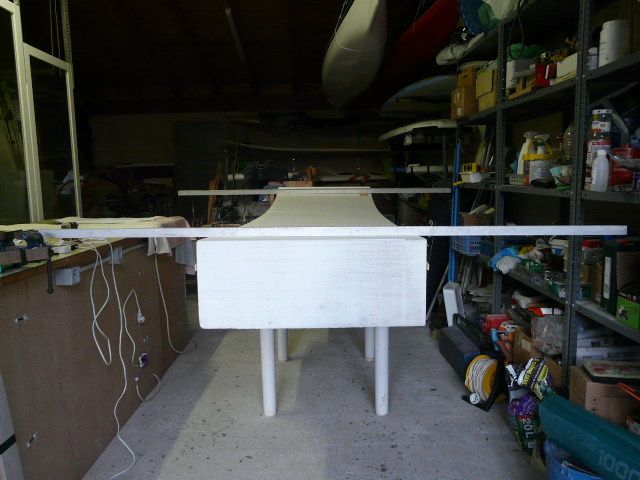
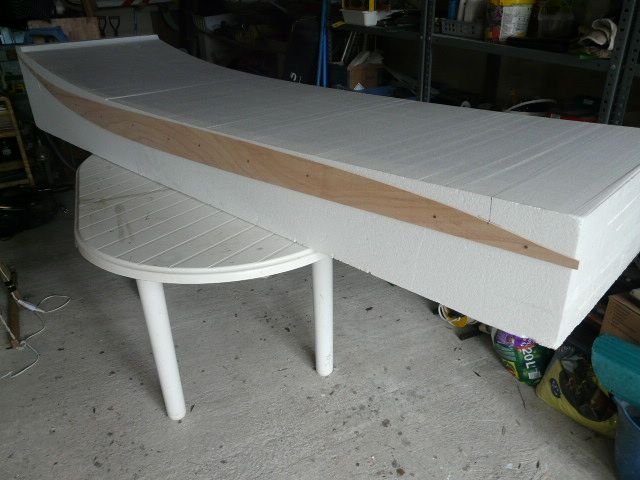
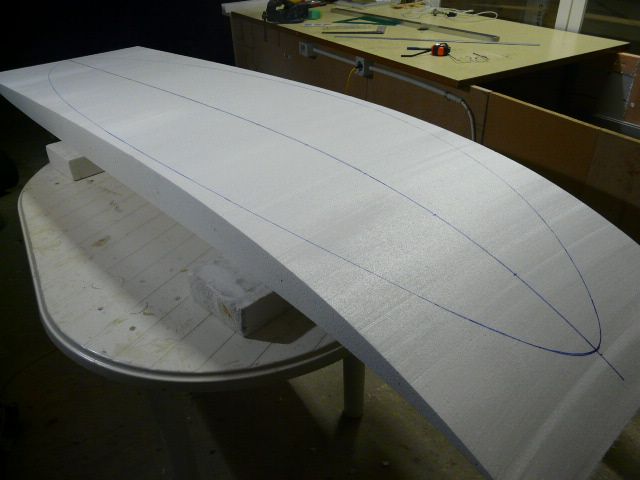
3. Forma de la carena. En este caso v plana en unos 3/4 de la carena hasta popa.
Para formar la v corto con hilo caliente deslizandolo, en un costado sobre la plantilla del perfil un poco desplazada, y cerca del centro de la carena sobre la parte recta de la plantilla del medio outline. Después se afina la forma con surform i rejilla o papel de lija.
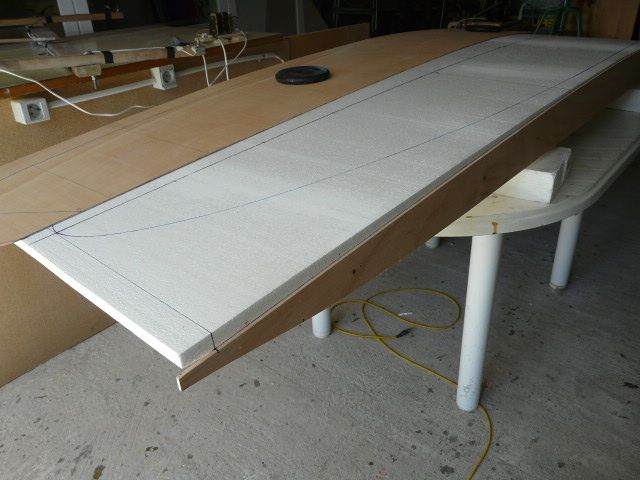
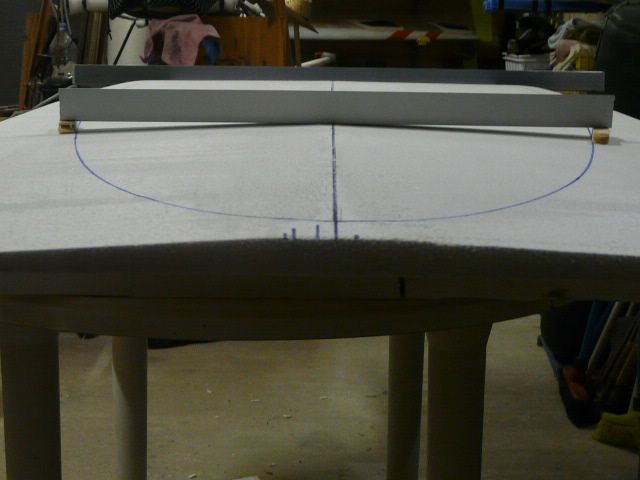
4. Primer laminado y pegado del pvc de carena. Primero corto el outline +2 cm en el eps. Después corto una capa de fibra de vidrio hueca de 160g con la forma del outline +2 cm y la misma forma +1 cm de lámina de espuma de pvc de 5 mm, de densidad 100 g/l
Lamino la fibra con resina epoxi directamente sobre el eps. Impregno con espátula una cara del pvc con epoxi espesado con sílice y microbalones y lo situo encima de la fibra. Bloqueo con cinta de pintor. Situo el contrascoop por la parte del puente, para no marcar la carena. Embolsado y vacio a -0,3 atm durante 18 h
El contrascoop es una regla de aluminio con una tira de xps con la forma del puente, sujeta con cinta de pintor.
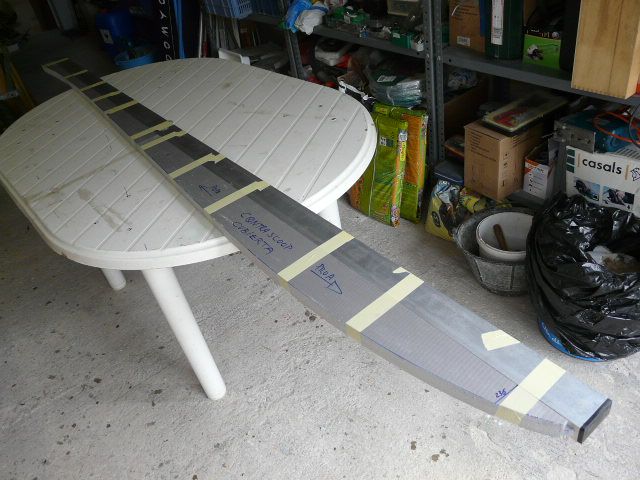
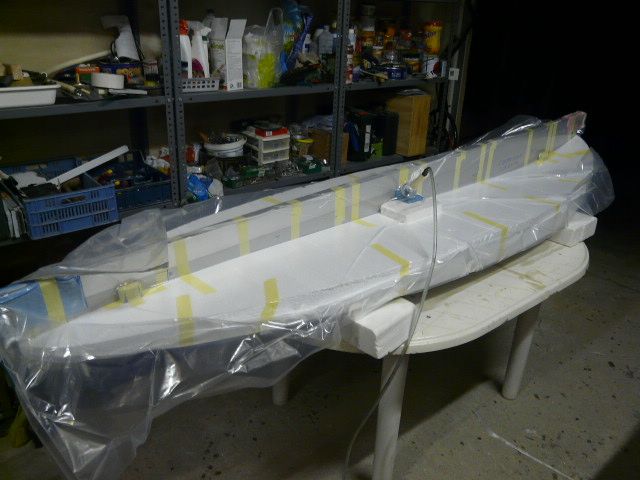
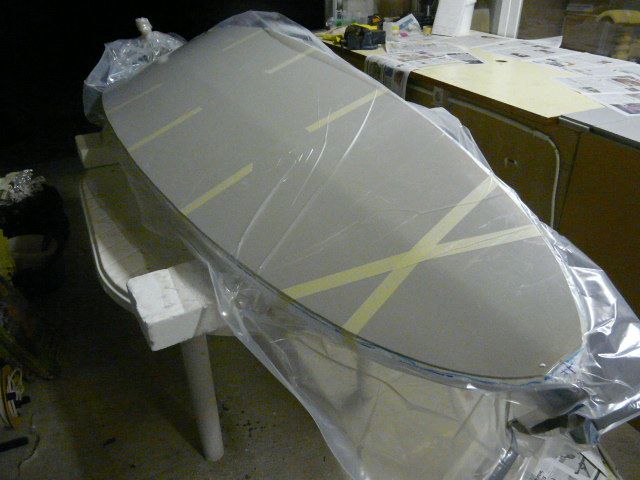
5. Forma de cantos y cubierta. Primero dibujo y cotro el outline definitivo. Después dibujo la linea que delimita la entrada del canto en la carena y también la linea que corresponde a la manga máxima. Las herramientas utilizadas aparecen en la foto.
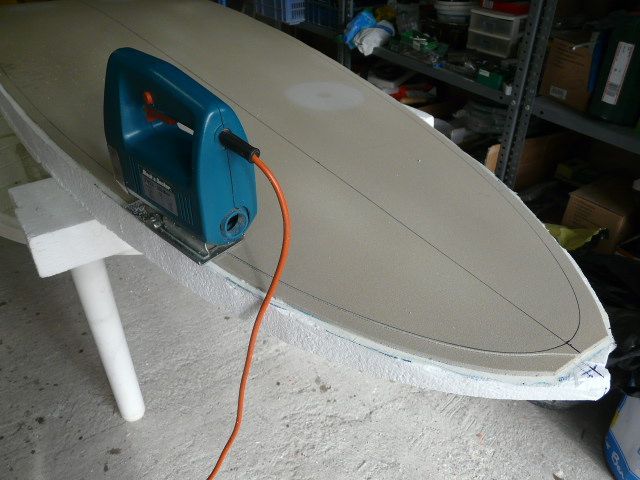
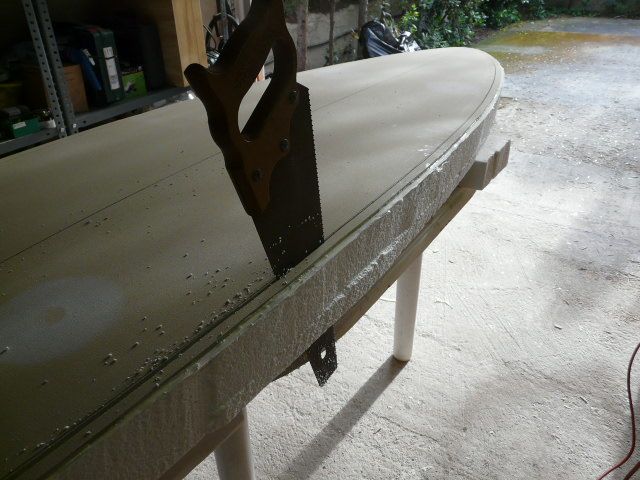
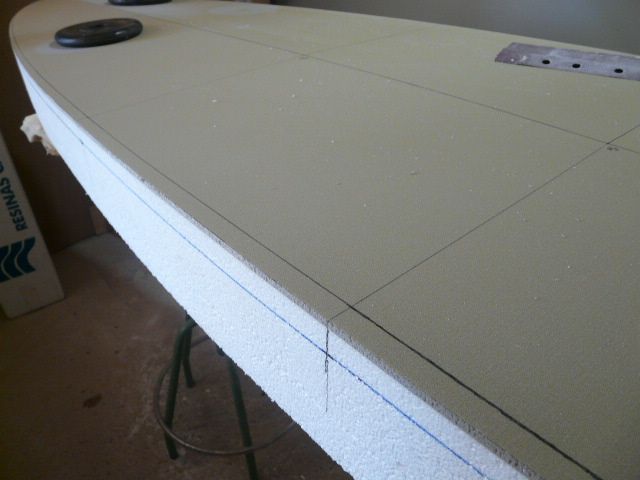
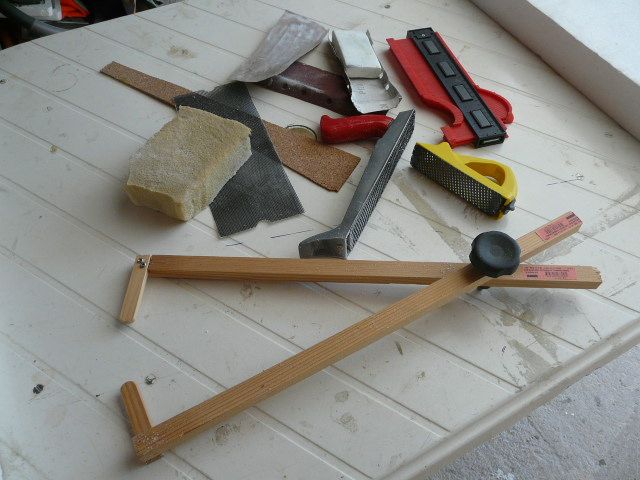
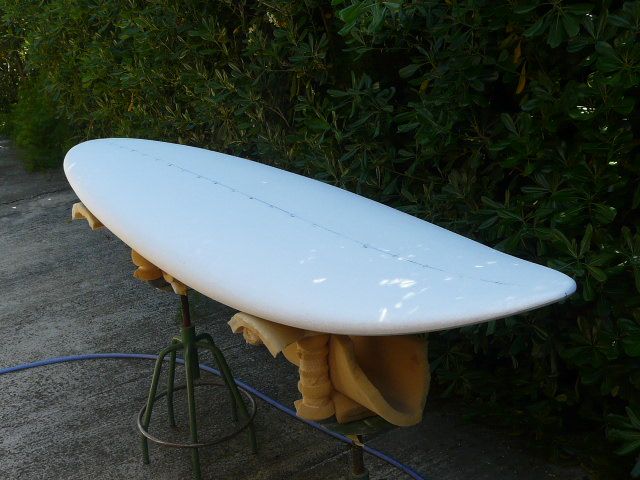
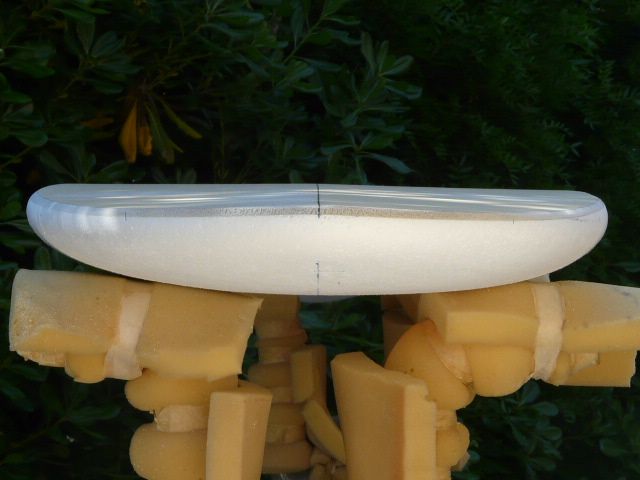
6. Insertar bloque de refuerzo para la caja del mástil. Hecho con piezas de pvc de 5 mm pegadas con epoxi espesado (no tenia de mas grosor). Empiezo el hueco fresando con una fresa normal y termino profundizando con una broca para madera montada en la fresadora. Inserto el taco envuelto en una capa de fibra de vidrio hueca 160 g, con epoxi espesado con microbalones, tambien hay una capa de fibra de vidrio hueca bajo la última capa de pvc.
Dejo curar con peso encima.
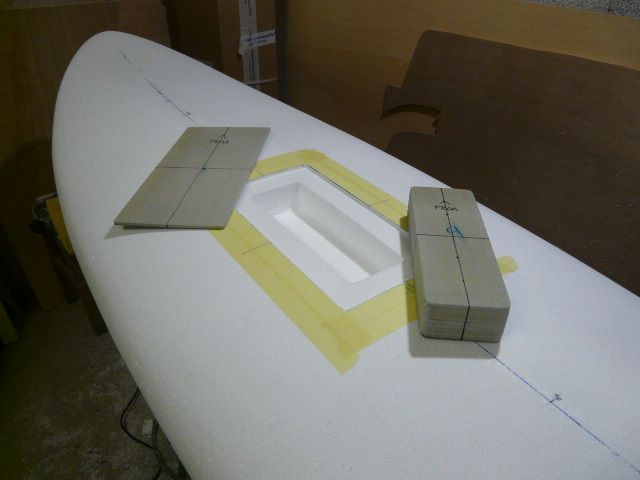
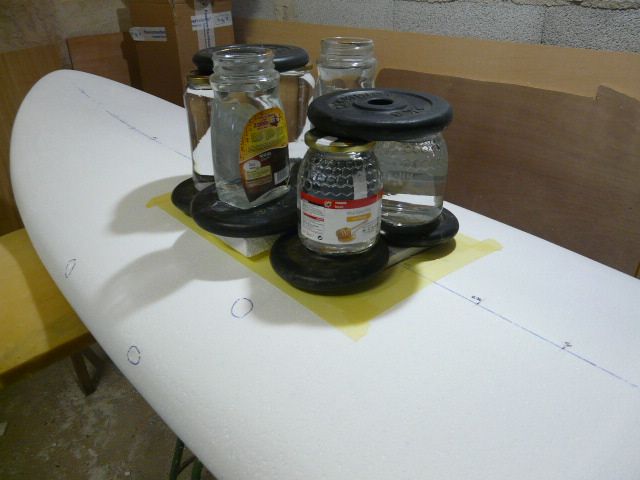
Continuará.